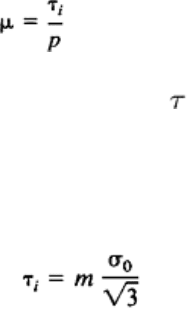
faster the deformation process, the greater the percentage of heat energy that goes to increase the temperature of the
workpiece.
Friction. An important concern in all practical metalworking processes is the friction between the deforming workpiece
and the tools and/or dies that apply the force and constrain the shape change. Friction occurs because metal surfaces, at
least on a microscale, are never perfectly smooth and flat. Relative motion between such surfaces is impeded by contact
under pressure.
The existence of friction increases the value of the deformation force and makes deformation more inhomogenous (Fig.
7c), which in turn increases the propensity for fracture. If friction is high, seizing and galling of the workpiece surfaces
occur, and surface damage results.
The mechanics of friction at the tool/workpiece interface are very complex; therefore, simplifying assumptions are
usually used. One such assumption is that friction can be described by Coulomb's law of friction:
(Eq 9)
where μ is the Coulomb coefficient of friction,
i
is the shear stress at the interface, and p is the stress (pressure) normal
to the interface.
Another simplification of friction is to assume that the shear stress at the interface is directly proportional to the flow
stress σ
0
of the material:
(Eq 10)
where m, the constant of proportionality, is the interface friction factor. For given conditions of lubrication and
temperature and for given die and workpiece materials, m is usually considered to have a constant value independent of
the pressure at the interface. Values of m vary from 0 (perfect sliding) to 1 (no sliding). In the Coulomb model of friction,
τ
i
increases with p up to a limit at which interface shear stress equals the yield stress of the workpiece material.
Control of friction through lubrication is an important aspect of metalworking. High friction leads to various defects that
limit workability. However, for most workability tests, conditions are selected under which friction is either absent or
easily controlled. Most workability tests make no provision for reproducing the frictional conditions that exist in the
production process; consequently, serious problems can result in the correlation of test results with actual production
conditions.
Stress State. Because of the different geometries of the tools and workpiece and the different manners in which the
forces of deformation are applied, different metalworking processes produce different stress states. A common system of
classifying the stress state found in metalworking processes is:
Tensile-compressive systems
• Biaxial tension-uniaxial compression, such as under the roll of a two-roll rotary piercer
• Uniaxial tension-uniaxial compression, such as in the flange of a cup in deep drawing
• Uniaxial tension-biaxial compression, such as in the deformation zone in wire and rod drawing
Compressive stress systems
• Uniaxial stress, such as in forging and upsetting in closed dies
• Biaxial stress, such as between the rolls of a rolling mill when operating without front or back tension
• Triaxial stress, such as in extrusion and in certain parts of a forging deformed in a die