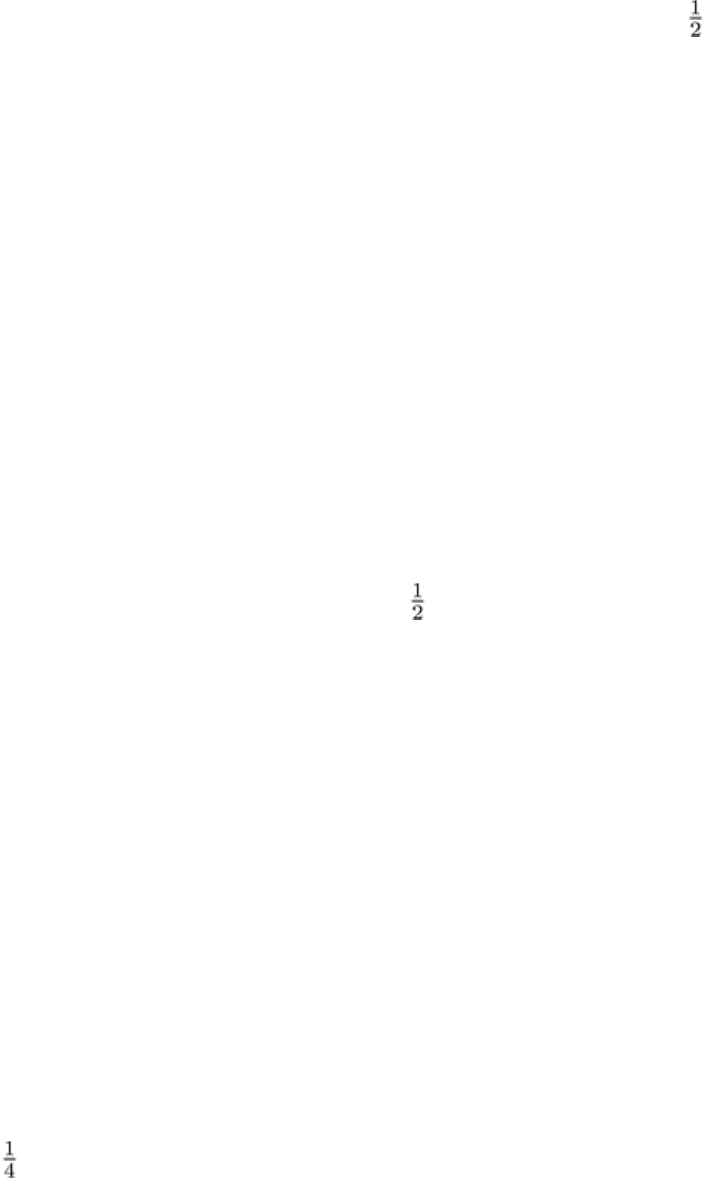
The amplitude of the reflection from the flat-bottom hole in the longest calibration block is set at 13 mm (0.5 in.) sweep
to peak, and the other points of the DAC curve are obtained at this gain setting. This curve can be marked on the face of
the screen or plotted on graph paper. This is the fixed DAC curve that will be used to evaluate the indications. Any
portion of the DAC curve above the vertical linearity limits of the instrument is brought on screen with the attenuator for
evaluation of the indications in this area.
After establishing the fixed DAC curve, the amplitude of the back reflection over the area of greatest acoustical
penetrability is determined at this instrument gain level. The transducer is then coupled to the forging over the area of
least penetrability, and the gain setting of the instrument is increased to bring the back reflection to the same amplitude as
the amplitude obtained over the area of greatest acoustical penetrability (a minimum of 40 mm, or 1 in., sweep to peak).
For scanning, the instrument gain level is increased a minimum of twice the final gain setting.
Any indication, detected while scanning, whose amplitude equals or exceeds the reporting level is evaluated. This
evaluation is conducted by readjusting the back reflection in a discontinuity-free area of the forging as close as practical
to the area of indication to equal the same height of back reflection obtained in the area of greatest acoustic penetrability
when the DAC curve was established. The search unit is repositioned over the area of the indication, and the evaluation to
the DAC curve is made.
Back-reflection reduction is evaluated by adjusting the first back reflection to the maximum back reflection within the
vertical linearity limits of the instrument in a discontinuity-free area of the forging as close as practical to the area of the
indication to be evaluated. The search unit is repositioned over the area containing the indication, and the amplitude is
recorded.
For contoured forgings at final inspection, ultrasonic inspection in the primary test direction is performed using a DAC
curve established from the same reference blocks used for preliminary inspection. The last point of the curve is 13 mm
(0.5 in.) sweep to peak, and the other points of the DAC curve are obtained at that gain setting. This is the fixed DAC
curve that will be used to evaluate any indications. Compensation for the areas of greatest and least penetrability does not
apply at final inspection with a contoured forging.
Calibration: Secondary Test Direction. The secondary test direction is approximately at 90° to the primary
direction. The transducer is coupled to the face of the forging, and the amplitude of the first back reflection is set within
the vertical linearity limit of the instrument (minimum 40 mm, or 1 in., sweep to peak). The DAC curve is established
at this gain setting, using the same blocks that were used for the longitudinal wave inspection in the primary test direction.
The last point of the DAC curve is extended parallel to the sweep line to midlength plus 25 mm (1 in.). Any indications
will be evaluated against this DAC curve. When the configuration of the forging at final inspection due to contour
machining prevents ultrasonic examination in the axial direction to midlength plus 25 mm (1 in.), the DAC curve will be
extended parallel to the sweep line to the deepest location, wherever possible, for evaluation of the indications.
Shear Wave Ultrasonic Inspection
Shear wave inspection is performed from the circumference of rings and hollow forgings that have axial length greater
than 50 mm (2 in.) and a ratio of outside to inside diameters of less than 2:1. A 1.0-MHz, 45° angle-beam search unit is
used when shear wave inspecting forgings having a ratio of outside to inside diameters of less than 1.4:1. Forgings with a
ratio of outside to inside diameters of 1.4:1 or greater, but less than 2:1, will be shear wave tested at a beam angle of less
than 45°. Shear wave inspection is performed by scanning in both circumferential directions (clockwise and
counterclockwise) along the periphery of the forging.
Inside diameter and outside diameter calibration notches are cut axially in the surface of the forging or a similar testpiece
(preferably, excess metal or test metal). The sides of the notches should be smooth and parallel to the axis of the forging.
The calibration notches are 25 mm (1 in.) long, V-shaped or rectangular, with a width not exceeding twice the depth.
These notches should have a depth of 3% of the maximum section thickness (based on thickness at initial ultrasonic
inspection) or 6 mm ( in.), whichever is smaller. If at final inspection it is necessary to place the calibration notches in
the forging, these will have to be weld repaired.