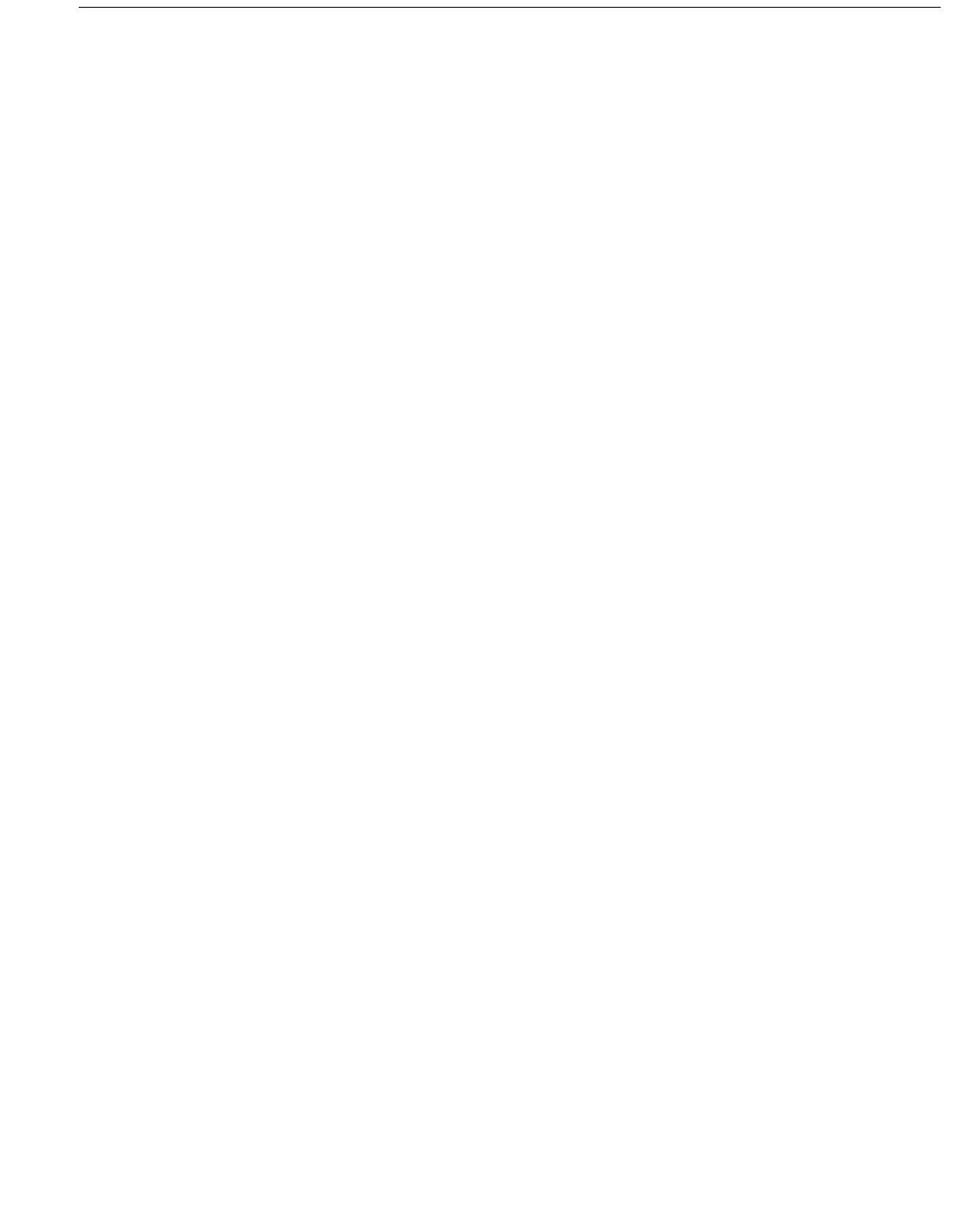
RECOMMENDED PRACTICE FOR PLANNING, DESIGNING AND CONSTRUCTING FIXED OFFSHORE PLATFORMS—WORKING STRESS DESIGN 269
Vessel supports should remain integral at least until process
blowdown is complete.
Stringers to which equipment is attached may have signifi-
cantly different natural periods than the surrounding struc-
ture. Their dynamic response may therefore need to be
assessed separately.
C18.9 ACCIDENTAL LOADING
C18.9.1 General
The following commentary presents general guidance and
information for consideration of vessel collision.
C18.9.2 Vessel Collision
All exposed elements at risk in the collision zone of an
installation should be assessed for accidental vessel impact
during normal operations.
The collision zone is the area on any side of the platform
that a vessel could impact in an accidental situation during
normal operations. The vertical height of the collision zone
should be determined from considerations of vessel draft,
operational wave height and tidal elevation.
Elements carrying substantial dead load (that is, knee
braces), except for platform legs and piles, should not be
located in the collision zone. If such elements are located in
the collision zone they should be assessed for vessel impact.
C18.9.2a Impact Energy
The kinetic energy of a vessel can be calculated using
Equation C18.9.2-1.
E = 0.5 a m v
2
(C18.9.2-1)
Where:
E = the kinetic energy of the vessel,
a = added mass factor,
= 1.4 for broadside collision,
= 1.1 for bow/stern collision,
m = vessel mass,
v = velocity of vessel at impact.
The added mass coefficients shown are based on a ship-
shaped or boat-shaped hull.
For platforms in mild environments and reasonably close
to their base of supply, the following minimum requirements
should be used, unless other criteria can be demonstrated:
Vessel Mass = 1,100 short tons (1,000 metric tons)
Impact Velocity = 1.64 feet/second (0.5 meters/second)
The 1100-short-ton vessel is chosen to represent a typical
180-200-foot-long supply vessel in the U.S. Gulf of Mexico.
For deeper and more remote locations, the vessel mass and
impact velocity should be reviewed and increased where nec-
essary. In shallow areas, it may be possible to reduce this cri-
teria where access to the platform is limited to small
workboats.
18.9.2b Energy Absorption
An offshore structure will absorb energy primarily from
the following:
a. Localized plastic deformation (that is, denting) of the
tubular wall.
b. Elastic/plastic bending of the member.
c. Elastic/plastic elongation of the member.
d. Fendering device, if fitted.
e. Global platform deformation (that is, sway).
f. Ship deformation and/or rotation.
In general, resistance to vessel impact is dependent upon
the interaction of member denting and member bending. Plat-
form global deformation may be conservatively ignored. For
platforms of a compliant nature, it may be advantageous to
include the effects of global deformation.
C18.9.2c Damage Assessment
Two cases should be considered:
1. Impact (energy absorption and survival of platform).
2. Post-impact (platform to meet post-impact criteria).
Primary framework should be designed and configured to
absorb energy during impact, and to control the consequences
of damage after impact. Some permanent deformation of
members may be allowable in this energy absorption.
The platform should retain sufficient residual strength after
impact to withstand the one-year environmental storm loads
in addition to normal operating loads. Special attention
should be given to defensible representation of actual stiff-
ness of damaged members or joints in the post-impact assess-
ment. Damaged members may be considered totally
ineffective providing their wave areas are modeled in the
analyses.
Where adequate energy absorption can be calculated for
individual members, further checking is not required. In cases
where very stiff members (grouted legs or members) cause
the main energy absorption to be in the vessel, the supporting
braces for the member, the joints at each end of the member,
and the adjacent framing members should be checked for
structural integrity resulting from the impact loads.
Bracing members: A number of research studies have
been performed to evaluate the force required to locally dam-
age tubular members [2, 3]. O. Furnes [3], reported on these
experimental test results and found the relationship between
force and dent depth to be:
Copyright American Petroleum Institute
Provided by IHS under license with API
Licensee=Indonesia location/5940240008
Not for Resale, 10/22/2008 00:07:12 MDT
No reproduction or networking permitted without license from IHS