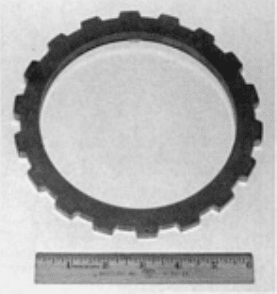
Fig. 27 Automatic transmission clutch plate examined by resistivity measurement. Courtesy of
and N.F. McQuiddy, Ferraloy
Eddy Current Testing. Another form of resistivity testing is the eddy current test. In this test, instead of producing
currents in the part by direct contact with electrodes, eddy currents are induced in the part by an alternating
electromagnetic field from an induction coil, as described in the article "Eddy Current Inspection" in this Volume.
Single-Coil Tests. Disruptions in the eddy current path due to any defect that changes the resistivity of the material are
detected as extraneous induced voltages in the induction coil. Alternatively, a separate detector coil can be placed in the
magnetic field around the testpiece.
The alternating current in the induction coil can vary from 1 to 1000 kHz. The depth of penetration varies with frequency,
with the highest frequencies yielding the smallest depths (skin effect). The way in which the eddy current varies as a
function of depth is also described in the article "Eddy Current Inspection" in this Volume.
The output of eddy current testing is in the form of an oscilloscope display. An eddy current inspection system can detect
changes from point to point in single testpieces (for example, welded tubes) as they move through the coil. For cases
where the testpieces consist of a series of discrete parts, a second coil containing a reference can be added to the system;
this configuration is called a magnetic bridge comparator.
Magnetic Bridge Comparator Testing. When a ferromagnetic part is placed in the core of a coil with an alternating
current, a unique set of harmonics characteristic to the part can be detected in the coil. Some of the variables influencing
the harmonics are alloy type, core or surface hardness, case depth, and porosity (Ref 35).
In the magnetic bridge comparator arrangement, the harmonic signals from two like coils are compared. The coils are
similar and carry the same excitation waveform. One coil contains the part to be inspected and the other a reference part
chosen at random from the group to be tested. Differences between the harmonic characteristics of the two parts are
displayed as the displacement of a dot from the center of an oscilloscope screen; no displacement means the two parts are
alike.
Although the magnetic susceptibility of porous sintered steels is reduced by the pinning of domain-boundary walls by
pores, P/M parts are also capable of being analyzed by the magnetic bridge comparator. In one study, 120 P/M production
parts were tested in a magnetic bridge comparator. Seventeen of the parts were singled out on the basis of a displacement
of the oscilloscope indication, as shown in Fig. 28. These parts were tested for chemistry, hardness, crush strength, and
pressed height. For comparison, 25 parts selected at random from the remaining specimens were also tested. Statistically
significant differences were found between the groups with regard to carbon content and hardness (Ref 36). The
technique has also been successfully applied to powder-forged parts (Ref 37). Although there are no published trials, there
is a possibility that the comparator could also be used for testing green compacts.