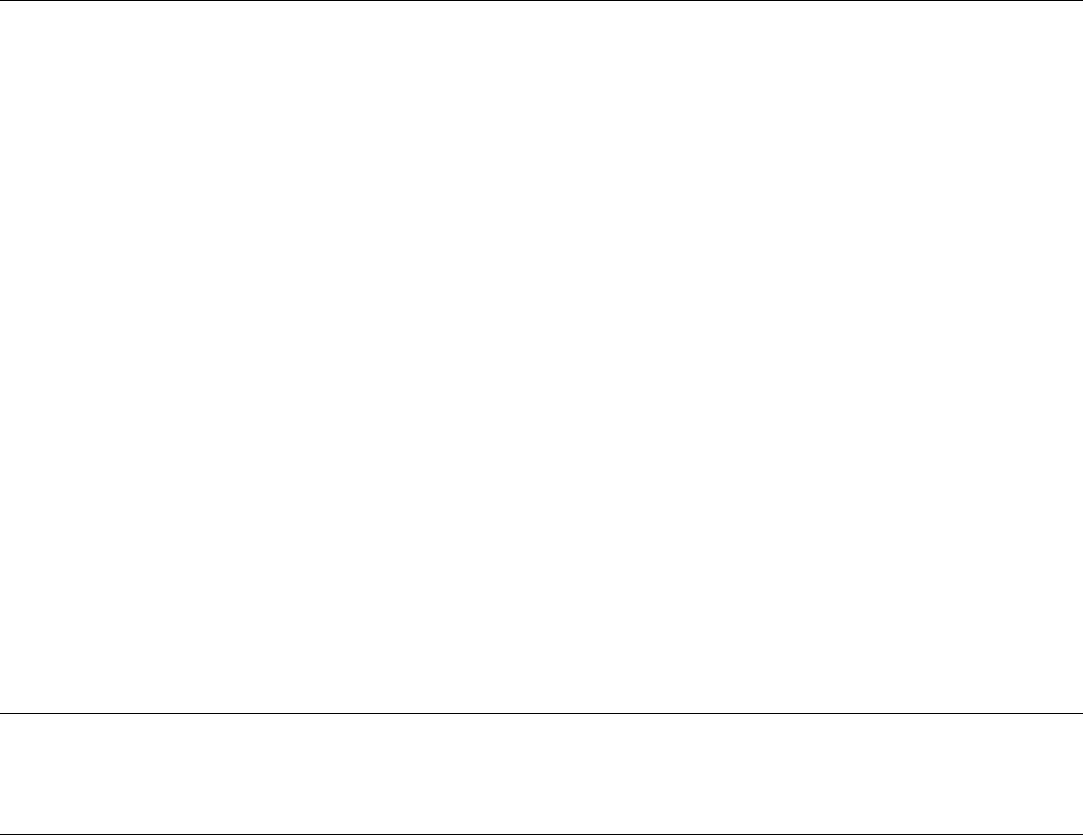
The elastic-plastic method assumes that the material deformation includes a small, recoverable elastic part and a
much larger, nonrecoverable plastic part. It can give details regarding deformation loads, stresses and strains, and residual
stresses. This method has been applied to a large variety of problems, including upsetting (Ref 48), indentation (Ref 49),
extrusion (Ref 50), and expansion of a hole in a plate (Ref 51). However, because of the large change in the material flow
behavior between elastic and plastic deformation and the need to check the status of each element, the deformation steps
must be small, and this makes the method uneconomical.
The rigid-viscoplastic method assumes that the deformation stresses are primarily dependent on deformation (strain)
rates. Several programs based on the variational approach have been written by various researchers and have been applied
to the same range of problems as the elastic-plastic finite-element method (Ref 52). Although predictions regarding
residual stresses cannot be made with the rigid-viscoplastic finite-element method, the larger steps that can be used in
modeling metal-forming procedures make the method very economical, especially for modeling hot deformation.
References cited in this section
41.
T. Altan, S. Oh, and H. Gegel, Metal Forming: Fundamentals and Applications,
Metals, 1983
42.
O. Hoffman and G. Sachs, Introduction to the Theory of Plasticity for Engineers, McGraw-Hill, 1953
43.
S. Kobayashi and E.G. Thomson, Approximate Solutions to a Problem of Press Forging, Trans. ASME,
B, Vol 81, 1959, p 217-227
44.
B. Avitzur, Metal Forming: Processes and Analysis, McGraw-Hill, 1968
45.
W. Johnson and H. Kudo, The Mechanics of the Metal Extrusion, Manchester University Press, 1962
46.
K. Lange, Handbook of Metal Forming, McGraw-Hill, 1985
47.
R. Hill and S.J. Tupper, A New Theory of the Plastic Deformation in Wire Drawing, J. Iron Steel Inst.,
159, 1948, p 353-359
48.
C.H. Lee and S. Kobayashi, Analysis of Axisymmetrical Upsetting and Plane-Strain Side-
Cylinders by Finite Element Method, J. Eng. Ind. (Trans. ASME), Vol 93, 1971, p 445
49.
C.H. Lee and S. Kobayashi, Elastoplastic Analysis of Plane-
Strain and Axisymmetric Flat Punch
Indentation by the Finite Element Method, Int. J. Mech. Sci., Vol 12, 1970, p 349
50.
A. Kumar, Ph.D. thesis, University of Roorkee, 1987
51.
J.S. Gunasekera and J.M. Alexander, Analysis of the Large Deformation of an Elastic-Plastic Axially-
Symmetric Continuum, in International Symposium on Foundations of Plasticity,
1972, p 25-146
52.
S. Kobayashi, Rigid Plastic Finite-
Element Analysis of Axisymmetrical Metal Forming Processes, in
Numerical Modeling of Manufacturing Processes ASME, PVP-PB-025, 1977, p 49-68
Modeling Techniques Used in Forging Process Design
H. L. Gegel and J.C. Malas, Air Force Wright Aeronautical Laboratories/Materials Laboratory; S.M. Doraivelu and V.A. Shende,
Universal Energy Systems, Knowledge Integration Center
Analysis of Large Plastic Incremental Deformation (ALPID)
The computer program ALPID, a rigid-viscoplastic FEM program that uses the approach of Kobayashi et al., was
developed at Battelle Columbus Laboratories under the Air Force Processing Science Program (Ref 53). Important
contributions (Ref 53) to the FEM formulation included the incorporation of convenient features, such as capabilities for
handling arbitrary die geometries and remeshing. Details of this FEM formulation and some of its applications to practical
problems can be found in Ref 53. The features of ALPID are discussed below.