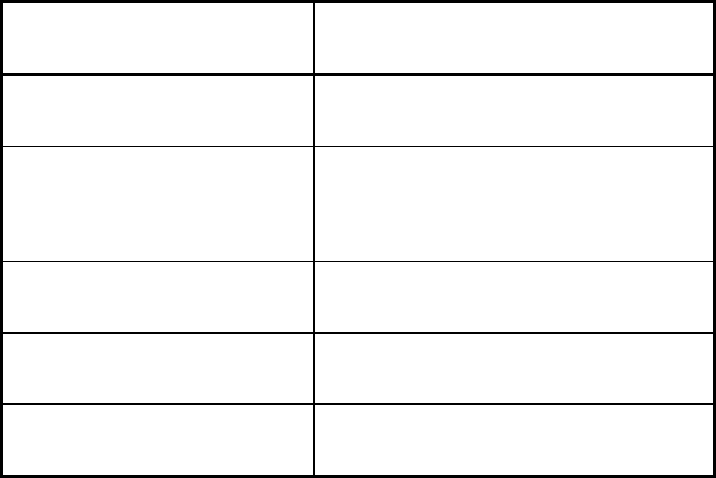
Table 3 Specifications of an ultrasonic flaw detection system for cold-drawn wires
Parameter
Specifications
Dimension of material, mm (in.)
15-30 (0.590-1.181)
Testing frequency
Normal beam: 10 MHz, 1 channel
Angle beam: 5 MHz, 2 channels
Surface wave: 5 MHz, 2 channels
Number of rotations of probe, rev/min
1000
Signal transmit
Noncontact rotation transmit
Marker One each for near-surface flaw and inside flaw
Source: Ref 1
Results of experiments with this system showed detectability of 0.1 mm (0.004 in.) minimum flaw depth on surface
defects and 0.2 mm (0.008 in.) minimum inside defect size. This system enables the user to inspect the entire cross
section of cold-drawn wires to a high degree of accuracy. Detailed information on the fundamentals, equipment, and
techniques for ultrasonic inspection is available in the article "Ultrasonic Inspection" in this Volume.
Electromagnetic Inspection Methods
Electromagnetic methods of inspection are used far more extensively for nondestructive inspection of steel bars than any
of the methods discussed above. Electromagnetic methods are readily adaptable to automation and can be set up to detect
flaws, as well as a number of different compositional and structural variations, in bars on a mass-production basis.
Equipment can be relatively simple, but for mass-production inspection the equipment may be highly sophisticated and
costly. Such equipment can not only detect flaws and indicate them on an oscilloscope or other form of readout but can
also mark the location of the flaw on the bar before it emerges from the inspection equipment and can automatically sort
the bars on the basis of seam depth.
Eddy Current Testing of Cold-Drawn Bars (Ref 1). Surface defects on cold-drawn bars can be inspected by eddy
current detection methods using an encircling coil. This method utilizes a rotating probe that detects surface defects with
the probe coil rotating at high speed around the circumference of the cold-drawn bars.
The encircling coil method exhibits lower detectability on linear flaws because flaw detection depends on the difference
between two test coils in which the material to be tested is encircled. On the other hand, the method of rotating the probe
coil at high speed along the circumference of the material to be tested can detect linear defects because it detects bars in
spiral scanning.
Table 4 lists the specifications of the detection system. One of the main features is signal transmission in the probe
rotation unit by the noncontact rotating transmit method, which requires no maintenance work. Guide sleeves are placed
in front of and behind the probe to maintain a constant distance between the probe and the material to be tested, which is
important for acceptable performance of the system (Fig. 8). Furthermore, the rotation axis of the probe and the axis of
the material to be tested are kept in a line by pinch rollers placed in front of and behind the detector. On the probe, a
distance sensor is used for the automatic gain control function to provide electric compensation against distance variation.