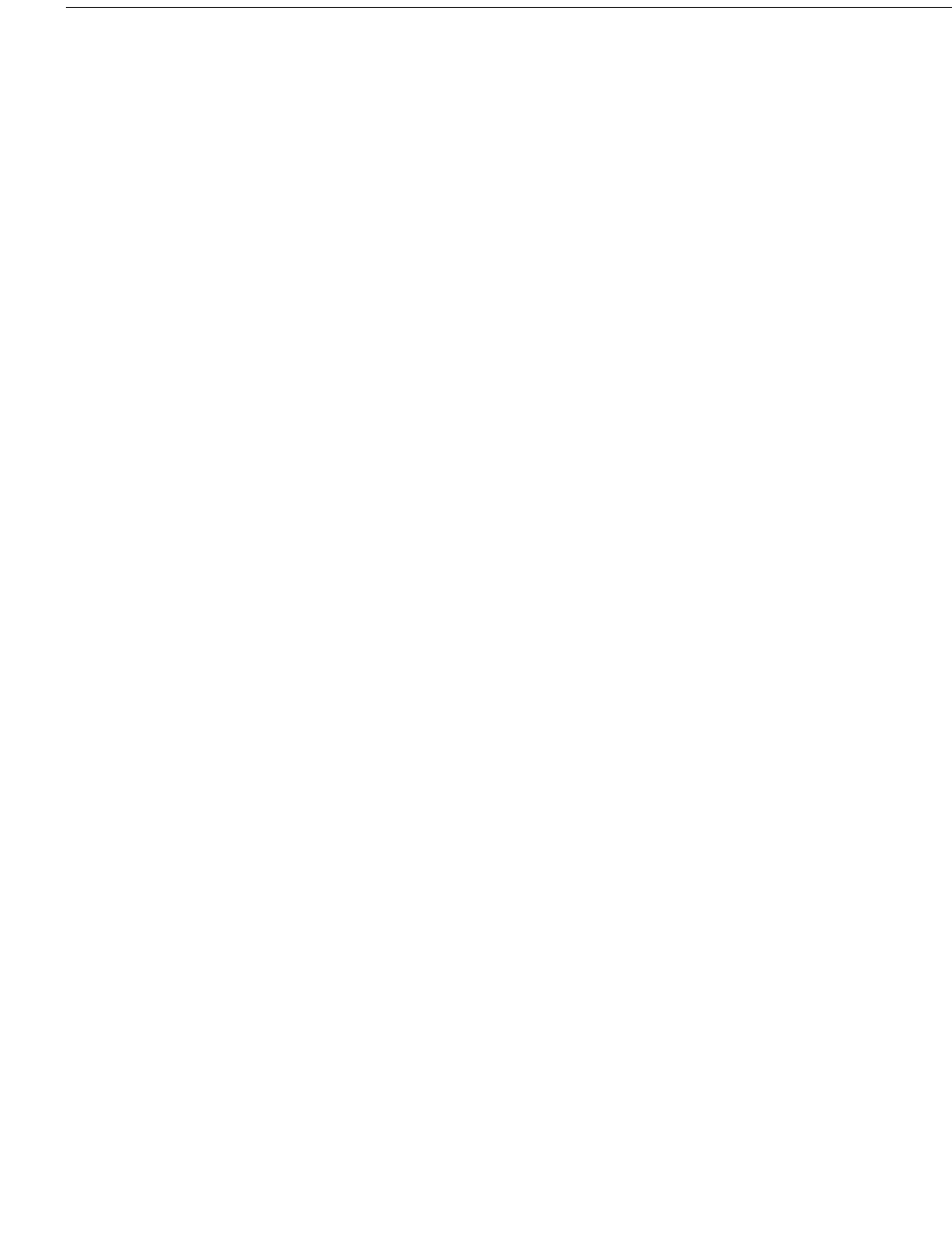
160 API STANDARD 618
I.5 Design Consideration
In addition to meeting the purposes described in I.2 the following factors should be considered when designing in designing a
distance piece vent, drain and buffer system:
a. Small diameter vent and drain piping will tend to foul and corrode over time, inhibiting their function. Consider using large
[e.g., DN 50 (NPS 2)] vent and drain headers and corrosion-resistant materials.
b. On two-compartment distance piece systems, external cross connections between the inner and outer compartment vents and
drains should be avoided.
c. On multiple machine systems, it should be possible to isolate each machine for maintenance.
d. Effective control of gas leakage requires the specification of gasketed solid metal covers on distance pieces (see 6.12.2.1).
e. Where vents, drains, liquid collection pots and distance pieces are connected to disposal systems, such as a flare or closed
drain system, they should be designed to withstand the maximum disposal system pressure (e.g., flare back pressure under
relieving conditions). See 6.12.2.3.
Note: Distance pieces are typically designed for a maximum gauge pressure of 2 bar (25 psi). Special designs are required for higher pressures.
f. Typically, the common vent and drain from the pressure packing (connection G in Figure I-1 and I-2) will be carrying a
mixture of liquid and gas. The system should be designed to separate these phases to avoid liquid blockage of the vent system.
g. Leaks from the stems of valve unloaders and clearance pockets may also need to be collected and controlled. These can be
integrated with the distance piece vent and drain system.
h. There is concern about the reliability of check valves in safety situations, particularly in low pressure systems such as distance
piece vent and drain systems where there is any mixture of gas and liquids. Check valve use should be avoided, where possible.
i. Except for the pressure packing combined vent and drain, which is a pressure driven flow, separate vent and drain lines are
necessary between the distance piece and liquid collection pot to pressure balance the system and allow free drainage. Sloped
headers, without pockets, assist draining.
j. Large diameter tubing [20 mm (
3
/4 in.) OD minimum] can be used between the individual distance pieces and the vent and
drain headers. This usually results in a neat, easily maintained installation compared to a piping system.
k. Manifolding and cross-connections with drains and blowoffs from other equipment should be avoided.
l. The buffer gas purge pressure must be limited to the maximum allowable pressure for the distance piece components (see
6.10.4). Some buffer gas will flow into the compressor frame. Frame venting must allow an outlet for this flow (see Figure G-5).
m. Pneumatic trip systems internal to the frame (e.g., crosshead pin temperature) should be energized with nitrogen rather than air
to assist in maintaining an inert atmosphere in the crankcase.
n. Effective establishment of an inert atmosphere in the crankcase will necessitate special maintenance safety procedures.
o. Where climatic conditions require, drains should be heat-traced and insulated.
p. Under total packing failure, it should not be possible to over-pressure the distance piece (see 6.10.4 and 6.10.5). If the vent area
is not sufficient, additional venting to a safe location by way of emergency pressure relief valves or spring-loaded pressure relief
doors may be required.
q. Buffer gas purge rates are typically sized for a flow rate of 0.03 m
3
/h (10 standard ft
2
/h) per packing set [may reach 0.2 m
3
/h
(65 standard ft
2
/h) per packing set on startup] and are fitted with flow indicators.
Copyright American Petroleum Institute
Provided by IHS under license with API
Licensee=IHS Employees/1111111001, User=Japan, IHS
Not for Resale, 01/01/2008 21:15:45 MST
No reproduction or networking permitted without license from IHS
--```,`,,,,`,``,,```,`,,`,,,,`-`-`,,`,,`,`,,`---