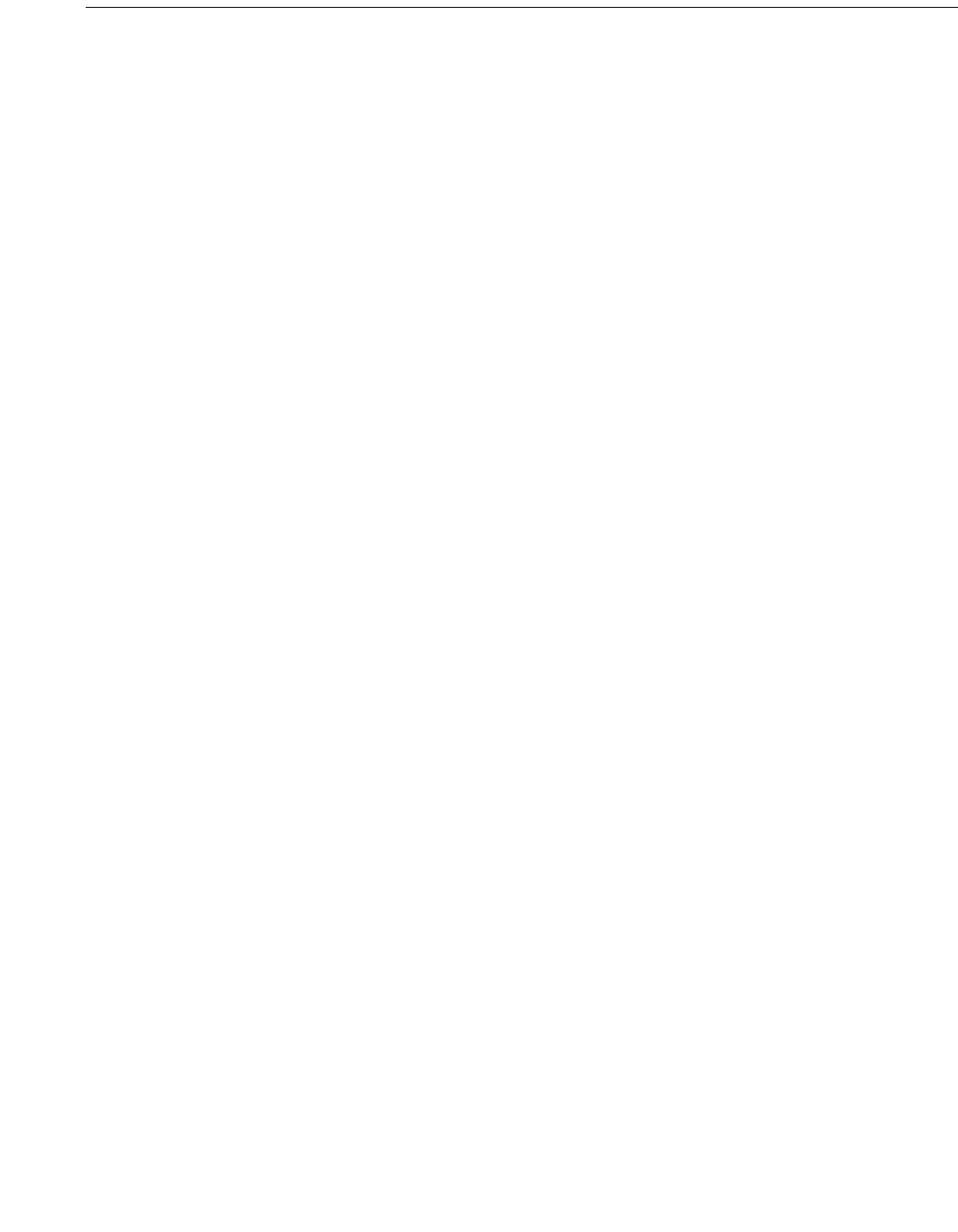
RECIPROCATING COMPRESSORS FOR PETROLEUM, CHEMICAL, AND GAS INDUSTRY SERVICES 141
2. Foundation plan including:
a. Dimensions of mounting plates for the complete train and auxiliary systems complete with diameter, number and location of
bolt holes and thickness of metal through which bolts must pass.
b. Speed, critical speed (if any),
c. Location and direction in the x, y, z-coordinate system of static and the first and second order dynamic (unbalanced) forces
and moments.
d. Location of the center of mass.
e. Leveling jackscrew location.
3. Allowable flange loading (either cylinder or pulsation suppression device) and coordinates (see 6.6.5). Allowable flange
loading(s) for all cylinder (or pulsation bottle) connections, including anticipated thermal movements referenced to a defined
point, and x, y, z-coordinate system.
4. Driver outline. Certified dimensional outline drawing for the driver and all its auxiliary equipment including:
a. Size, location, orientation and purpose of all customer connections, including conduit boxes, conduit, instrumentation and
any piping or ducting.
b. Type, rating and facing for any flanged connections.
c. Size and location of anchor bolt holes and leveling jackscrews and thickness of sections through which bolts must pass.
d. Total mass of each Item of equipment (driver and auxiliary equipment). plus loading diagrams, heaviest weight, and name of
the part.
e. Overall dimensions and all horizontal and vertical clearances necessary for dismantling and the approximate location of
lifting lugs.
f. Shaft center line height.
g. Shaft end dimensions, plus tolerances for the coupling.
h. Direction of rotation.
5. Drive arrangement drawing, including, but not limited to the following:
a. Flywheel data.
b. Driver and mechanical transmission mass.
c. Moments of inertia.
d. Stator shift.
e. Air gap.
6. Dimensional outline for all vendor supplied major accessory equipment.
7. Performance data (see 9.3.3.1).
8. Pressure packing drawing(s). (One for each packing type.)
9. Gas load, rod load and crosshead load reversal and duration charts (see 9.3.3.2).
10. Starting torque versus speed curves. (For driver and compressor—on the same chart.) Acceleration time (see 9.3.3.5).
11. Motor driver performance characteristics and performance data including:
a. For induction motors 150 kW (200 hp) and smaller:
1. Efficiency and power factors at one-half, three-quarter and full load.
2. Speed-torque curves.
b. For induction motors larger than 150 kW (200 hp), certified test reports for all tests run and performance curves as follows:
1. Time-current heating curve.
2. Speed-torque curves at 70%, 80%, 90% and 100% of rated voltage.
3. Efficiency and power factor curves from 0 to rated service factor.
4. Current versus load curves from 0% – rated service factor.
5. Current versus speed curves from 0% – 100% of rated speed.
6. Permissible safe stall time and repeated start capability (hot and cold).
c. For synchronous motors.
1. Speed-torque, current-speed and power factor-speed curves at 70%, 80%, 90% and 100% of rated voltage.
2. Pull-in and pull-out torque.
3. Permissible safe stall time and repeated start capability (hot and cold).
4. Efficiency and power factor curves from 0 to rated service factor.
Copyright American Petroleum Institute
Provided by IHS under license with API
Licensee=IHS Employees/1111111001, User=Japan, IHS
Not for Resale, 01/01/2008 21:15:45 MST
No reproduction or networking permitted without license from IHS
--```,`,,,,`,``,,```,`,,`,,,,`-`-`,,`,,`,`,,`---