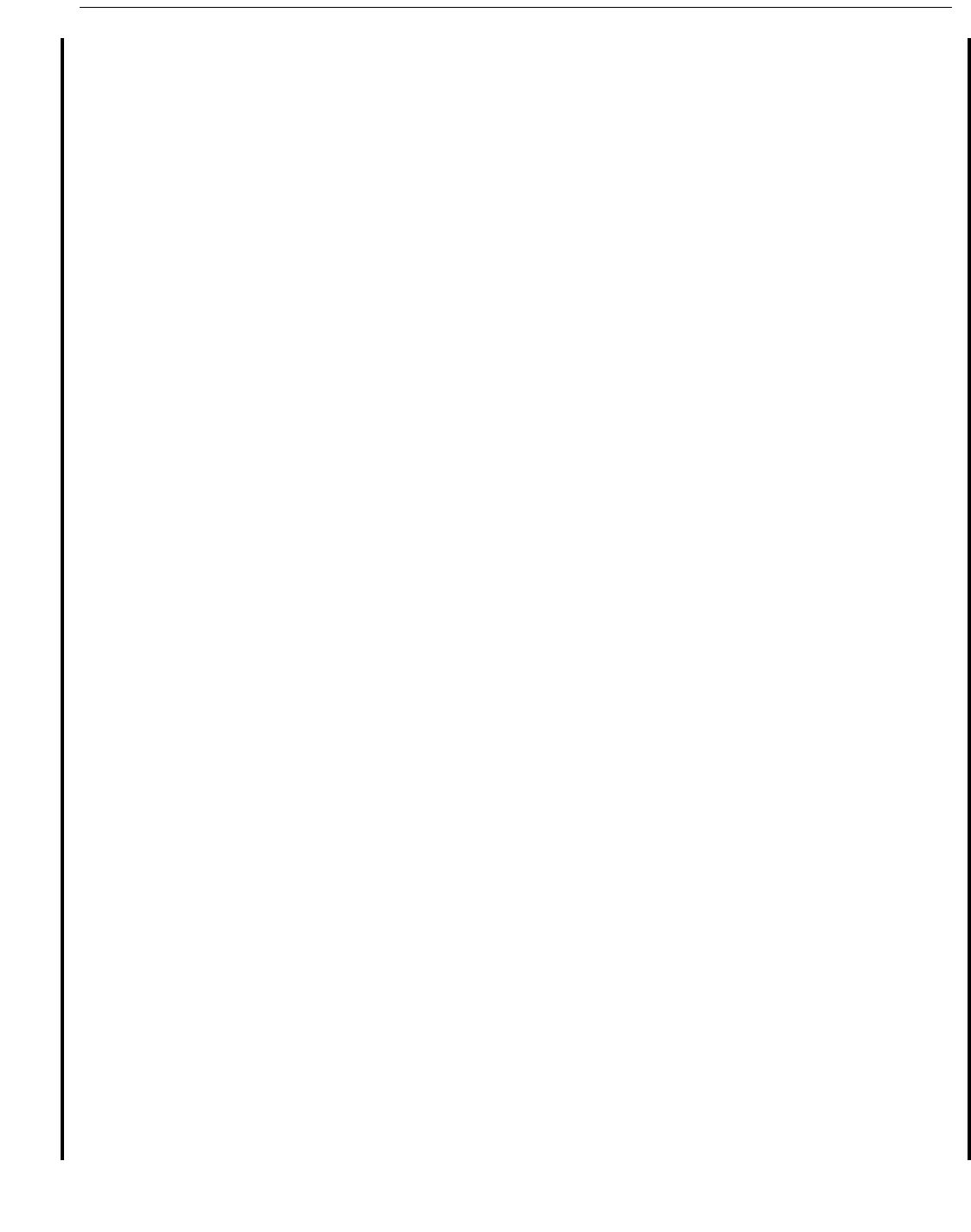
RECOMMENDED PRACTICE FOR PLANNING, DESIGNING AND CONSTRUCTING FIXED OFFSHORE PLATFORMS—WORKING STRESS DESIGN 47
from the actual structure could be required. If the through-
thickness toughness of joint can steel is ill-defined, inspection
for possible cracks or lamellar tearing should be considered.
Section 8.4.1 contains recommendations for grout materi-
als (for use in grouted joints).
4.2.2 Design Loads and Joint Flexibility
The adequacy of the joint may be determined on the basis
of nominal loads in both the brace and chord.
Reductions in secondary (deflection induced) bending
moments or inelastic relaxation through the use of joint elas-
tic stiffness’ may be considered, and for ultimate strength
analysis of the platform, information concerning the force-
deformation characteristics for joints may be utilized. These
calculations are dependent on the joint type, configuration,
geometry, material properties, and load case and, in certain
instances, hydrostatic pressure effects. See Commentary for a
further discussion.
4.2.3 Minimum Capacity
The connections at the ends of tension and compression
members should develop the strength required by design
loads, but not less than 50% of the effective strength of the
member. The effective strength is defined as the buckling
load for members loaded in either tension or compression,
and as the yield load for members loaded primarily in tension.
Welds in connections at the ends of tubular members
should be in accordance with 11.1.3 or should not be less than
required to develop a capacity equal to the lesser of:
1. Strength of the branch member based on yield, or
2. Strength of the chord based on basic capacity Equa-
tions 4.3-1a and 4.3-1b. (where applicable).
4.2.4 Joint Classification
Joint classification is the process whereby the axial load in
a given brace is subdivided into K, X, and Y components of
loading corresponding to the three joint types for which
capacity equations exist. Such subdivision normally consid-
ers all of the members in one plane at a joint. For purposes of
this provision, brace planes within ±15 degrees of each other
may be considered as being in a common plane. Each brace
in the plane can have a unique classification that could vary
with load condition. The classification can be a mixture
between the above three joint types. Once the breakdown into
axial components is established, the capacity of the joint can
be estimated using the procedures in Section 4.3.
Figure 4.2-1 provides some simple examples of joint clas-
sification. For a brace to be considered as K-joint classifica-
tion, the axial load in the brace should be balanced to within
10% by loads in other braces in the same plane and on the
same side of the joint. For Y-joint classification, the axial load
in the brace is reacted as beam shear in the chord. For X-joint
classification, the axial load in the brace is transferred
through the chord to the opposite side (e.g., to braces,
padeyes, launch rails).
Case (h) in Figure 4.2-1 is a good example of the loading
and classification hierarchy that should be adopted in the
classification of joints. Replacement of brace load by a com-
bination of tension and compression load to give the same net
load is not permitted. For example, replacing the load in the
horizontal brace on the left hand side of the joint by a com-
pression load of 1000 and tension load of 500 is not permitted
as this may result in an inappropriate X classification for this
horizontal brace and a K classification for the diagonal brace.
Special consideration should be given to establishing the
proper gap if a portion of the load is related to K-joint behav-
ior. The most obvious case in Figure 4.2-1 is (a), for which
the appropriate gap is between adjacent braces. However, if
an intermediate brace exists, as in case (d), the appropriate
gap is between the outer loaded braces. In this case, since the
gap is often large, the K-joint capacity could revert to that of a
Y joint. Case (e) is instructive in that the appropriate gap for
the middle brace is gap 1, whereas for the top brace it is gap
2. Although the bottom brace is treated as 100% K classifica-
tion, a weighted average in capacity is required, depending on
how much of the acting axial load in this brace is balanced by
the middle brace (gap 1) and how much is balanced by the top
brace (gap 2).
There are some instances where the joint behavior is more
difficult to define or is apparently worse than predicted by the
above approach to classification. Two of the more common
cases in the latter category are launch truss loading and in-situ
loading of skirt pile-sleeves. Some guidance for such
instances is given in the Commentary.
4.2.5 Detailing Practice
Joint detailing is an essential element of joint design. For
unreinforced joints, the recommended detailing nomenclature
and dimensioning is shown in Figures 4.2-2 and 4.2-3. This
practice indicates that if an increased chord wall thickness (or
special steel) is required, it should extend past the outside edge
of incoming bracing a minimum of one quarter of the chord
diameter or 12 inches (300 mm), whichever is greater. Even
greater lengths of increased wall thickness or special steel may
be needed to avoid downgrading of joint capacity per Section
4.3.5. If an increased wall thickness of brace or special steel is
required, it should extend a minimum of one brace diameter or
24 inches (600 mm), whichever is greater. Neither the cited
chord can nor brace stub dimension includes the length over
which the 1:4 thicknesses taper occurs. In
situations where
fatigue considerations can be important, tapering on the inside
may have an undesirable consequence of fatigue cracking orig-
inating on the inside surface, and be difficult to inspect.
Copyright American Petroleum Institute
Provided by IHS under license with API
Licensee=Indonesia location/5940240008
Not for Resale, 10/22/2008 00:07:12 MDT
--`,,```,,,`,,,,,,,,,,,,,,`,``,`-`-`,,`,,`,`,,`---