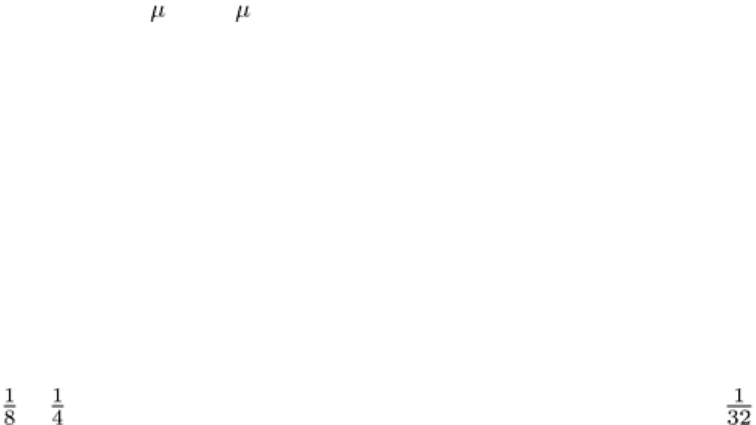
There are two basic methods of magnetic field application. For detecting longitudinal seams or cracks, the circular
magnetization method is used. For detecting transverse seams or cracks, longitudinal (or coil) magnetization is used. For
continuous-cast billets, circular and coil magnetization have been applied simultaneously. To detect multidirectional near-
surface flaws and surface flaws, it is convenient to use simultaneously a dc field for circular magnetization and an ac field
for longitudinal magnetization.
Generally, the billets are 3 to 14 m (10 to 45 ft) in length. The large billets are often referred to as blooms. To apply the
circular field, the current is passed directly through the billet longitudinally. To apply the longitudinal field, the billet is
placed along the axis of the coil, and either the billet or the coil is moved relative to the other.
In the wet magnetic particle method, for economy and handling convenience, a common carrier of the particles is water.
The particles are formulated so that they will not easily deteriorate in prolonged mixture with water. Other ingredients can
be added to facilitate the use of such a mixture, such as a wetting agent to disperse the particles and properly wet the part
surface, antifoaming chemicals to reduce the suds due to agitation, and antifreeze to keep the bath from freezing in winter.
If needed, fixer or binder can also be added to the bath to make the dried indications durable enough to withstand the
normal handling in the mill.
Inspection of Rolled Billets. Typically, particle types with sizes ranging from less than 10 to 70 μm (400 μin. to
0.003 in.) are often adequate to find the significant seams in rolled-billet inspection. The finest-size particle, 6 μm (240
μin.) or less, is good for finding extremely minute flaws--for example, inclusion flaws as small as 25 μm (0.001 in.) wide
in 0.25 mm (0.010 in.) thick steel sheets. For these flaws, larger-size particles may be ineffective; significant leakage
fields are confined to very small areas. The total forces exerted on the individual particles are usually weak a short
distance away, and the relatively bulky size and the momentum of large particles would prevent most of them from
getting close enough to the flaws to be strongly attracted and stay there. As a result, either too few magnetic particles are
retained at the flaw sites to contrast with the background, or the indications can be easily disturbed by their own weight
and by the bath flow.
However, very fine and shallow flaws are not important in practical billet inspection, in which flaw depths greater than
0.64 mm (0.025 in.) are often the only ones of interest. (When reheated, the outer skin of the billet with shallow flaws will
be oxidized to become scale and will fall off the part during further rolling operations.) Therefore, particles with nominal
diameters of 10 to 50 m (400 in. to 0.002 in.) are often used to give large indications for the significant seams and to
ignore very minor ones.
The ultimate choice of particle type is not determined by particle size alone. Other factors, such as the magnetic
properties, color, and brightness of the particles, must also be considered.
For the proper magnetization current level, a rule of thumb has been developed: Roughly 1000 Adc per 25 mm (1.0 in.) of
material diameter is satisfactory for most critical inspections. The equivalent surface field is about 1.2 × 10
4
A · m
-1
(157
Oe). For most practical large-billet inspections, less than half this value is used.
Inspection of Continuous-Cast Products. Slag pockets, transverse cracks, and longitudinal cracks are the typical
flaws found in continuous as-cast products (billets, blooms, and slabs). The slag pockets are near-surface inclusions. In a
few cases, they can be partially exposed to the surface. The inclusions are mainly slags. There may also be voids with
coats of oxidelike chemicals on the walls. They are often approximately round, but can be elongated in depth or
longitudinal direction. Depending on product type, the largest slag pockets uncovered in the laboratory can be 3.2 to 6.4
mm ( to in.) in diameter. The smallest ones may have diameters less than 0.8 mm ( in.). The pockets are generally
found within a 2.5 mm (0.1 in.) deep layer under the product surface. Small slag pockets are often found near the surface.
Cracks in the continuous-cast products have been observed to be deep and tight, with inclusions. The cracks can occur in
the direction of the oscillating mold marks (transverse corner cracks) or perpendicular to that direction. Depending on the
casting technique, they can occur in groups and branch out in all directions like a web, covering significant areas.
In general, the discussions about seam indication formation in rolled billets can be applied to crack indications in the
continuous-cast product. For example, in the case of slag-pocket indications, the parameter equivalent to the seam width
is the indication diameter. However, there are still a few differences between rolled-billet inspection and continuous-cast
bloom inspection.
Differences in Magnetization Levels. The magnetization level used in continuous-cast product inspection is usually
stronger than that required for rolled billets. Because of the subsurface nature of the flaws and the wider flaw dimensions,