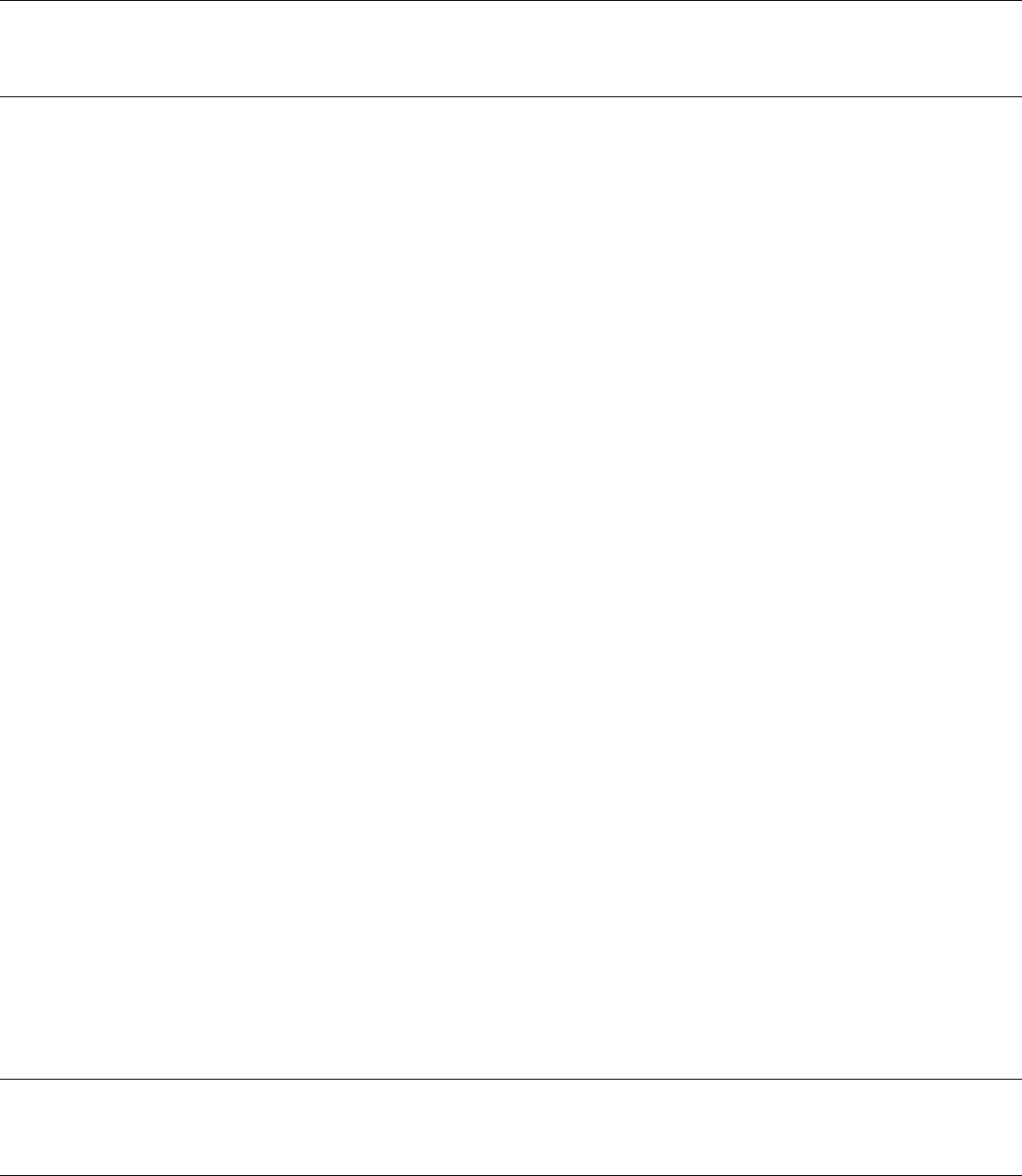
Introduction to Workability
George E. Dieter, University of Maryland
Introduction
WORKABILITY refers to the relative ease with which a metal can be shaped through plastic deformation. The term
workability is often used interchangeably with the term formability, which is preferred when referring to the shaping of
sheet metal parts (see the Section "Evaluation of Formability for Secondary (Sheet) Forming" in this Volume). However,
workability is usually used to refer to the shaping of materials by such bulk deformation processes as forging, extrusion,
and rolling.
The characterization of the mechanical behavior of a material by tension testing measures two different types of
mechanical properties: strength properties (such as yield strength and ultimate strength) and ductility properties (such as
percentage of elongation and reduction in area). Similarly, the evaluation of workability involves both measurement of
the resistance to deformation (strength) and determination of the extent of possible plastic deformation before fracture
(ductility). Therefore, a complete description of the workability of a material is specified by its flow stress dependence on
processing variables (for example, strain, strain rate, preheat temperature, and die temperature), its failure behavior, and
the metallurgical transformations that characterize the alloy system to which it belongs.
However, the major emphasis in workability is on measurement and prediction of the limits of deformation before
fracture.Therefore, the emphasis in this article is on methods for determining the extent of deformation a metal can
withstand before cracking or fracture occurs. It is important, however, to allow for a more general definition in which
workability is defined as the degree of deformation that can be achieved in a particular metalworking process without
creating an undesirable condition. Generally, the undesirable condition is cracking or fracture, but it may be another
condition, such as poor surface finish, buckling, or the formation of laps, which are defects created when metal folds over
itself during forging.In addition, in the most general definition of workability, the creation by deformation of a
metallurgical structure that results in unsatisfactory mechanical properties, such as poor fracture toughness or fatigue
resistance, can be considered to be a limit on workability.
In the restricted context of the forging process, the relative ability of a material to deform without fracture is termed
forgeability.Because the ability of the material to flow readily and to fill the die recesses completely is important, this is
another aspect of forgeability. This aspect of forgeability is measured by the flow stress of the material. Methods of
measuring flow stress are briefly discussed in this article and are treated in more detail in the Section "Computer-Aided
Process Design for Bulk Forming".
Generally, workability depends on the local conditions of stress, strain, strain rate, and temperature in combination with
material factors, such as the resistance of a metal to ductile fracture. In addition to a review of the many process variables
that influence the degree of workability, the mathematical relationships that describe the occurrence of room-temperature
ductile fracture under workability conditions are summarized in this article. The most common testing techniques for
workability prediction are discussed in the article "Workability Tests" in this Section.
Introduction to Workability
George E. Dieter, University of Maryland
Material Factors Affecting Workability
Fracture Mechanisms. Fracture in bulk deformation processing usually occurs as ductile fracture, rarely as brittle
fracture.However, depending on temperature and strain rate, the details of the ductile fracture mechanism will vary.
Figure 1 illustrates the different modes of ductile fracture obtained in a tension test over a wide range of strain rates and
temperatures. At temperatures below about one-half the melting point of a given material (below the hot-working region),
a typical dimpled rupture type of ductile fracture usually occurs. A more commonly found representation of possible