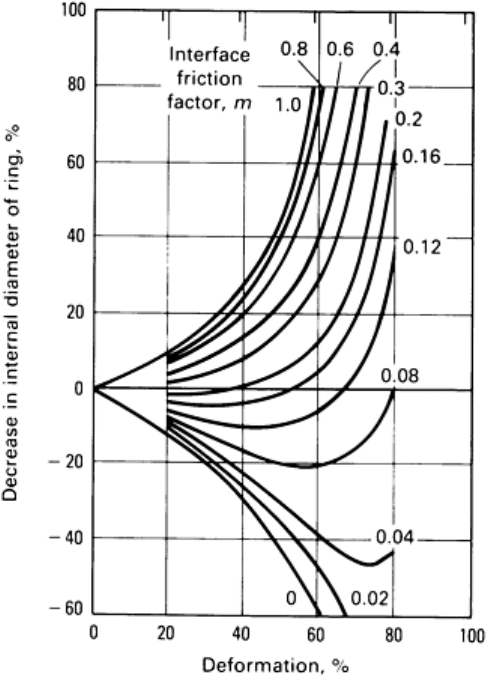
The ring thickness is usually expressed in relation to
the inside and outside diameters. The maximum
thickness that can be used while still satisfying the
mathematical assumption of thin-specimen
conditions varies, depending on the actual friction
conditions. Under conditions of maximum friction,
the largest usable specimen height is obtained with
rings of dimensions in the OD:ID:thickness ratio of
6:3:1. Under conditions of low friction, thicker
specimens can be used while still satisfying the
above assumption. For normal lubricated conditions,
a geometry of 6:3:2 can be used to obtain results of
sufficient accuracy for most applications.
For experimental conditions in which specimen
thicknesses are greater than those permitted by a
geometry of 6:3:1 and/or the interface friction is
relatively high, the resulting side barreling or
bulging must be considered. Analytical treatment of
this more complex situation is available in Ref 24.
The ring compression test can be used to measure
the flow stress under high-strain practical forming
conditions. The only instrumentation required is that
for measuring the force needed to produce the
reduction in height. The change in diameter of the
6:3:1 ring is measured to obtain a value of the ratio
p/σ
0
by solving the analytical expression for the
deformation of the ring or by using computer
solutions for the ring (Ref 25). Measurement of the
area of the ring surface formerly in contact with the
die and knowledge of the deformation load facilitate
calculation of p and therefore the value of the
material flow stress, σ
o
, for a given amount of deformation. Repetition of this process with other ring specimens over a
range of deformation allows the generation of a complete flow stress-strain curve for a given material under particular
temperature and strain rate deformation conditions.
Hot Tension Testing. Although necking is a fundamental limitation in tension testing, the tension test is nevertheless
useful for establishing the temperature limits for hot working. The principal advantage of this test for industrial
applications is that it clearly establishes maximum and minimum hot-working temperatures (Ref 26).
Most commercial hot tensile testing is done with a Gleeble unit, which is a high strain rate, high-temperature testing
machine (Ref 27). A solid buttonhead specimen that has a reduced diameter of 6.4 mm (0.250 in.) and an overall length of
89 mm (3.5 in.) is held horizontally by water-cooled copper jaws (grips), through which electric power is introduced to
resistance heat the test specimen (Fig. 16). Specimen temperature is monitored by a thermocouple welded to the specimen
surface at its midlength. The thermocouple, with a function generator, controls the heat fed into the specimen according to
a programmed cycle. Therefore, a specimen can be tested under time-temperature conditions that simulate hot-working
sequences.
Fig. 15 Th
eoretical calibration curve for standard ring with
an OD:ID:thickness ratio of 6:3:2.