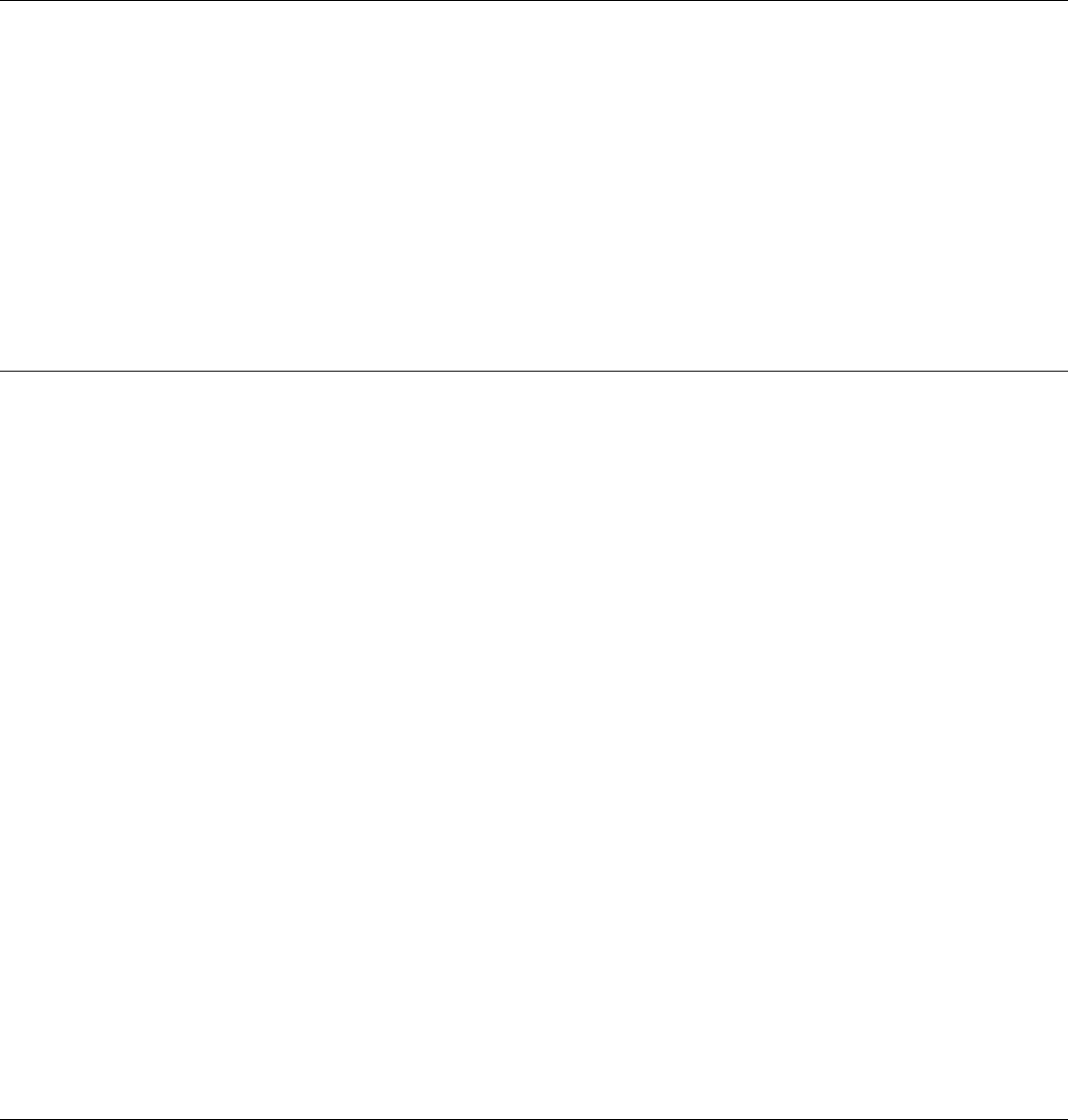
be monitored is provided by an electronic gate, adjustable through 180°. Only half of the full 360° wave is required, the
remainder being the negative duplicate of the positive and not shown on the oscilloscope. Both systems (standard coils,
Fig. 18) are fully independent and should be operated at different positions of the waveform to obtain as much
information as possible during the test. The standard system is used to monitor each bar in a lot for composition, hardness,
structure, and size and to indicate the presence of uniform-depth seams, cracks, and laps, which generally escape
detection by the null system.
Nondestructive Inspection of Steel Bar, Wire, and Billets
Equipment Requirements
In addition to coil arrangements such as those illustrated in Fig. 17 and 18, a fairly elaborate set of electronic gear is
required for inspecting steel bars. Some type of equipment for handling the bars and conveying them through the coils at
the desired rate is also required. The degree of sophistication designed into the equipment depends mainly on the number
of similar bars to be inspected.
Typical control units are adaptable to either the eddy current or the magnetic permeability systems of inspection. Many
variations are commercially available.
Nondestructive Inspection of Steel Bar, Wire, and Billets
Flaw Detection Procedure Using a Permeability System
The following description is presented purely as an example of setting up a procedure for detecting flaws by permeability
change using the null coils with one specific type of instrumentation. Procedures vary widely for various types of
equipment.
Select the proper size of secondary coil for the bars to be tested, and insert it into the primary-coil unit, making sure all
electrical connections are secure. Turn on the primary power, and adjust the coil current to about 8 A as shown on the
electrical meter on the power-supply panel. Adjust the combined coil unit so that the material will be concentric with the
inside diameter of the secondary coil. Select the appropriate feed-through speed of the conveyor system, and insert a bar
into the test coil. Turn the sensitivity on the null-equipment panel clockwise to about midposition, and while the bar is
moving in the forward direction, alternately adjust the balance x and y controls to bring the null waveshape, as seen on the
oscilloscope, to as near a straight line as possible. Do not stop the bar while making these adjustments, because it heats
rapidly and its permeability changes with increasing temperature, resulting in a flaw indication when passed through the
test coil on a repeat run. Furthermore, do not adjust the controls when the feed is reversed through the test coil, because
the magnetic field is dragged by the bar in the direction of travel and the balance obtained would not be correct for the
normal feed direction.
Assuming the oscilloscope controls are adjusted properly, the two stress peaks of the null waveshape will be located
equidistant from the edge of the tube face and 180° apart. Locate the index or gate about 10 to 15° to the right of the left
stress peak by use of its control knob, and adjust its height by the gain control so that it is easily recognizable. The choice
of using a 60-Hz filter, either in or out, is based on past experience when testing the same type of material with a similar
setup. Finally, readjust the sensitivity control so that the small fluctuations within the gate do not reach the preset trip
level for the various signaling devices.
Nondestructive Inspection of Steel Bar, Wire, and Billets
Sorting Procedure Using a Permeability System