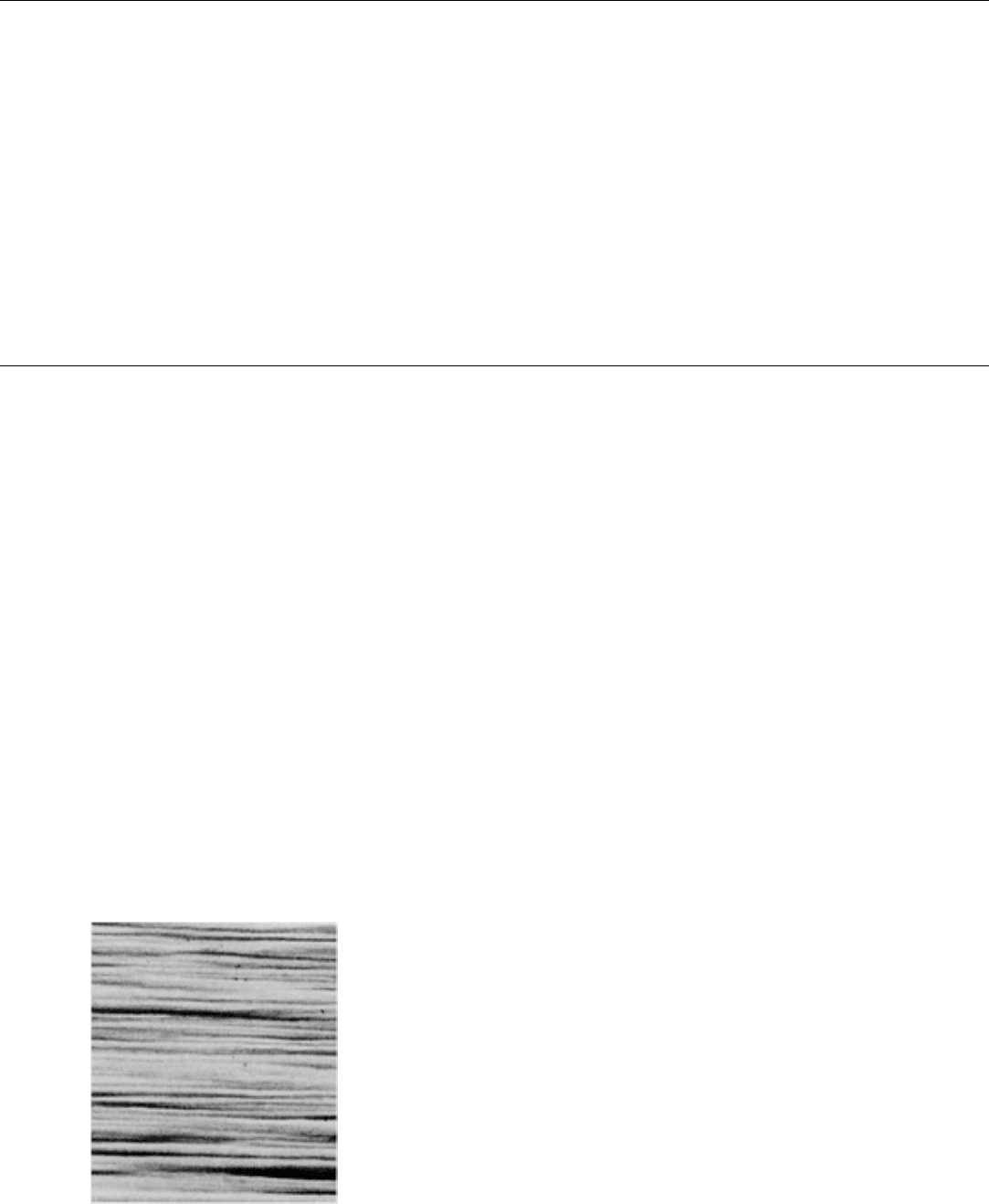
Nondestructive Inspection of Forgings
Introduction
IN FORGINGS of both ferrous and nonferrous metals, the flaws that occur most often are caused by conditions that exist
in the ingot, by subsequent hot working of the ingot or the billet, and by hot or cold working during forging. The
nondestructive inspection (NDI) methods most commonly used to detect these flaws include visual, magnetic particle,
liquid penetrant, ultrasonic, eddy current, and radiographic inspection. This article discusses the applications of these
methods to forgings. Information on the equipment and techniques used in these inspection methods is available in the
articles so titled in this Volume.
Nondestructive Inspection of Forgings
Flaws Originating in the Ingot
Many large open-die forgings are forged directly from ingots. Most closed-die forgings and upset forgings are produced
from billets, rolled bar stock, or preforms. Many, though by no means all, of the imperfections found in forgings can be
attributed to conditions that existed in the ingot, sometimes even when the ingot has undergone primary reduction prior to
the forging operation. Some, but again by no means all, of the service problems that occur with forgings can be traced to
imperfections originating in the ingot.
Chemical Segregation. The elements in a cast alloy are seldom distributed uniformly. Even unalloyed metals contain
random amounts of various types of impurities in the form of tramp elements or dissolved gases; these impurities are also
seldom distributed uniformly. Therefore, the composition of the metal or alloy will vary from location to location.
Deviation from the mean composition at a particular location in a forging is termed segregation. In general, segregation is
the result of solute rejection at the solidification interface during casting. For example, the gradation of composition with
respect to the individual alloying elements exists from cores of dendrites to interdendritic regions. Segregation therefore
produces a material having a range of compositions that do not have identical properties.
Forging can partially correct the results of segregation by recrystallizing or breaking up the grain structure to promote a
more homogeneous substructure. However, the effects of a badly segregated ingot cannot be totally eliminated by
forging; rather, the segregated regions tend to be altered by the working operation, as shown in Fig. 1.
In metals, the presence of localized regions that deviate from the
nominal composition can affect corrosion resistance, forging and
joining (welding) characteristics, mechanical properties, fracture
toughness, and fatigue resistance. In heat-treatable alloys,
variations in composition can produce unexpected responses to
heat treatments, which result in hard or soft spots, quench cracks,
or other flaws. The degree of degradation depends on the alloy and
on process variables. Most metallurgical processes are based on an
assumption that the metal being processed is of a nominal and
reasonably uniform composition.
Ingot Pipe and Centerline Shrinkage. A common
imperfection in ingots is the shrinkage cavity, commonly known as
pipe, often found in the upper portion of the ingot. Shrinkage
occurs during freezing of the metal, and eventually there is
insufficient liquid metal near the top end to feed the ingot. As a
result, a cavity forms, usually approximating the shape of a
cylinder or cone--hence the term pipe. Piping is illustrated in Fig.
Fig. 1
Microstructural bonding due to chemical
segregation and mechanical working