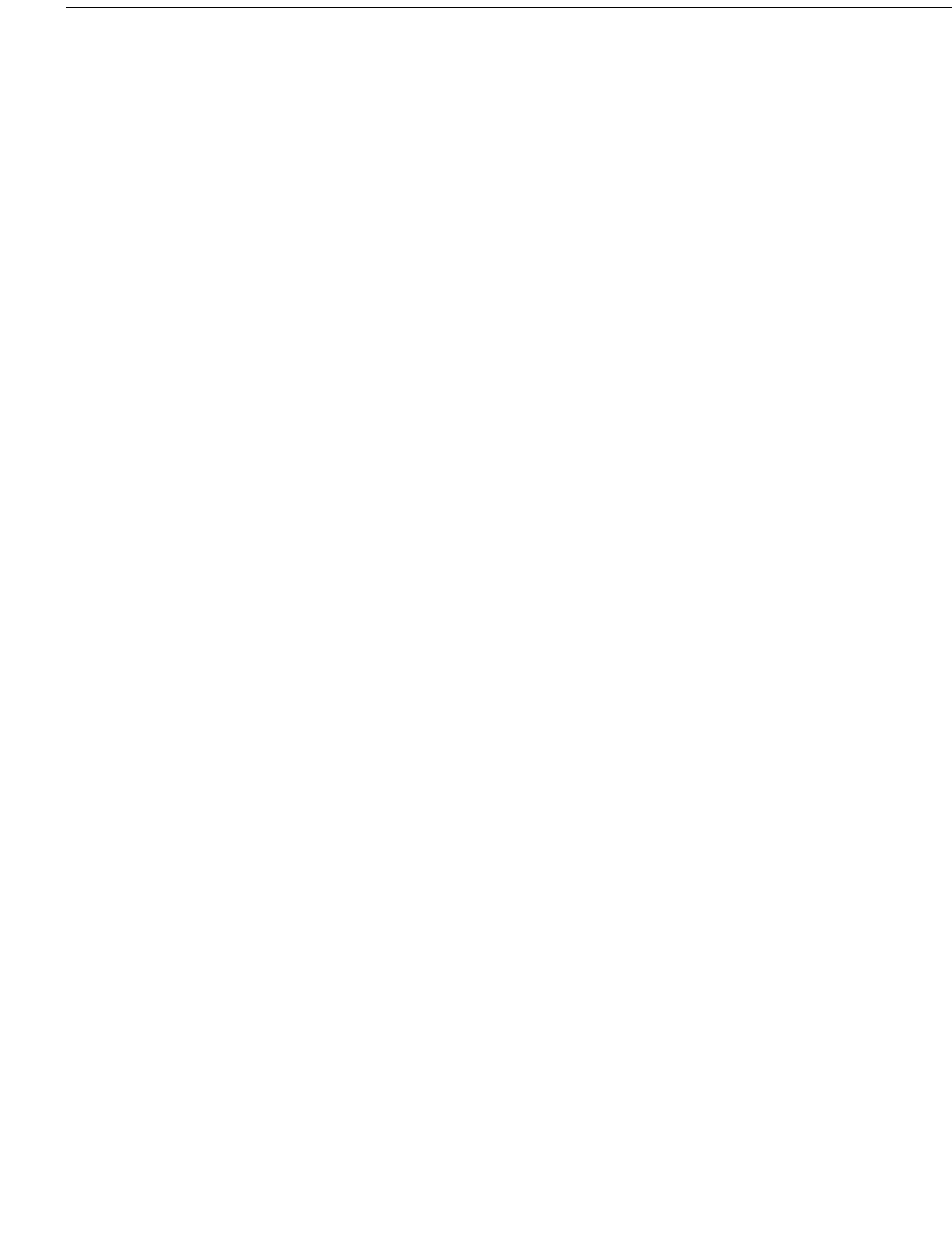
186 API STANDARD 618
where
C
KS
is the constant dependent on support stiffness units (SI units:
1
/130; USC units: 25);
A is the pipe cross-sectional metal area in mm
2
(in.
2
);
=
π
/4 × (OD
2
– ID
2
);
I is the pipe cross-sectional area moment of inertia in mm
4
(in.
4
);
=
π
/64 × (OD
4
– ID
4
);
OD is the pipe outer diameter in mm (in.);
ID is the pipe inner diameter in mm (in.);
f
n,T
is the minimum transverse natural frequency in Hz (see P 3.2.5);
n is the number of active supports (or n = 2 as a minimum, see P 3.2.7).
The actual value of k
s
should be determined and compared to the minimum k
s
requirement. When the actual ks is greater than
minimum k
s
there is sufficient support stiffness to constrain higher shaking forces (up to the limit defined by Equation 10 in
7.9.4.2.5.2.3.2 and P.1). When the actual k
s
is lower than minimum k
s
, the minimum mechanical natural frequency separation
margin guideline will not be met, and the possibility of operating on resonance within the first two orders of compressor speed
must be considered.
The actual and minimum k
s
values should also be compared with the range of typical support stiffness values found in Note 2 of
7.9.4.2.5.2.3. The actual k
s
should fall within the range of the corresponding support type. When the minimum k
s
required
exceeds the range of the corresponding support type, the actual k
s
must be carefully determined and either a sufficiently stiff type
of structure must be used or the shaking force guideline must be reduced.
P.3.2.2 When supports are not collinear with the pipe run where the shaking force is acting (such as the middle section of U, Z
or 3D bends), the perpendicular pipe sections clamped by the supports may be more flexible than the supports, and k
eff
must
correspondingly be reduced. Flexibility of the perpendicular pipe section should be considered when the support is offset greater
than 25% of the maximum acceptable span length.
P.3.2.3 The calculation of minimum k
s
does not include lumped masses, but results in a conservative shaking force criteria
when the separation margin minimum natural frequency guideline is satisfied. To ensure the separation margin criteria are
satisfied, the support requirements of each lumped mass, such as valves, must additionally be provided.
P.3.2.4 The calculation of minimum k
s
is based on the minimum number of supports required to satisfy the minimum
mechanical natural frequency guideline. When more than the minimum number of supports are present, the minimum k
s
can be
reduced by the ratio of the minimum number required divided by the number of active supports.
P.3.2.5 The minimum transverse natural frequency (f
n,T
) required is dependent on the frequency of the shaking force. For
example, to comply with the first part of the separation margin criteria, it is typically chosen as 2.4 times maximum rated speed.
In higher speed compressors, this is not always practical to achieve, however Equation P-2 can still be used to determine the
minimum support stiffness required for the given f
n,T
.
P.3.2.6 The minimum axial support stiffness requirements of vessels and equipment (such as secondary pulsation dampeners,
separators, cooler sections and heat exchangers) should be determined directly from the equipment mass to meet the separation
margin criteria.
P.3.2.7 The number of active supports include all axial restraints along the run containing the shaking force and restraints offset
from the run less than 25% of the maximum acceptable span length.
P.3.2.8 Vessels and equipment may also be restraints. See examples in Figure P-5.
P.3.2.9 Pipe wall thickness is specified based on design pressure using applicable design codes and is not increased as a method
to control vibration.
Copyright American Petroleum Institute
Provided by IHS under license with API
Licensee=IHS Employees/1111111001, User=Japan, IHS
Not for Resale, 01/01/2008 21:15:45 MST
No reproduction or networking permitted without license from IHS
--```,`,,,,`,``,,```,`,,`,,,,`-`-`,,`,,`,`,,`---