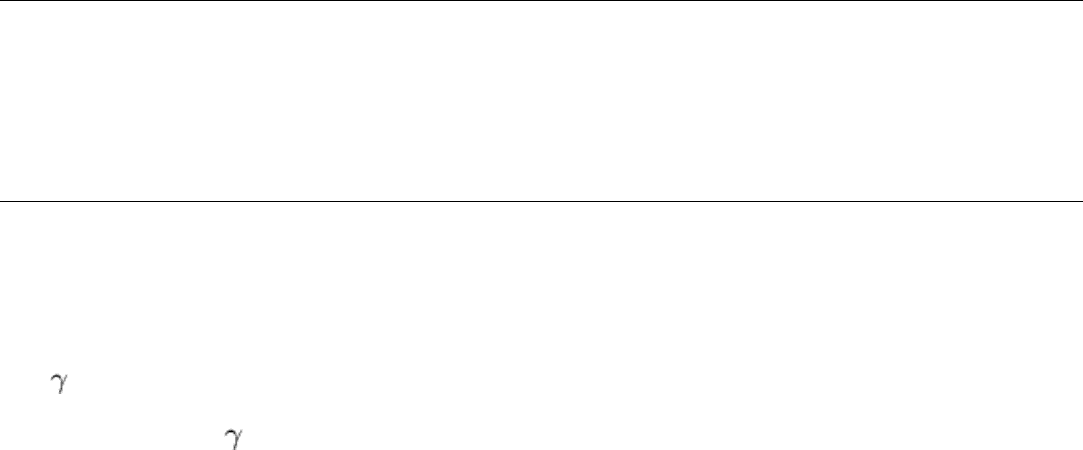
were strapped to identify the hottest zones. Growth to failure in HK-40 material having a rough exterior surface is
difficult to measure, because total creep of only about 1% has occurred by the time of failure. Gaging did not show much,
but strapping on some tubes clearly identified bulging in the hottest areas about 1.4 m (54 in.) above the burner terrace.
This was used as the basis for radiographing all other tubes.
The catalyst was removed from the tubes in preparation for radiography. Two IR-192 radiation sources having a strength
of 3300 GBq (90 Ci) and one 3700 GBq (100 Ci) source were used, mounted in jigs at distances of 750 and 900 mm (30
and 36 in.), respectively, from the film. A tungsten collimator was also used to limit the emission to a single tube and
permit the technicians to remain in the firebox during exposure. Exposure time was 7 to 10 min per shot, and
approximately 700 shots were taken.
Shortly after the first furnace was back on stream, the second furnace was shut down and the tubes radiographed. Using
the same techniques but with a 3900 GBq (105 Ci) source, time to radiograph the second furnace was reduced about 25%.
Twenty-four tubes in the first furnace and 53 in the second furnace showed significant fissuring. One of these fissured
tubes was left in the first furnace and 15 in the second; when these tubes eventually failed, they would provide an
indication of remaining life after a known radiographic examination.
One of the tubes that had been removed from the furnace was sectioned at two places--through a radiographic indication
of a fissure and through an area containing no indications. Macrographs of these sections are shown in Fig. 8(d) and 8(e).
Figure 8(d) shows fissuring that was detected by radiography. Fine fissuring that was not seen on the radiograph is shown
in Fig. 8(e).
Conclusion. Radiography was a practical, economical method of detecting the creep fissuring, and it provided advance
information for purchase of replacement tubes. However, because radiography was limited to detecting fissures caused by
third-stage creep in tubes from which the nickel catalyst had been removed and because of the cost of removing the
catalyst, ultrasonic techniques were developed for inspecting the tubes. These techniques are described in Example 4 in
this article.
Reference cited in this section
14.
R.R. Dalton, Radiographic Inspection of Cast HK-40 Tubes for Creep Fissures, Mater. Eval.,
12), Dec 1972, p 249-253
Nondestructive Inspection of Boilers and Pressure Vessels
Ultrasonic Inspection of Pressure Vessels
Volumetric inspections are used to inspect the volume of material bounded by the surfaces of components and of piping.
Theoretically, any source of energy that penetrates the volume of a material can be used. In practice, however, only x-
rays, -rays, and ultrasonic waves are used. In nuclear vessels, which are housed in a containment building, radiographic
inspection methods for in-service inspection currently have limited use because of the need for access to both surfaces
and because of the high -ray background in most areas of the containment building. When radiography is used, other
inspection methods such as acoustic emission can also be used for additional monitoring. However, a large number of
inspections are performed using various ultrasonic techniques.
As described in the article "Ultrasonic Inspection" in this Volume, ultrasonic waves are generated by piezoelectric
transducers that convert high-frequency electrical signals into mechanical vibrations. These mechanical vibrations form a
wave front, which is coupled to the vessel being inspected through the use of a suitable medium. Several wave modes can
be used for inspection, depending on the orientation and location of the discontinuities that exist. Longitudinal, shear, and
surface waves are used separately in different techniques to reveal discontinuities that are respectively parallel to, at an
angle to, and on or near the surface from which the inspection is performed. These inspections are made with longitudinal
wave transducers, pulse-echo, through transmission, pitch-catch, or delta techniques. Most of the inspections are
performed using pulse-echo straight longitudinal wave beams and angled shear wave beams from a single transducer.