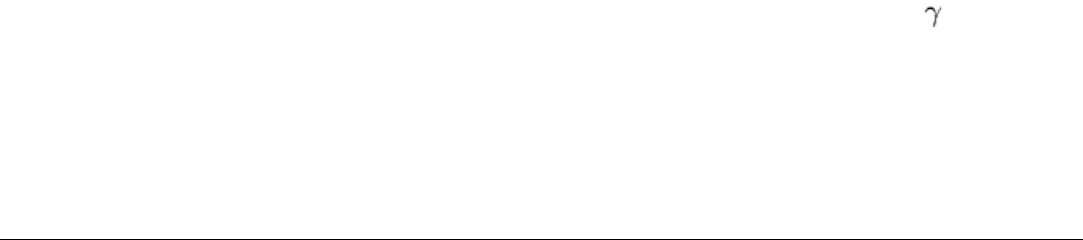
resistant alloys. Source: Ref 3, 4, 5, 6, 7, 8, and 9.
The nickel-base alloys are sensitive to minor variations in composition, which can cause large variations in forgeability,
grain size, and final properties. In one case, wide heat-to-heat variations in grain size occurred in parts forged from Alloy
901 (UNS N09901) in the same sets of dies. For some parts, optimal forging temperatures had to be determined for each
incoming heat of material by making sample forgings and examining them after heat treatment for variations in grain size
and other properties.
In the forging of nickel-base alloys, the forging techniques developed for one shape usually must be modified when
another shape is forged from the same alloy; therefore, development time is often necessary for establishing suitable
forging and heat-treating cycles. This is especially true for such alloys as Waspaloy (UNS N07001), Alloy 41 (UNS
N07041), U-500 (UNS N07500), and U-700.
Cobalt-Base Alloys. Many of the cobalt-base alloys cannot be successfully forged because they ordinarily contain
more carbon than the iron-base alloys and therefore greater quantities of hard carbides, which impair forgeability.
The two cobalt-base alloys listed in Table 1 are forgeable. The strength of these alloys at elevated temperatures, including
the temperatures at which they are forged, is considerably higher than that for iron-base alloys; consequently, the
pressures required in forging them are several times greater than those for the iron-base alloys.
Even when forged at its maximum forging temperature, Alloy-25 work hardens; therefore, forging pressure must be
increased with greater reductions. Accordingly, this alloy generally requires frequent reheating during forging to promote
recrystallization and to lower the forging pressure for subsequent steps.
Forging conditions (temperature and reduction) have a significant effect on the grain size of cobalt-base alloys. Because
low ductility, notch brittleness, and low fatigue strength are associated with coarse grains, close control of forging and of
final heat treatment is important.
Cobalt-base alloys are susceptible to grain growth when heated above about 1175 °C (2150 °F). They heat slowly and
require a long soaking time for temperature uniformity. Forging temperatures and reductions, therefore, depend on the
forging operation and the part design.
The alloys are usually forged with small reductions in initial breakdown operations. The reductions are selected to impart
sufficient strain to the metal so that recrystallization (and usually grain refinement) will occur during subsequent
reheating. Because the cross section of a partly forged section has been reduced, less time is required to reach temperature
uniformity in reheating. Consequently, because reheating time is shorter, the reheating temperature may sometimes be
increased 30 to 85 °C (50 to 150 °F) above the initial forging temperature without harmful effects. However, if the part
receives only small reductions in subsequent forging steps, forging should be continued at the lower temperatures. These
small reductions, in turn, must be in excess of about 5 to 15% to avoid abnormal grain growth during subsequent
annealing. The forging temperatures given in Table 1 are usually satisfactory.
Powder Alloys. Some alloys, such as Alloy IN-100 and Alloy 95, contain very high proportions of ', and their cast
ingots cannot be forged. Powders of these alloys, however, can be compacted by a number of techniques to produce
billets having a very fine grain structure. Such billets can then be superplastically forged. Pratt and Whitney Aircraft has
used its patented Gatorizing process to produce preforms for engine compressor and turbine disks with IN-100 billets. In
Gatorizing, which is a type of isothermal forging process, both the workpiece and the dies are maintained at 1175 °C
(2150 °F). Boron nitride is used as the lubricant. The process is done in vacuum in order to protect the heated dies from
oxidation. The use of Gatorizing has led to substantial reductions in material use and finish machining.
References cited in this section
1.
H.J. Henning, A.M. Sabroff, and F.W. Boulger, "A Study of Forging Variables," Report ML-TDR-64-
U.S. Air Force, 1964
2.
A.M. Sabroff, F.W. Boulger, and H.J. Henning, Forging Materials and Practices, Reinhold, 1968