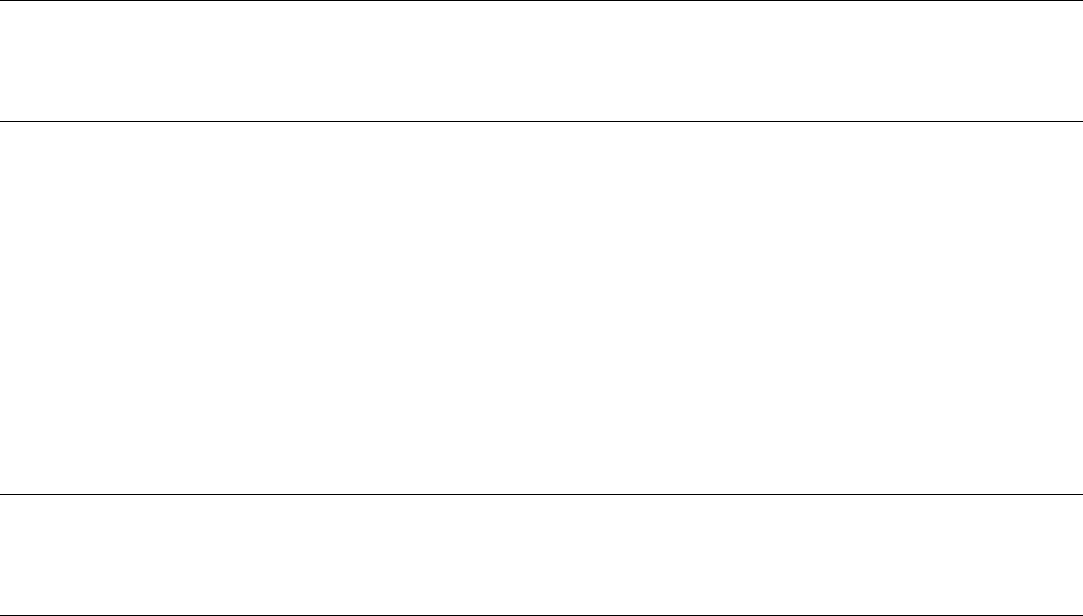
References
1. S. Kobayashi, "Thermovisioplastic Analysis of Titanium Alloy Forging," AFWAL-TR-81-
Wright Aeronautical Laboratories, 1981
2. S.-I. Oh, "Finite Element Analysis of Metal Forming Processes with Arbitrarily-Shaped Dies,"
Sci., Vol 24, 1982, p 479
3. J.S. Gunasekera, H.L. Gegel, J.C. Malas, S.M. Doraivelu, and G. Griffin, Computer-
Approach to Metal Forming, American Society of Mechanical Engineering, 1982, p 1-6
4. R.J. Mayer, IGES: One Answer to the Problems of CAD Database Exchange, BYTE, 1987, p 209-214
5. J.P. Tang, S.-I. Oh, D.W. Birch, and K. Hoang-
Vu, "Manufacturing Science Program to Develop a
Computer-Aided Engineering (CAE) System for Die (Mold) Design and Manufacturing," AFWAL-TR-86-
405, Air Force Wright Aeronautical Laboratories, 1986
6.
K.R. Venuri, P.S. Ragupathi, and T. Altan, "Automatic Design of Blocker Forging Dies," Paper presented
at the 14th NAMRC Conference, Minneapolis, 1986
7.
H.L. Gegel, J.C. Malas, S.M. Doraivelu, J.M. Alexander, and J.S. Gunasekera, "Materials Modeling and
Intrinsic Workability for Simulation of Bulk Deformation," Advanced Technology of Plasticity,
Springer-
Verlag, 1987, p 1243; and product publication of Universal Energy Systems Knowledge
Integration Center, 1987
8. A.B. Shapiro, "TOPAZ 2D--A Two-
Dimensional Finite Element Code of Heat Transfer Analysis,
Electrostatic and Magnetostatic Problems," Report UCID 20824, July 1986
9. J.O. Hallquist, "NIKE-
2D, a Vectorized Implicit Finite Deformation, Finite Element Code for Analyzing
the Static and Dynamic Response of 2-D Solids," Lawrence Livermore National Laboratory, 1983
10.
V. Ashok and J. Ramanathan, A Knowledge-Based Software Development Assistant, in
Spring DECUS, U.S. Symposium, Digital Equipment Computer Users Society, May 1987, p 35
Modeling Techniques Used in Forging Process Design
H. L. Gegel and J.C. Malas, Air Force Wright Aeronautical Laboratories/Materials Laboratory; S.M. Doraivelu and V.A. Shende,
Universal Energy Systems, Knowledge Integration Center
Introduction
AN UNDERSTANDING of the flow behavior of the workpiece material under processing conditions is necessary in
order to exploit the full potential of process modeling techniques. Mechanistic and dynamic material modeling
approaches are being used to understand the fundamentals of flow, fracture, and workability. The former approach is
based on activation energy analysis and is limited to processes that can be described by steady-state equations applied to
pure, crystalline, and simple alloys. The latter approach is based on continuum and thermodynamic fundamentals and is
used to understand the intrinsic workability of simple as well as complex alloys. Dynamic material modeling is required
for obtaining realistic predictions of the total performance of any nonlinear deformation process and for reducing the cost
of the design process. The basic concepts and procedures involved in each of these approaches will be discussed in this
article.
Modeling Techniques Used in Forging Process Design
H. L. Gegel and J.C. Malas, Air Force Wright Aeronautical Laboratories/Materials Laboratory; S.M. Doraivelu and V.A. Shende,
Universal Energy Systems, Knowledge Integration Center
Constitutive Equations for Material Modeling