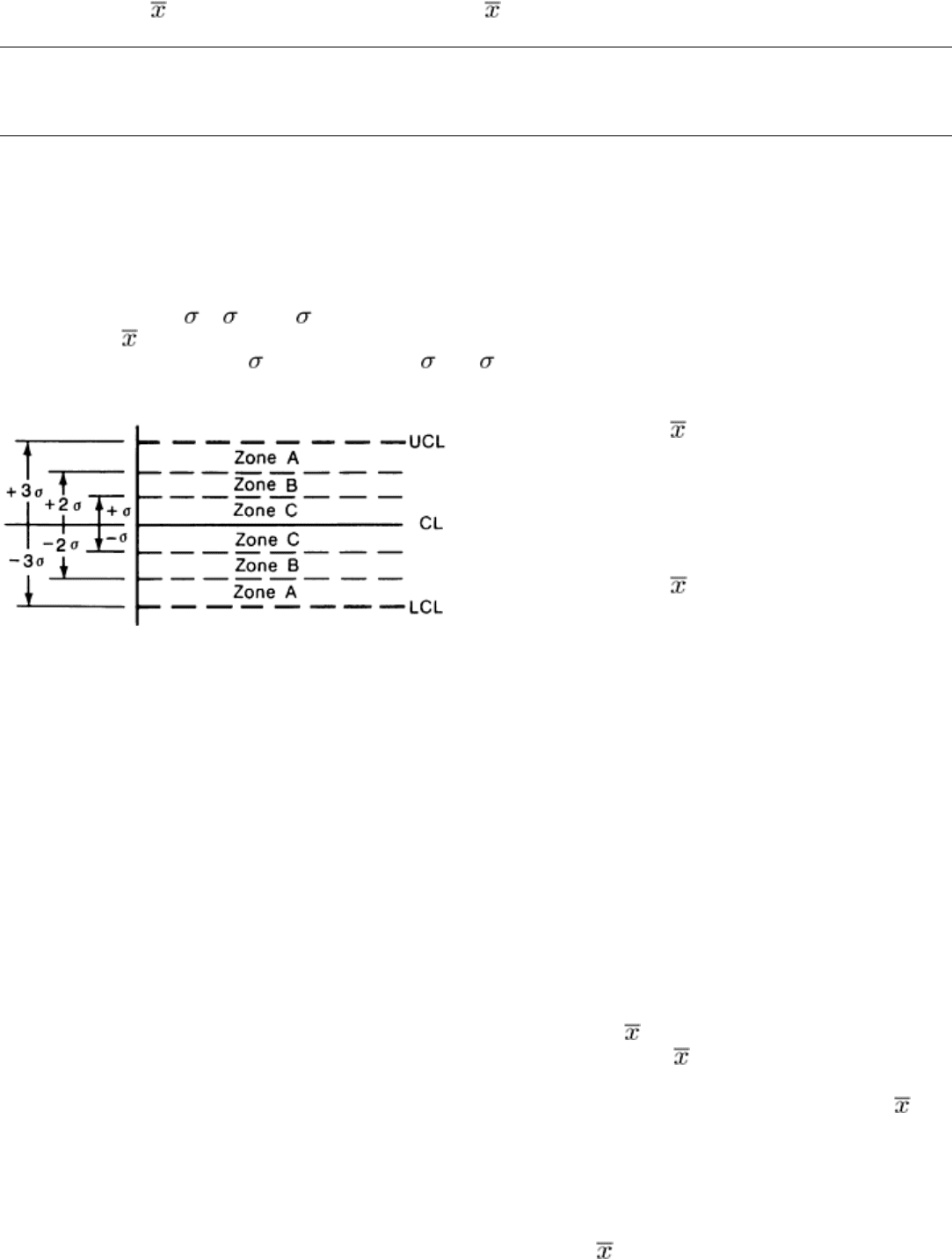
from all machines, the within-sample variability will be too low, and the between-sample differences in the means tend to
be large. Thus, the -chart would give an appearance that the values are too far away from the centerline.
Statistical Quality Design and Control
Richard E. DeVor, University of Illinois, Urbana-Champaign; Tsong-how Chang, University of Wisconsin, Milwaukee
Zone Rules for Control Chart Analysis
Special causes often produce unnatural patterns that are not as clear cut as points beyond the control limits or obvious
regular patterns. Therefore, a more rigorous pattern analysis should be conducted. Several useful tests for the presence of
unnatural patterns (special causes) can be performed by dividing the distance between the upper and lower control limits
into zones defined by , 2 , and 3 boundaries, as shown in Fig. 22. Such zones are useful because the statistical
distribution of follows a very predictable pattern--the normal distribution; therefore, certain proportions of the points
are expected to fall within the ± boundary, between and 2 , and so on.
The following sections discuss eight tests that can be applied
to the interpretation of and R control charts. Not all of
these tests follow/use the zones just described, but it is
useful to discuss all of these rules/tests together. These tests
provide the basis for the statistical signals that indicate that
the process has undergone a change in its mean level,
variability level, or both. Some of the tests are based
specifically on the zones defined in Fig. 22 and apply only to
the interpretation of the -chart patterns. Some of the tests
apply to both charts. Unless specifically identified to the
contrary, the tests/rules apply to the consideration of data to
one side of the centerline only.
When a sequence of points on the chart violates one of the
rules, the last point in the sequence is circled. This signifies
that the evidence is now sufficient to suggest that a special cause has occurred. The issue of when that special cause
actually occurred is another matter. A logical estimation of the time of occurrence may be the beginning of the sequence
in question. This is the interpretation that will be used here. It should be noted that some judgment and latitude should be
given. Figure 23 illustrates the following patterns:
• Test 1(extreme points): The existence of a single point beyond zone A signals the presence of an out-of-
control condition (Fig. 23a)
• Test 2 (2 out of 3 points in zone A or beyond):
The existence of 2 out of any 3 successive points in zone
A or beyond signals the presence of an out-of-control condition (Fig. 23b)
• Test 3 (4 out of 5 points in zone B or beyond):
A situation in which there are 4 out of 5 successive points
in zone B or beyond signals the presence of an out-of-control condition (Fig. 23c)
• Test 4 (runs above or below the centerline):
Long runs (7 or more successive points) either strictly
above or strictly below the centerline; this rule applies to both the and R control charts (Fig. 23d)
• Test 5 (trend identification): When 6 successive points on either the or the R co
continuing increase or decrease, a systematic trend in the process is signaled (Fig. 23e)
• Test 6 (trend identification): When 14 successive points oscillate up and down on either the or R
control chart, a systematic trend in the process is signaled (Fig. 23f)
• Test 7 (avoidance of zone C test): When 8 successive points, occurring on either side of the center
avoid zone C, an out-of-
control condition is signaled. This could also be the pattern due to mixed
sampling (discussed earlier), or it could also be signaling the presence of an over-
process (Fig. 23g)
• Test 8 (run in zone C test): When 15 successive points on the -
chart fall in zone C only, to either side
of the centerline, an out-of-
control condition is signaled; such a condition can arise from stratified
Fig. 22 Control chart zones to aid chart interpretation