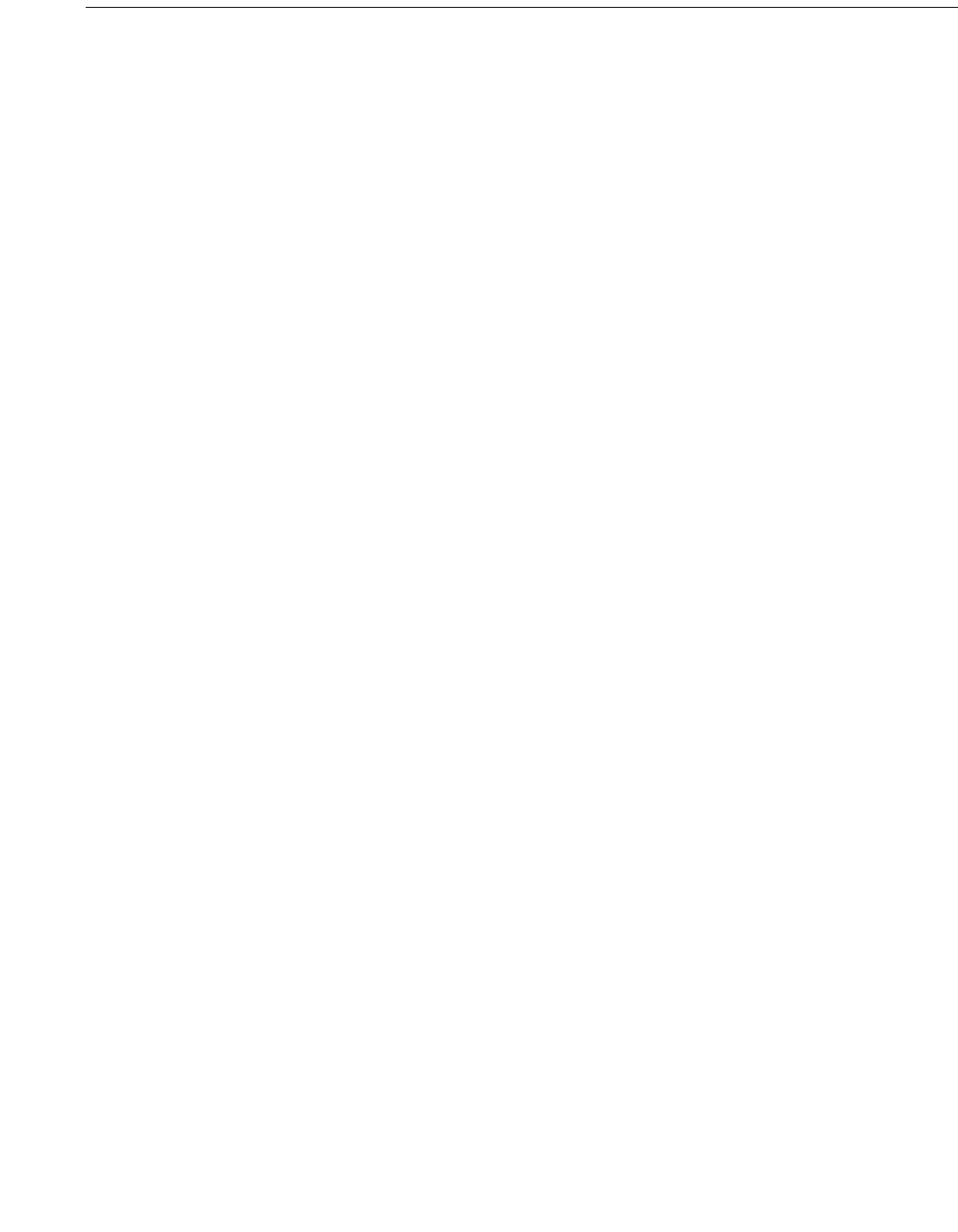
RECIPROCATING COMPRESSORS FOR PETROLEUM, CHEMICAL, AND GAS INDUSTRY SERVICES 123
C.5.4 For correct vertical rod runout calculations, it is important to use actual measured running clearances for the cylinder and
crosshead, as well as the actual measured dimensions of the dial indicator locations along the top of the piston rod. Correct rod
lengths as required by Figure C-6A are also important.
C.5.5 Rod runout should always be measured starting with the rod at the extreme end of the stroke, with the piston at the crank
end of the cylinder. The dial indicators should be zeroed. Manual bar-over should be such that the connecting rod runs over (that
is, over the top on the outstroke) as the crosshead, piston rod, and piston are stroked slowly outward toward the end of the stroke
at the head end of the cylinder. Dial indicator readings are observed during the stroke and recorded at the end of the stroke. If this
method, and the dial indicator positions noted in C.5.3 are used as the standard measurement procedure, then field runout readings
can be properly compared and evaluated with factory runout readings provided in Figure C-3.
C.5.6 The dimensions shown in Figure C-1, Figure C-2, Figure C-5, and used in Figure C-6B for the calculation example, were
selected for convenience in illustrating basic runout geometry and principles. Dimensions for actual compressors may vary
greatly from the illustration dimensions, while some may be close or identical. Since vertical rod runout will vary according to
stroke, rod length, rod sag, and the difference in running clearances between the crosshead and cylinder, different compressors
with different cylinder configurations may have significantly different vertical runout readings for conditions of perfect
alignment.
C.5.7 Excessive rod runout is corrected by realignment and/or squaring up some or all components involved. These may
include cylinders, liners, heads, distance pieces, crossheads and crosshead guides, and rods and pistons. Crosshead threads and
face, piston rod nut threads and face, and piston rod threads may have to be checked and corrected for perpendicularity. As a
check for squareness at the interface of the crosshead and piston rod, both horizontal and vertical runout should be checked first
with the crosshead nut loose and then tight. Certain conditions of excessive rod runout at the packing case can further be
evaluated by placing an dial indicator on the rod in the cylinder through a crank end valve port to verify full length liner
concentricity with the cylinder bore and/or cylinder crank end face squareness with the bore. With a dial indicator in the cylinder,
full stroke runout cannot be taken since the dial indicator takes up some of the space between the crank-end head and the piston.
However, the available stroke is sufficient to get a suitable reading to determine alignment status
C.6 Horizontal Runout
Horizontal runout readings can be used as a direct indication of the horizontal alignment from the crosshead through the distance
pieces to the cylinder. No calculations are necessary, as horizontal runout should be within the zero limits regardless of whether
the unit is cold or hot, or of the axial location of the dial indicator along the side of the rod. It is measured by placing dial
indicators on the side of the rod as close as possible to the crosshead and the pressure packing case at the locations noted in C.5.2,
and shown in Figure C-6A. For perfect alignment, the dial indicators should read zero as the rod is moved slowly through the
entire length of the stroke during manual bar-over. The best indication of perfect horizontal alignment is when horizontal rod
runout measures zero with dial indicators set at both the crosshead end and the piston end of the rod, in other words, as close to the
packing case as possible. See 6.1.28 for allowable limit.
C.7 Vertical Runout
C.7.1 COLD RUNOUT
Cold vertical runout readings other than zero are not necessarily an indication of misalignment. When all components are
perfectly aligned, the normal cold vertical rod runout is the result of the difference between the cold running clearance of the
piston in the bore and that of the crosshead in the crosshead guide, plus the effect of normal rod sag, the length of the stroke, the
length of the rod, and the location of the dial indicators along the top of the rod. It is, therefore, important that the actual running
clearances for the cylinder and crosshead are used for the calculations, as well as the rod lengths and actual dial indicator locations
shown in Figure C-6A.
C.7.2 BASIC GEOMETRY
The basic geometry is illustrated in Figures C-1 and C-2. Piston and crosshead centerlines lie below the perfect alignment
centerline by one half of the running clearances. In cylinders where the running clearance is greater (or less) than the crosshead
running clearance, the piston will lie below (or above) the crosshead centerline by one half of the difference in the cold running
clearances. The result is basic vertical rod runout that is normally something other than zero for perfect alignment. This one-half
Copyright American Petroleum Institute
Provided by IHS under license with API
Licensee=IHS Employees/1111111001, User=Japan, IHS
Not for Resale, 01/01/2008 21:15:45 MST
No reproduction or networking permitted without license from IHS
--```,`,,,,`,``,,```,`,,`,,,,`-`-`,,`,,`,`,,`---