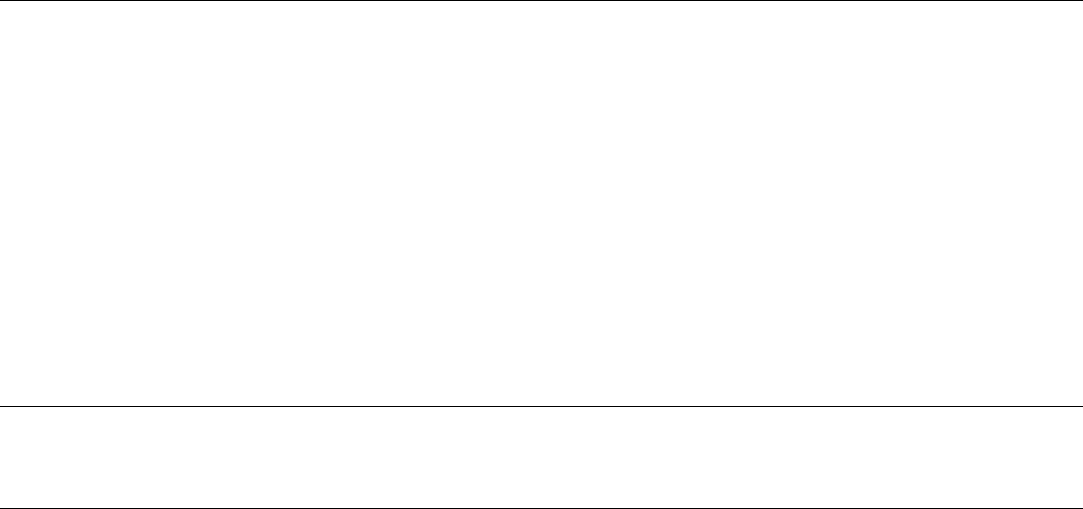
Inspection Without Standards. When standards are not available, a known undamaged area can be used as the
standard. Repaired areas are inspected by comparing them to an unrepaired area. The instrument reading may change
because of structural changes resulting from the repair. Repeated inspection scans must be conducted under various
instrument settings, and the inspection should be verified by other methods and/or instruments. A knowledge of the part
configuration (for example, number of bond lines, adhesive thickness, skin thickness, and so on) is essential for
interpreting the test results.
References cited in this section
1. M.T. Clark, "Definition and Non-Destructive Detection of Critical Adhesive Bond-Line Flaws," AFML-
TR-78-108, U.S. Air Force Materials Laboratory, 1978
4.
P. Bijlmer and R.J. Schliekelmann, The Relation of Surface Condition After Pretreatment to Bondability of
Aluminum Alloys, SAMPE Q., Oct 1973
10.
D. Hagemaier and R. Fassbender, Nondestructive Testing of Adhesive Bonded Structures, SAMPE Q.,
9 (No. 4), 1978
32.
"Adhesive Bonding (Structural) for Aerospace Systems, Requirements for," MIL-A-83377
33.
"Adhesive Bonded Aluminum Honeycomb Sandwich Structure, Acceptance Criteria," MIL-A-83376
34.
"Inspection Requirements, Nondestructive: For Aircraft Materials and Parts," MIL-I-6870 (ASG)
35.
"Nondestructive Testing Personnel Qualification and Certification," MIL-STD-410
Nondestructive Inspection of Adhesive-Bonded Joints
*
Donald J. Hagemaier, Douglas Aircraft Company, McDonnell Douglas Corporation
Evaluation and Correlation of Inspection Results
The experience, confidence, and effectiveness of NDI technicians and engineering personnel are gained by correlating
NDI results with destructive testing. Comparisons can be made between the NDI results and the actual size, shape,
location, and type of defect. Mistakes will occur in the early stages of the bonding program, but if accurate records,
photographs, and sketches are kept, they can serve as effective training devices. Sections of defective parts should be kept
for training purposes. All these items add to the confidence of the inspector in evaluating and accurately reporting defects.
They also add to the engineer's confidence in the inspector and in the data reported by the inspector.
Procedure
Before new adhesive-bonded assemblies are fabricated on a mass production basis, the first assembly is evaluated by
numerous methods. Inspections are performed and NDT results are evaluated to detect any variations in the part that are
indicative of discontinuities. The part is then cut up, and special precautions are taken to section through the
discontinuities or to separate the joint at the discontinuity to identify and verify the NDI results. To determine which NDT
method(s) detected the discontinuity, the NDI technicians use different color markings--for example, blue for x-ray, green
for ultrasonic, red for a bond tester, and so on. These markings can be affixed to the surface of the part or placed on a
transparent overlay of the part. When the part is sectioned, the results will identify which NDT method(s) correctly
identified the location, size, shape, and type of discontinuity. Although it is expensive, cutting the adhesive-bonded
assemblies is sometimes the only way to determine the nature of the discontinuity or to verify its existence. All inspection
results should be carefully documented for future reference.
Once a highly confident inspection technique is established, the remaining defective assemblies can be used for
developing repair procedures. The original NDI techniques can then be used for determining if the repairs are effective. In
some cases, defective parts are consistently produced, and the material, production process, or design must be changed to
correct the condition. This condition is usually evident when the same type of defect occurs in the same location in all
manufactured parts.