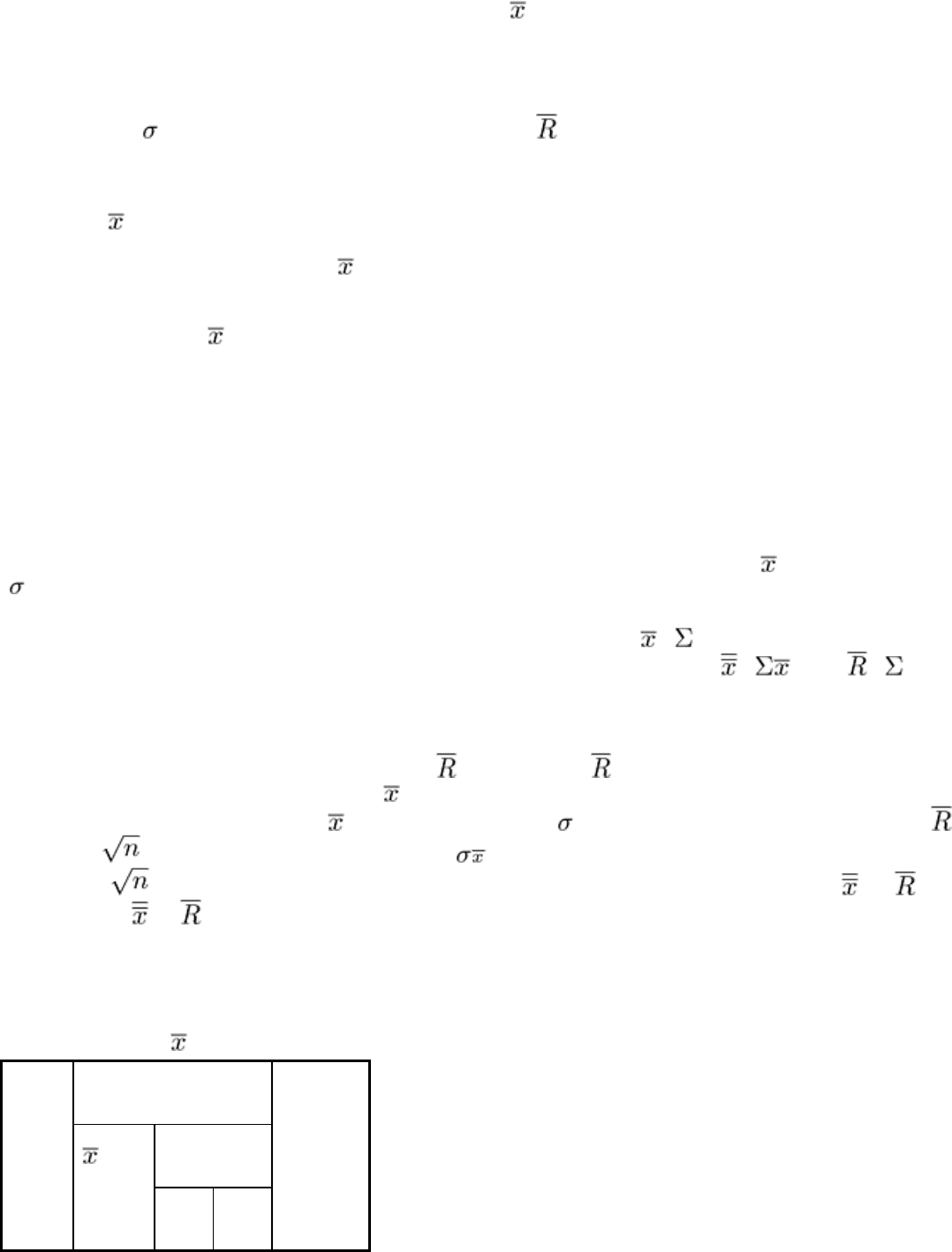
to aid in determining when a change in the mean level has occurred. By determining the range, R, for each sample and
tracking its behavior over time, a basis is provided for identifying the presence of changes in process variability.
Establishing a control chart for ranges R comparable to the -chart requires more specific information about the
distribution of the process. In particular, it will be assumed that the individual measurements x are normally distributed.
Doing so establishes the relationship between the standard deviation of ranges R and the standard deviation of individual
process observations or measurements.
For simplicity, ±3
R
limits will be placed about the average range to define the upper and lower control limits for R
even though the frequency distribution of ranges is not a symmetric distribution. Obtaining σ
R
will be discussed later in
this article.
Setting Up and R Control Charts. Once the statistical basis for Shewhart control charts has been established, it
remains to define the necessary elements of the charts mathematically and to establish a standard graphical representation.
This section deals with the construction of and R control charts. All the necessary equations and general procedures for
the calculation and graphical representation of the basic elements of the charts are presented in this section.
The first step in setting up and R control charts is the selection of the samples. It is important that all samples be rational
samples. Rational samples are groups of measurements whose variation is attributable only to one constant system of
common cause. Sampling from different machines, sampling over extended periods of time, and sampling from product
combined from several sources are all nonrational sampling methods and must be avoided. Rational samples will be
discussed in more detail later in this article.
As a rule of thumb, 25 to 50 samples should be selected to provide a solid basis for the initiation of the control charts.
This will help to ensure more precise estimation of the process mean and standard deviation. The sample/subgroup size
should be relatively small (between n = 3 and n = 6).
With k rational samples of n each, the following steps can be used as a guide when constructing , R control charts with
3 limits:
• Calculate the sample mean and sample range for each sample using = x/n and R = x
max
- x
min
• Calculate the grand mean of the n sample means and the average range using = /k and = R/k
• Calculate the control limits for the R-
chart. Although the true distribution of sample ranges is not
normal and not symmetric, the symmetric limits are conventionally used for the R-
normal distribution for the individua
l measurements, the following formulas can be used for the
calculation of the control limits: UCL
R
= D
4
and LCL
R
= D
3
• Calculate the control limits for the -chart. Although the
required standard deviation (the standard
deviation of the sample mean, ) for setting the limits is
x
, this value is conveniently estimated by
/(d
2
), where d
2
is a function of n. For 3 limits, one uses a factor called A
2
3/(d
2
) and can be found in Table 1. Thus, the control limits are calculated by: UCL
x
= + A
2
LCL
x
= - A
2
The appropriate values for d
2
, A
2
, D
3
, and D
4
are obtained from Table 1.
Table 1 Factors for and R control chart limits
Factors for control limits
R-chart
Sample
size, n
-chart
A
2
D
3
D
4
Factor for
calculating
σ
x
from
range, R
d
2