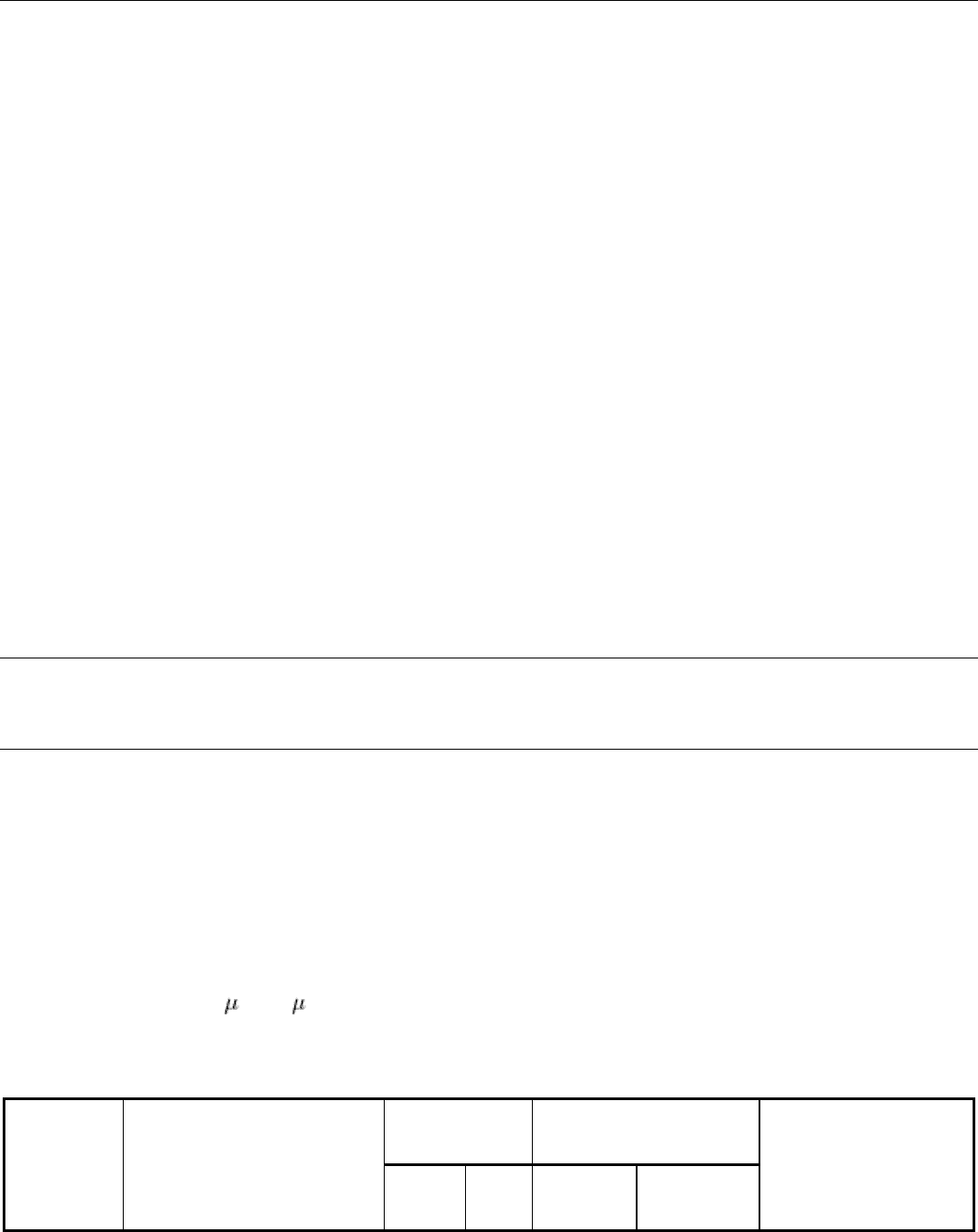
elongation. (d) Room-temperature impact energy. See also Fig. 26.
References cited in this section
70.
F.G. Hanejko, Mechanical Property Anisotropy of P/M Hot Formed Materials, Mod. Dev. Powder Metall.,
Vol 10, 1977, p 73
71.
Closed-Die Steel Forgings, in Properties and Selection: Irons and Steels, Vol 1, 9th ed., Metals Handbook,
American Society for Metals, 1978, p 357
72.
G.T. Brown, The Core Properties of a Range of Powder Forged Steels for Carburizing Applications,
Powder Metall., Vol 20 (No. 3), 1977, p 171
73.
G.T
. Brown and T.B. Smith, The Relevance of Traditional Materials Specifications to Powder Metal
Products, Mod. Dev. Powder Metall., Vol 7, 1974, p 9
74.
G.T. Brown, Properties and Prospects of Powder Forged Low Alloy Steels Related to Component
Production, in Powder Metallurgy: Promises and Problems, Société Française de Métallurgie--
Techniques, 1975, p 96
75.
W.J. Huppmann and G.T. Brown, The Steel Powder Forging Process--A General Review, Powder Metall.,
Vol 21 (No. 2), 1978, p 105
76.
"GKN Powder Forging Materials Specification and Properties," Issue 2, GKN PowderMet, April 1978
77.
D. Glover, A Ball/Rod Rolling Contact Fatigue Tester, in
Rolling Contact Fatigue Testing of Bearing
Steels, STP 771, J. Hoo, Ed., 1982, p 107
78.
S. Buzolits, "Military Process Specification for Type 46XX Powder-
Forged Weapon Components," Final
Technical Report AD-E401-376, U.S. Army Armament Research and Development Center, Aug 20, 1985
79.
S. Buzolits and T. Leister, "Military Specification for Type 10XX Powder-
Forged Weapon Components,"
Final Technical Report AD-E401-
412, U.S. Army Armament Research and Development Center, Oct 14,
1985
Powder Forging
W. Brian James, Michael J. McDermott, and Robert A. Powell, Hoeganaes Corporation
Quality Assurance for P/F Parts
Many of the quality assurance tests applied to wrought parts are similar to those used for powder forged parts. Among the
parameters specified are: part dimensions, surface finish, magnetic particle inspection, composition, density,
metallographic analysis, and nondestructive testing. These are discussed below.
Part Dimensions and Surface Finish. Typical tolerances for powder forged parts are summarized in Table 11. The
as-forged surface finish of a powder forged part is directly related to the surface finish of the forging tool. Surface finish
is generally better than 0.8 m (32 in.), which is better than that obtained on wrought forged parts. This good surface
finish is beneficial to the fatigue performance of P/F parts.
Table 11 Typical tolerances for powder forged parts
Typical tolerance
Minimum tolerance Dimension or
characteristic
Description
mm/mm
in./in. mm in.