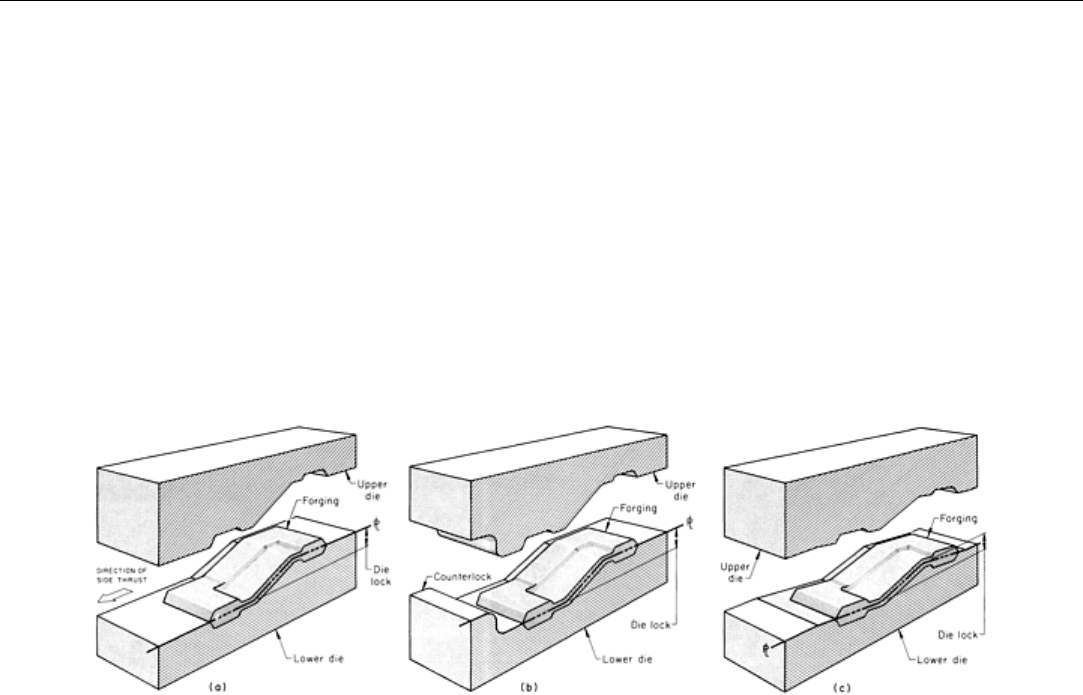
Dies and Die Materials for Hot Forging
Locks and Counterlocks
Many forgings require a parting line that is not flat and, correspondingly, die parting surfaces that are neither planar nor
perpendicular to the direction in which the forging force is applied. Dies that have a change in the plane of their mating
surfaces, and that therefore mesh ("lock") in a vertical direction when closed, are called locked dies.
In forging with locked dies, side or end thrust is frequently a problem. A strong lateral thrust during forging may cause
mismatch of the dies or breakage of the forging equipment. There are several ways to eliminate or control side thrust.
Individual forgings can be inclined, rotated, or otherwise placed in the dies so that the lateral forces are balanced (see Fig.
13c). Flash can be used to cushion the shock and help absorb the lateral forces. When the production quantity is large
enough and the size of the forging is small enough to permit forging in multiple-part dies, the impressions can be arranged
so that the side thrusts cancel one another out.
Fig. 13 Locked and counterlocked dies. (a) Locked dies with no means to
counteract side thrust. (b)
Counterlocked dies. (c) Dies requiring no counterlock because the forging has been rotated to minimize side
thrust
Generally, with optimum placement of the impression in the die, and with the clearance between the guides on the
hammer or press absorbing some side thrust, alignment between the upper and lower die impression can be maintained.
Sometimes, however, the methods suggested above are insufficient or unsuitable for maintaining the required alignment,
and it is necessary to counteract side thrust by machining mating projections and recesses (counterlocks) into the parting
surfaces of the dies.
Counterlocks can be relatively simple. A pin lock that consists of a round or square peglike section with a mating section
may be all that is required to control mismatch. Two such sections, or even sections at each corner of the die, may be
necessary. A simple raised section with a mating countersunk section running the width and the length of the die can
control side and end match. Counterlocks of these types should not be used in long production runs.
Counterlocks in high-production dies should be carefully designed and constructed. The height of the counterlock usually
is equal to, or slightly greater than, the depth of the locking portion of the die. The thickness of the counterlock should be
at least 1.5 times the height, so that it will have adequate strength to resist side thrust. Adequate lubrication of the sliding
surfaces is difficult to maintain, because of the temperature of the die and the heat radiated from the workpiece.
Therefore, the surfaces of the counterlock wear rapidly and need frequent reworking. Because of the cost of constructing
and maintaining counterlocks, they should be used only if a forging cannot be produced more economically without them.
To forge the connecting link shown in Fig. 13 requires a locked die because of the part shape. With the die design shown
in Fig. 13(a), side thrust is particularly large because of the angle at which the die faces meet the inclined portion of the
work metal. Because no means is provided to counteract side thrust, it is impossible to avoid mismatch of the upper and
lower dies. The position of the forging in the die in Fig. 13(b) is the same as in Fig. 13(a), but a counterlock is machined
into the die to counteract side thrust. With this arrangement, the possibility of mismatch is eliminated, but the cost of
making and maintaining the dies is high. Figure 13(c) shows a position of the forging in the die that is preferable for