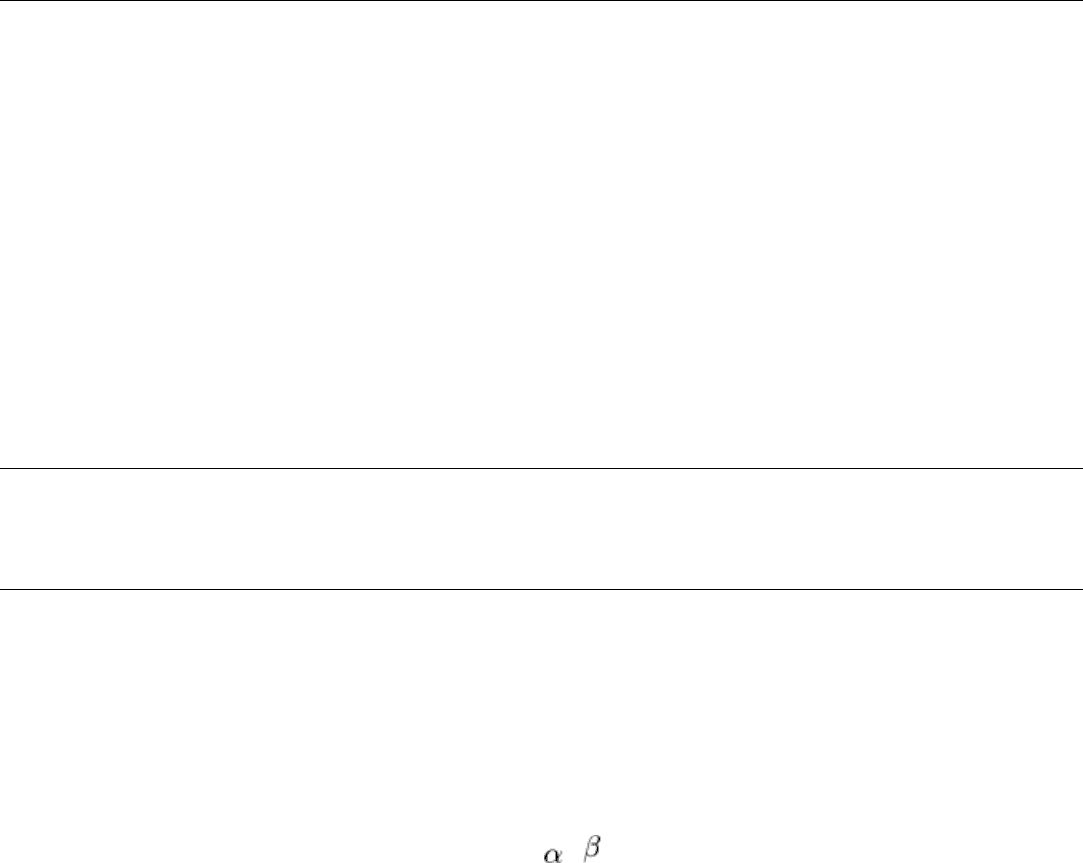
Preexisting Flow Lines in Billet. When the ALPID simulation is for an operation using an already worked billet or a
forged preform, prior flow lines exist. In this case, the technique offered is to provide flow lines as input to the simulation
and then to follow these flow lines through the course of the simulation. An example of this technique is given in Fig.
12(b).
References cited in this section
6. S.M. Doraivelu et al., Int. J. Mech. Sci., Vol 26, 1984, p 527
53.
S.I. Oh, Finite Element Analysis of Metal Forming Problems With Arbitrarily Shaped Dies,
Sci., Vol 17, 1982, p 293
54.
O.C. Zienkiewicz, The Finite Element Method, 3rd ed., McGraw-Hill, 1977
55.
W.T. Wu and S.I. Oh, ALPIDT: A General Purpose FEM Code for Simulation of Non-
Processes, NAMRC-XIII, University of California, Berkeley, 1985
56.
Y.T. Im, Ph.D. dissertation, University of California, Berkeley, 1985
57.
J.J. Park and S. Kobayashi, Three-Dimensional Finite Element Analysis of Block Compression,
Mech. Sci., Vol 26, 1984, p 165-176
58.
J.C. Malas, "A Thermodynamic and Continuum Approach to the Design and Control of Precision Forging
Processes," Wright State University, 1985
59.
H. Nitin, M.S. thesis, Ohio University, 1987
Modeling Techniques Used in Forging Process Design
H. L. Gegel and J.C. Malas, Air Force Wright Aeronautical Laboratories/Materials Laboratory; S.M. Doraivelu and V.A. Shende,
Universal Energy Systems, Knowledge Integration Center
Example Applications of ALPID
Spike Forging. In spike forging, a cylindrical billet is forged in an impression die containing a central cavity (Ref 60).
The deformation characteristics of spike forging are such that the portion of the material near the outside diameter flows
radially, while the portion near the center of the top of the surface is extruded, forming a spike.
In this application, the primary objective was to determine the conditions that would allow complete die filling in spike
forging. For this purpose, the constitutive equations for the + Ti-6Al-2Sn-4Zr-2Mo microstructure at 954 °C (1750
°F), which exhibits strain rate hardening, were selected for the analysis. The die shape and the specimen with the selected
mesh pattern are illustrated in Fig. 13.