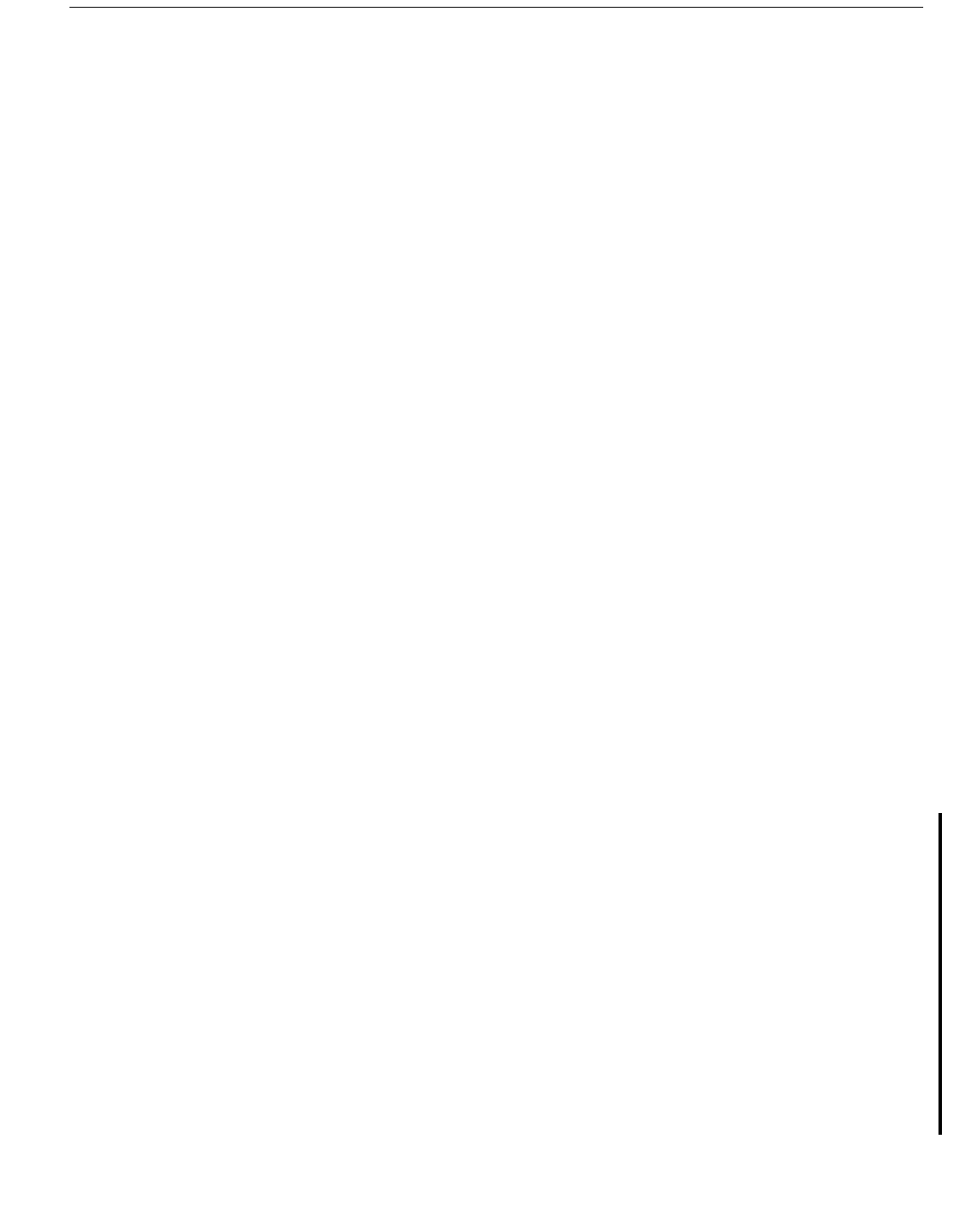
258 API RECOMMENDED PRACTICE 2A-WSD
level (design level analysis) allows recognition of the work-
ing strength of a member or joint within the elastic range
using current technology. The third level (ultimate strength
analysis) recognizes the full strength of the platform structure
to demonstrate adequacy and stability.
C17.7.2 Design Level Analysis Procedures
C.17.7.2a General
It should be noted that the design level analysis criteria
provided in Section 17.6 were calibrated for structures that
did not have wave loading on their decks. It is therefore
unconservative to consider wave loading on decks for assess-
ments using design level analysis. Ultimate strength analysis
is required instead, using the higher environmental criteria
contained in Section 17.6. Note that for some wave-in-deck
loading, only a linear global analysis will be necessary (see
Section 17.7.3a).
C.17.7.2b Structural Steel Design
Should ongoing research be used to determine the strength
of members, it must be carefully evaluated to assure applica-
bility to the type of member, its level of stress, and the level
of confidence in the conclusions of the research. For exam-
ple, the use of smaller values for effective length (K) factors
might be appropriate for members developing large end
moments and high levels of stress, but might not be appropri-
ate for lower levels of stress.
Because of availability and other nonstructural reasons,
members could have steel with yield stress higher than the
specified minimum. If no such data exist, tests can be used
to determine the actual yield stress. Joint industry studies
have indicated that higher yield stresses can be justified sta-
tistically.
C.17.7.2c Connections
Joints are usually assumed rigid in the global structural
model. Significant redistribution of member forces can result
if joint flexibility is accounted for, especially for short brac-
ing with small length-to-depth ratios, and for large leg can
diameters where skirt piles are used. Joint flexibility analysis
may use finite element methods as appropriate. Steel joints
can have higher strength than currently accounted for. Simi-
larly, the evaluation of strength for grouted joints, as well as
the assessment of grout stiffness and strength, may consider
higher values than normally used for design.
C.17.7.2d Fatigue
All offshore structures, regardless of location, are subject
to fatigue degradation. In many areas, fatigue is a major
design consideration due to relatively high ratios of opera-
tional seastates to maximum design environmental events. In
the U.S. Gulf of Mexico, however, this ratio is low. Still,
fatigue effects should be considered and engineering deci-
sions should be consciously based on the results of any
fatigue evaluations.
Selection of critical areas for any Level III and/or IV
inspections should preferably be based on factors such as
joint and member loads, stresses, stress concentration, struc-
tural redundancy, and fatigue lives as determined by platform
design.
In the U.S. Gulf of Mexico, Level III and/or IV underwater
surveys may be considered adequate if they indicate no
fatigue cracks. Should cracks be indicated, no further analysis
is required if these are repaired. The use of analytical proce-
dures for the evaluation of fatigue can be adequate if only
Level II survey is done.
C17.7.3 Ultimate Strength Procedures
It should be noted that limited structural damage is accept-
able and that the more severe environmental loading as noted
in Section 17.6 is required.
In ultimate strength analysis, structural elements are
allowed to carry loads up to their ultimate capacities, they can
continue to carry load after reaching those capacities, depend-
ing on their ductility and post-elastic behavior. Such elements
may exhibit signs of damage, having crossed over buckling
or inelastic yielding. In this context, damage is acceptable as
long as the integrity of the structure against collapse is not
compromised.
Since structures do not usually develop overload stresses in
most of their elements at one time, the need to perform com-
plex ultimate strength analyses for the whole structure might
not be justified for a few overloaded elements, thus the need
to distinguish between local and global overloading.
An efficient approach to ultimate capacity assessment is to
carry it out in a step-wise procedure as follows: (a) perform a
linear global analysis to determine whether nonlinearity is a
local or a global problem, and (b) perform local or global ulti-
mate strength analysis as required.
As an alternative to a nonlinear assessment such as a push-
over analysis, it may be possible to demonstrate that the plat-
form will pass the ultimate strength assessment by using a
linear elastic analysis, similar to a design level analysis, with
the exception that the typical factors of safety associated with
axial, bending, shear and other loading conditions have been
removed. Other known sources of conservatism such as the
use of mean yield strength instead of nominal yield strength
may also be taken into account. The intent is to approximate
performance of the platform members when loads are above
allowable stress but below actual yield or buckling. If all of
the platform members can be shown to remain elastic, consid-
ering all combined stress states, then the platform passes the
ultimate strength assessment. If the load in a platform mem-
ber or members exce
eds yield, then a nonlinear ultimate
strength analysis should be utilized.
Copyright American Petroleum Institute
Provided by IHS under license with API
Licensee=Indonesia location/5940240008
Not for Resale, 10/22/2008 00:07:12 MDT
No reproduction or networking permitted without license from IHS