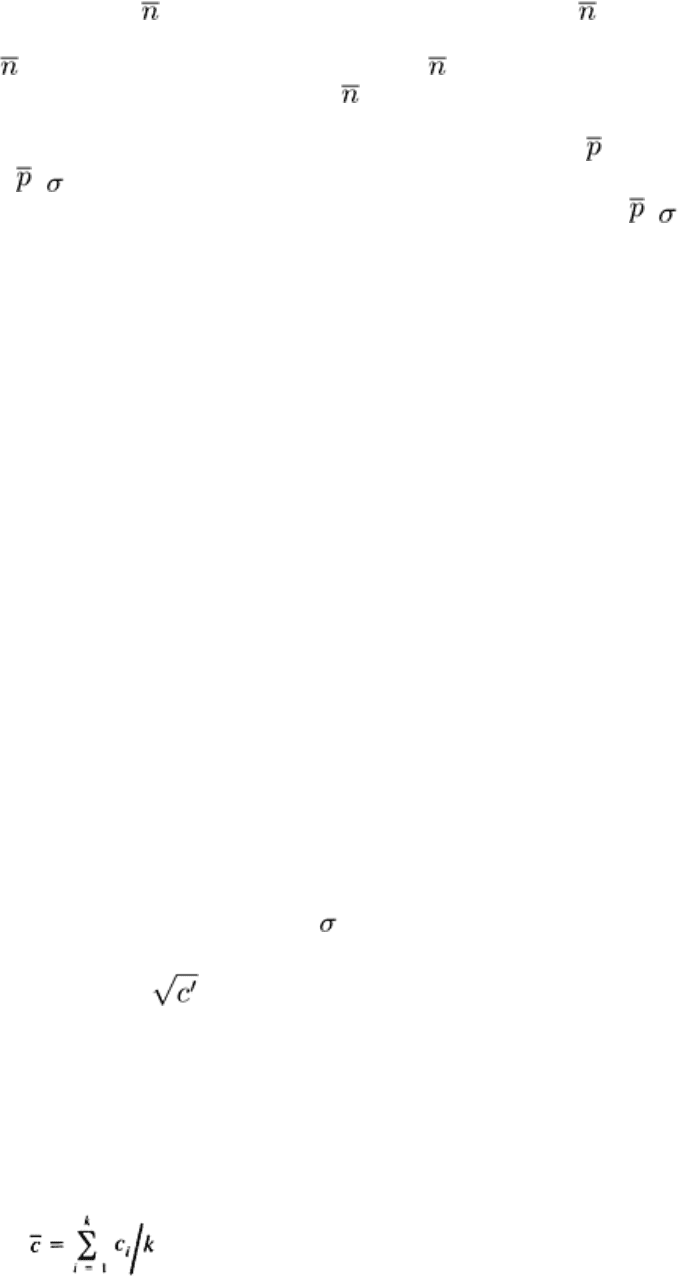
100% inspection) and production rates vary from day to day. Because the limits on a p-chart depend on the sample size n,
some adjustments must be made to ensure that the chart is properly interpreted. There are several ways in which the
variable sample size problem can be handled. Some of the more common approaches are the following:
• Compute separate limits for each individual subgroup. This approach certainly
leads to a correct set of
limits for each sample, but requires continual calculation of the control limits and a somewhat messy-
looking control chart
• Determine an average sample size, , and a single set of control limits based on
appropriate if the sample sizes do
not vary greatly, perhaps no more than about 20%. However, if the
actual n is less than , a point above the control limit based on
may not be above its own true upper
control limit. Conversely, if the actual n is greater than
, a point may not show out of control when in
reality it is
• A third procedure for varying sampling size is to express the fraction defective
units, that is, plot (p - )/
p
on a control chart where the centerline is zero and the control limits are set
at ±3.0. This stabilizes the plotted value even though n may be varying. Note that (p - )/
p
form; recall the standard normal (Z
) distribution. For this method, the continued calculation of the
stabilized variable is somewhat tedious, but the chart has a clean appearance, with constant limits of
always ±3.0 and constant centerline at 0.0
c-Chart: A Control Chart for Number of Defects
The p-chart deals with the notion of a defective part or item where defective means that the part has at least one
nonconformity or disqualifying defect. It must be recognized, however, that the incidence of any one of several possible
nonconformities would qualify a part for defective status. A part with ten defects, any one of which makes it a defective,
is on equal footing with a part with only one defect in terms of being a defective.
Often it is of interest to note every occurrence of every type of defect on a part and to chart the number of defects per
sample. A sample may only be one part, particularly if interest is focusing on final inspection of an assembled product,
such as an automobile, a lift truck, or perhaps a washing machine. Inspection may focus on one type of defect (such as
nonconforming rivets on an aircraft wing) or multiple defects (such as flash, splay, voids, and knit lines on an injection-
molded truck grille).
Considering an assembled product such as a lift truck, the opportunity for the occurrence of a defect is quite large,
perhaps to be considered infinite. However, the probability occurrence of a defect in any one spot arbitrarily chosen is
probably very, very small. In this case, the probability law that governs the incidence of defects is known as the Poisson
law or Poisson probability distribution, where c is the number of defects per sample. It is important that the opportunity
space for defects to occur be constant from sample to sample. The Poisson distribution defines the probability of
observing c defects in a sample where c' is the average rate of occurrence of defects per sample.
Construction of c-Charts From Sample Data. The number of defects, c, arises probabilistically according to the
Poisson distribution. One important property of the Poisson distribution is that the mean and variance are the same value.
Then given c', the true average number of defects per sample, the 3 limits for the c-chart are given by:
CL
c
= c' ± 3
(Eq 5)
Note that the standard deviation of the observed quantity c is the square root of c'. The Poisson distribution is a very
simple probability model, being completely described by a single parameter c'.
When c' is unknown, it must be estimated from the data. For a collection of k samples, each with an observed number of
defects c, the estimate of c' is:
(Eq 6)