Подождите немного. Документ загружается.
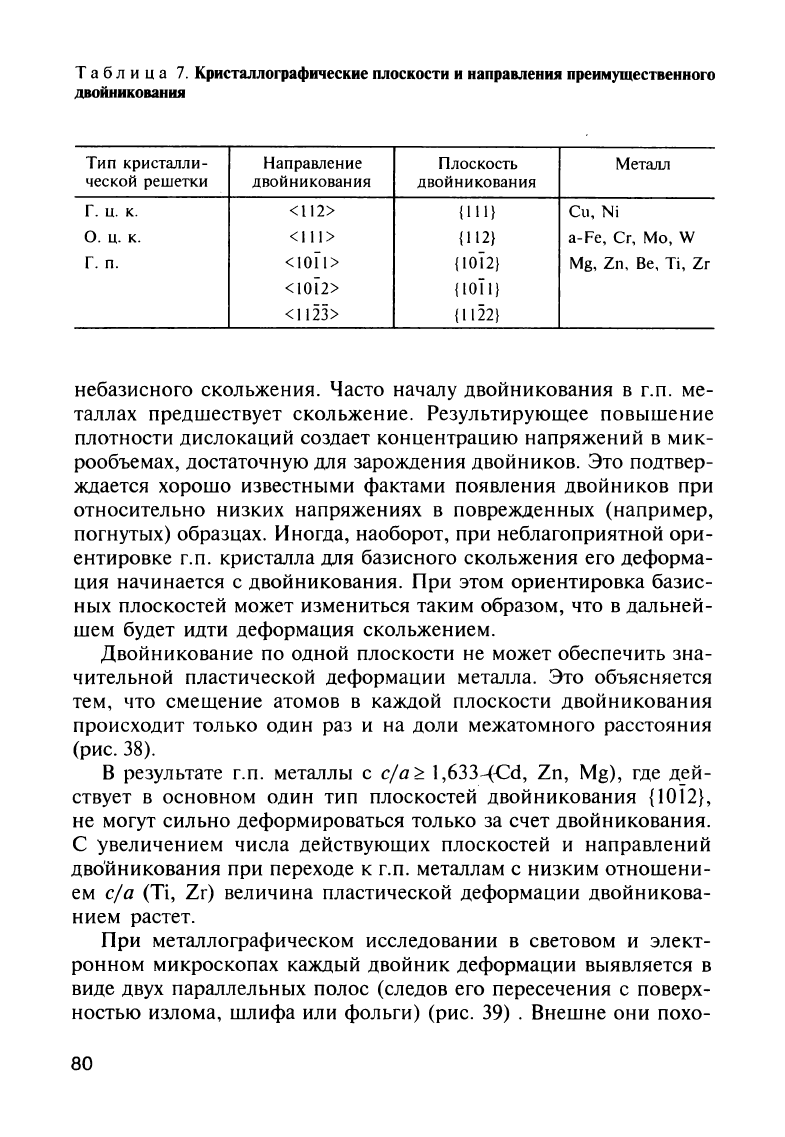
Т
а
б
л
и
ц
а
7.
Кристаллоrpафические
плоскости
и
направления
преимущественноrо
двойникования
Тип
кристалли-
Направление
Плоскость
Металл
ческой
решетки
двойникования
двойникования
г. ц.
к.
<112>
{111}
Св,
Ni
о.
ц.
к.
<111>
{112}
a-Fe,
Сг,
Мо,
W
г.
п.
<1011>
{IOI2}
Mg,
Zn,
Ве,
Ti,
Zr
<1012>
{1011}
<1123>
{1122}
небазисного
скольжения.
Часто
началу
двойникования
в
Г.П.
ме
таллах
предшествует
скольжение.
Результирующее
повышение
плотности
дислокаций
создает
концентрацию
напряжений
в
мик
рообъемах,
достаточную
для
зарождения
двойников.
Это
подтвер
ждается
хорошо
известными
фактами
появления
двойников
при
относительно
низких
напряжениях
в
поврежденных
(например,
погнутых)
образцах.
Иногда,
наоборот,
при
неблагоприятной
ори
ентировке
Г.П.
кристалла
для
базисного
скольжения
его
деформа
ция
начинается
с
двойникования.
При
этом ориентировка
базис
ных
плоскостей
может
измениться
таким
образом,
что
в
дальней
шем
будет
идти
деформация
скольжением.
Двойникование
по
одной
плоскости
не
может
обеспечить
зна
чительной
пластической
деформации
металла.
Это
объясняется
тем,
что
смещение
атомов
в
каждой
плоскости
двойникования
происходит
только
один
раз
и на
доли
межатомного
расстояния
(рис.
38).
В
результате
г.п.
металлы
с
c/a~
1,633--(Cd, Zn, Mg),
где
дей
ствует
в
основном
один
тип
плоскостей
двойникования
{10I2},
не могут
сильно
деформироваться
только
за
счет
двойникования.
С
увеличением
числа
действующих
плоскостей
и
направлений
дво'йникования
при
переходе
к
г.п.
металлам
с
низким
отношени
ем
с/а
(Ti, Zr)
величина
пластической
деформации
двойникова
нием
растет.
При
металлографическом
исследовании
в
световом
и
элект
ронном
микроскопах
каждый
двойник
деформации
выявляется
в
виде
двух
параллельных
полос
(следов
его
пересечения
с
поверх
ностью
излома,
шлифа
или
фольги)
(рис.
39)
.
Внешне
они
похо-
80
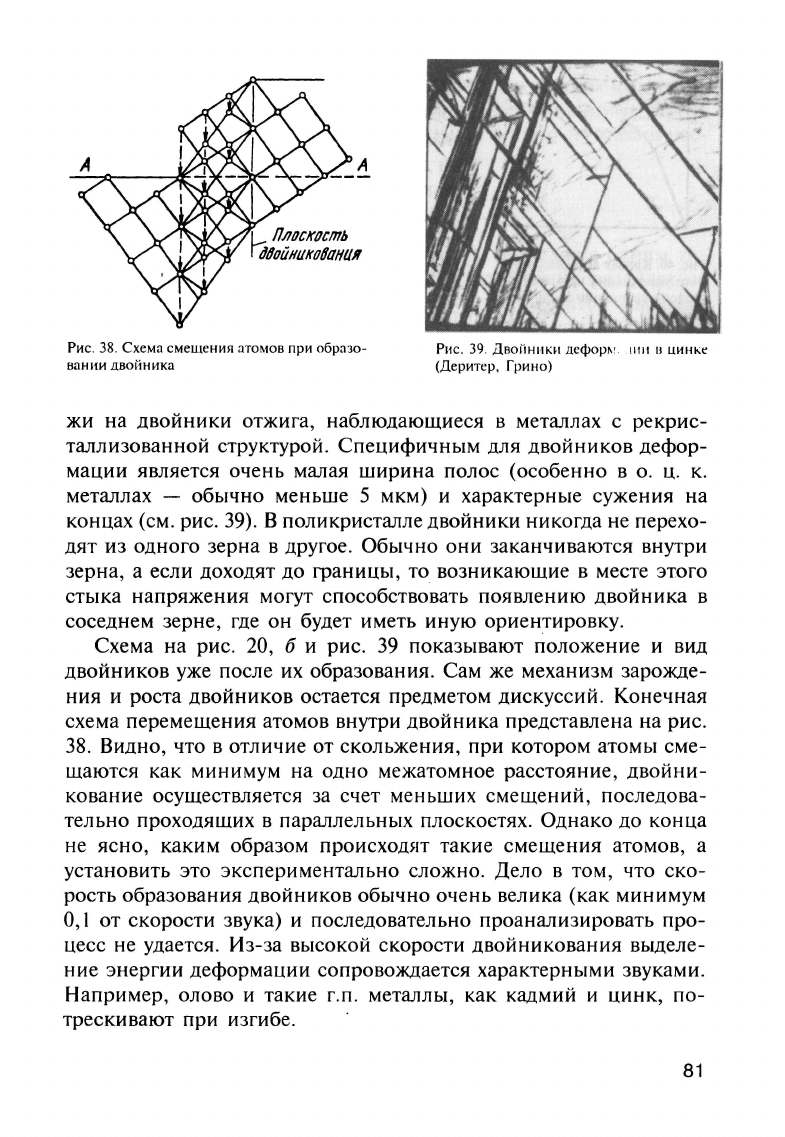
Рис
.
38.
Схема
смешения
атомо
в
при
обра
зо
ваНI1И
двойника
Рис.
39
.
ДRОIIЮIКII
лсф
о
р
~,
l
1111
IJ
uинке
(Деритер.
Грино)
жи
на
двойники
отжига,
наблюдающиеся
в
металлах
с
рекрис
таллизованной
структурой.
Специфичным
для
двойников
дефор
мации
является
очень
малая
ширина
полос
(особенно
в
о.
ц
.
к.
металлах
-
обычно
меньше
5
мкм)
И
характерные
сужения
на
концах
(см.
рис
.
39).
В
поликристалле
двойники
никогда
не перехо
дят
из
одного
зерна
в
другое.
Обычно
они
заканчиваются
внутри
зерна
,
а
если
доходят
до
границы,
то
возникающие
в
месте
этого
стыка
напряжения
могут
способствовать
появлению
двойника
в
соседнем
зерне,
где
он
будет
иметь
иную
ориентировку
.
Схема
на
рис.
20,
б
и
рис.
39
показывают
положение
и
вид
двойников
уже
после
их
образования
.
Сам
же
механизм
зарожде
ния
и
роста
двойников
остается
предметом
дискуссий.
Конечная
схема
перемещения
атомов
внутри
двойника
представлена
на
рис.
38.
Видно,
что
в
отличие
от
скольжения,
при
котором
атомы
сме
щаются
как
минимум
на
одно
межатомное
расстояние,
двойни
кование
осуществляется
за
счет
меньших
смещений,
последова
тельно
проходящих
в
параллельных
плоскостях
.
Однако
до
конца
не
ясно,
каким
образом
происходят
такие
смещения
атомов,
а
установить
это
экспериментально
сложно.
Дело
в
том
,
что
ско
рость
образования
двойников
обычно
очень
велика
(как
минимум
О,
I
от
скорости
звука)
и
последовательно
проанализировать
про
цесс не
удается.
Из-за
высокой
скорости
двойникования
выделе
ние
энергии
деформации
сопровождается
характерными
звуками.
Например,
олово
и
такие
г.п.
металлы,
как
кадмий
и
цинк
,
по
трескивают
при
изгибе.
81
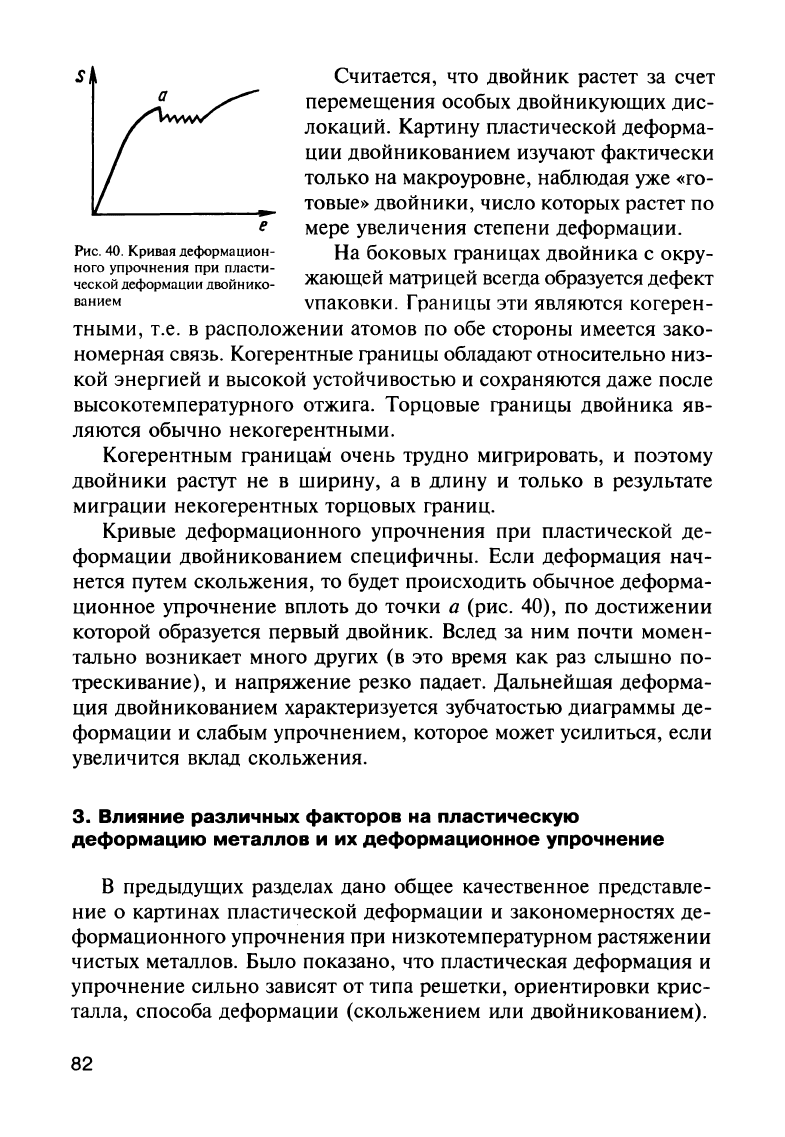
s
Считается,
что
двойник
растет
за
счет
перемещения
особых
двойни
кующих
дис
локаций.
Картину
пластической
деформа
ции
двойникованием
изучают
фактически
только
на
макроуровне,
наблюдая
уже
«го
товые»
двойники,
число
которых
растет
по
е
мере
увеличения
степени
деформации.
Рис.
40.
Кривая
деформацион-
На
боковых
границах
двойника
с
окру-
ного
упрочнения
при
пласти-
б
фе
ческой
деформации
двойнико-
жающей
матрицей
всегда
о
разуется
де
кт
ванием
vпаковки.
Границы
эти
являются
когерен
тными,
Т.е.
в
расположении
атомов
по
обе
стороны
имеется
зако
номерная
связь.
Когерентные
границы
обладают
относительно
низ
кой
энергией
и
высокой
устойчивостью
и
сохраняются
даже
после
высокотемпературного
отжига.
Торцовые
границы двойника
яв
ляются
обычно
некогерентными.
Когерентным
границам
очень
трудно
мигрировать,
и
поэтому
двойники
растут
не
в
ширину,
а
в
длину
и
только
в
результате
миграции
некогерентных
торцовых
границ.
Кривые
деформационного
упрочнения
при
пластической
де
формации
двойникованием
специфичны.
Если
деформация
нач
нется
путем
скольжения,
то будет
происходить
обычное
деформа
ционное
упрочнение
вплоть
до
точки
а
(рис.
40),
по
достижении
которой
образуется
первый
двойник.
Вслед
за
ним
почти
момен
тально
возникает
много
других
(в
это
время
как
раз
слышно
по
трескивание),
и
напряжение
резко
падает.
Дальнейшая
деформа
ция
двойникованием
характеризуется
зубчатостью
диаграммы
де
формации
и
слабым
упрочнением,
которое
может
усилиться,
если
увеличится
вклад
скольжения.
З.
Влияние
различных
факторов
на
пластическую
деформацию
металлов
и их
деформационное
упрочнение
в
предыдущих
разделах
дано
общее
качественное
представле
ние
о
картинах
пластической
деформации
и
закономерностях
де
формационного
упрочнения
при
низкотемпературном
растяжении
чистых
металлов.
БьuJO
показано, что
пластическая
деформация
и
упрочнение
сильно
зависят
от
типа
решетки,
ориентировки
крис
талла,
способа
деформации
(скольжением
или
двойникованием).
82
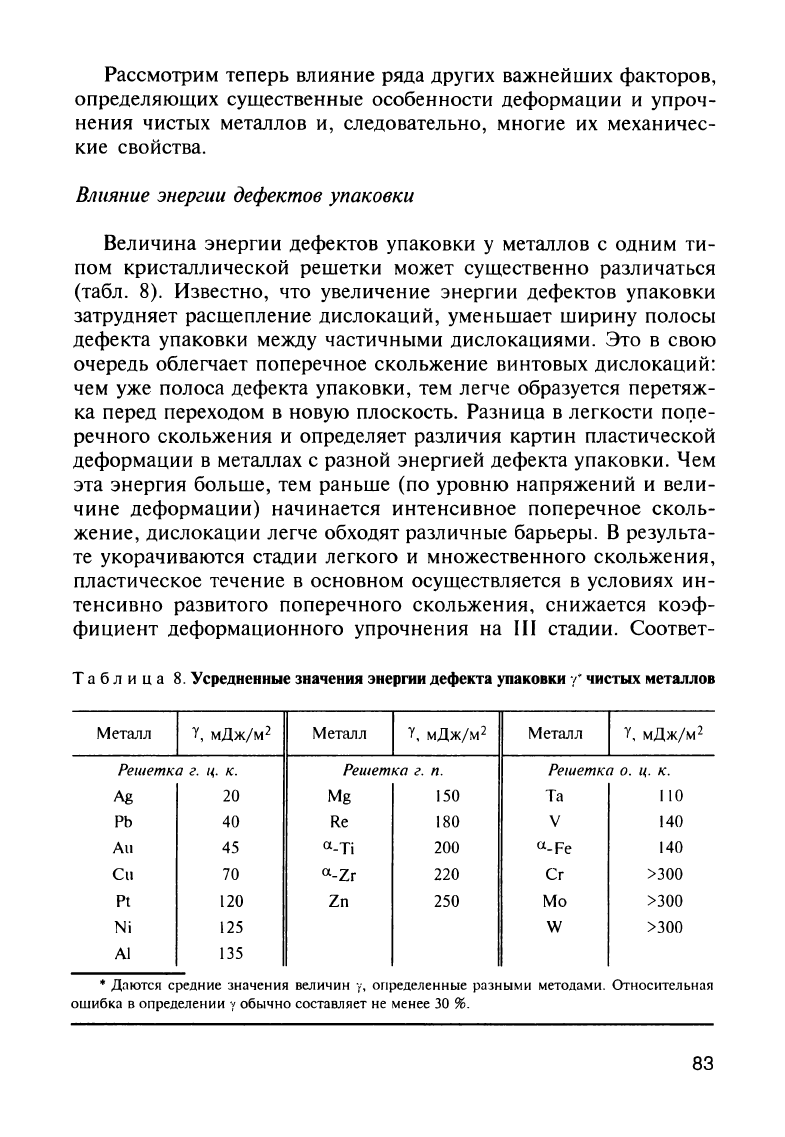
Рассмотрим
теперь
влияние
ряда других
важнейших
факторов,
определяющих
существенные
особенности
деформации
и
упроч
нения
чистых
металлов
и,
следовательно,
многие
их
механичес
кие
свойства.
Влияние
энергии
дефектов
упаковки
Величина
энергии
дефектов упаковки
у
металлов
с
одним
ти
пом
кристаллической
решетки
может
существенно
различаться
(табл.
8).
Известно,
что
увеличение
энергии
дефектов
упаковки
затрудняет
расщепление
дислокаций,
уменьшает
ширину
полосы
дефекта
упаковки
между
частичными
дислокациями.
Это
в
свою
очередь
облегчает
поперечное
скольжение
винтовых
дислокаций:
чем
уже
полоса
дефекта
упаковки,
тем
легче
образуется
перетяж
ка
перед
переходом
в
новую
плоскость.
Разница
в
легкости
ПОIJе
речного
скольжения
и
определяет
различия
картин
пластической
деформации
в
металлах
с
разной
энергией
дефекта
упаковки.
Чем
эта
энергия
больше,
тем
раньше
(по
уровню
напряжений
и
вели
чине
деформации)
начинается
интенсивное
поперечное
сколь
жение,
дислокации
легче
обходят
различные
барьеры.
В
результа
те
укорачиваются
стадии
легкого
и
множественного
скольжения,
пластическое
течение
в
основном
осуществляется
в
условиях
ин
тенсивно
развитого
поперечного
скольжения,
снижается
коэф
фициент
деформационного
упрочнения
на
111
стадии.
Соответ-
Т
а
б л
и
ц
а
8.
Усредненные
значенНJI
энерrнн
дефекта
упаковки
"('
чнстых
металлов
Металл
У,
мДж/м
2
Металл
У,
мДж/м
2
Металл
У,
мДж/м
2
PelllemKa
г.
ц.
К.
Решетка
г.
n.
PelllemKa
о. ц.
К.
Ag
20
Mg
150
Та
110
РЬ
40
Re
180
У
140
Ан
45
а_
Ti
200
Cl-Fe
140
Сн
70
Cl_Z
r
220
Сг
>300
Pt
120 Zn 250
Мо
>300
Ni
125
W
>300
AI
135
•
Даются
средние
значения
величин
у,
определенные
разными
методами.
Относительная
ошибка
в
определении
у
обычно
составляет
не
менее
30
%.
83
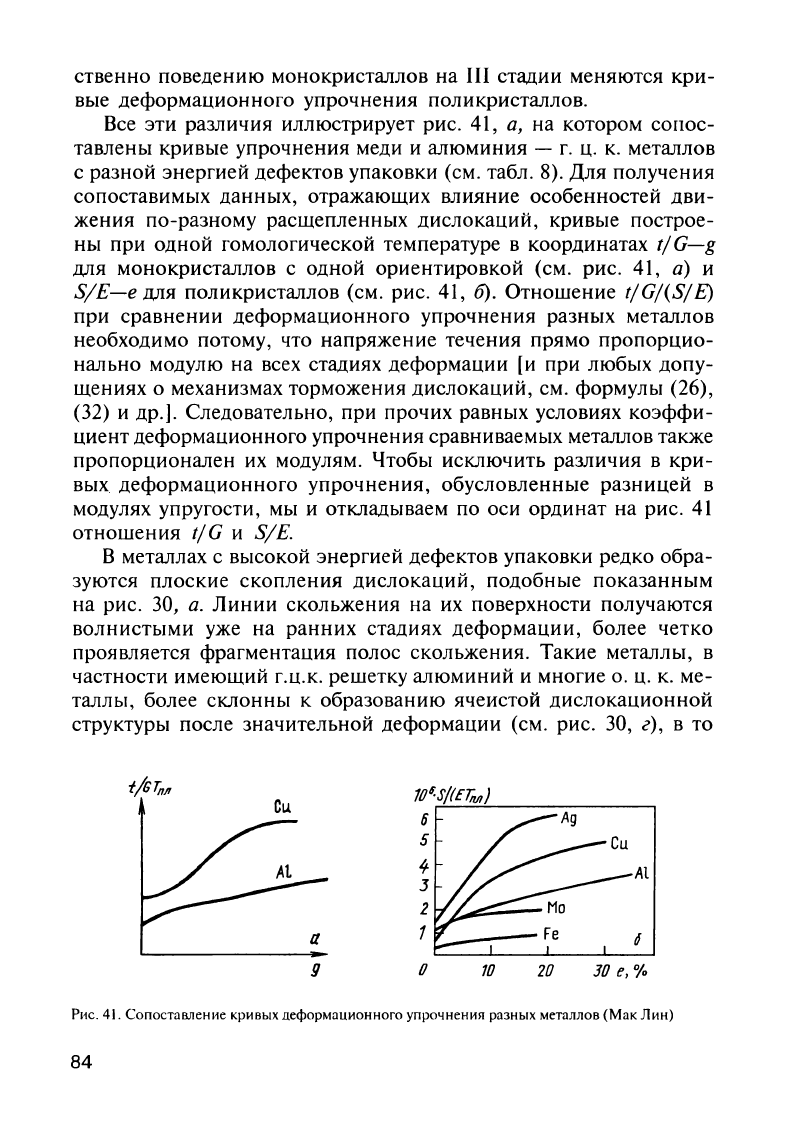
ственно
поведению
монокристаллов
на
111
стадии
меняются
кри
вые
деформационного
упрочнения
поликристаллов.
Все эти
различия
иллюстрирует
рис.
41,
о,
на
котором
сопос
тавлены
кривые
упрочнения
меди
и
алюминия
-
г.
ц.
к.
металлов
с
разной
энергией
дефектов
упаковки
(см.
табл.
8).
Для
получения
сопоставимых
данных,
отражающих
влияние
особенностей
дви
жения
по-разному
расщепленных
дислокаций,
кривые
построе
ны
при
одной
гомологической
температуре
в
координатах
t/G-g
для
монокристаллов
с
одной
ориентировкой
(см.
рис.
41,
о)
и
SjE-е
для
поликристаллов
(см.
рис.
41, 6).
Отношение
t/G/(S/
Е)
при
сравнении
деформационного
упрочнения
разных
металлов
необходимо
потому,
что
напряжение
течения
прямо
пропорцио
нально
модулю
на
всех
стадиях
деформации
[и
при
любых
допу
щениях
о
механизмах
торможения
дислокаций,
см.
формулы
(26),
(32)
и
др.].
Следовательно,
при
прочих
равных
условиях
коэффи
циент
деформационного
упрочнения
сравниваемых
металлов
также
пропорционален
их
модулям.
Чтобы
исключить
различия
в
кри
вых.
деформационного
упрочнения,
обусловленные
разницей
в
модулях
упругости,
мы
и откладываем
по
оси
ординат
на
рис.
41
отношения
t/G
и
SjE.
В
металлах
с
высокой
энергией
дефектов
упаковки
редко
обра
зуются
плоские
скопления
дислокаций,
подобные
показанным
на
рис.
30,
о.
Линии
скольжения
на
их
поверхности
получаются
волнистыми
уже
на
ранних
стадиях
деформации,
более
четко
проявляется
фрагментация
полос
скольжения.
Такие
металлы,
в
частности
имеющий
г.ц.к.
решетку
алюминий
и
многие
о.
ц.
к.
ме
таллы,
более
склонны
к
образованию
ячеистой
дислокационной
структуры
после
значительной
деформации
(см.
рис.
30,
г),
в
то
fjGт"л
10I.S/fЕlЛл)
Сц
6
5
4
J
А!
2
а
1
I
g
О
10
20
зо
е,
су.
Рис.
41.
СопостаW1ение
кривых
деформационного
упрочнения
разных
металлов
(Мак
Лин)
84
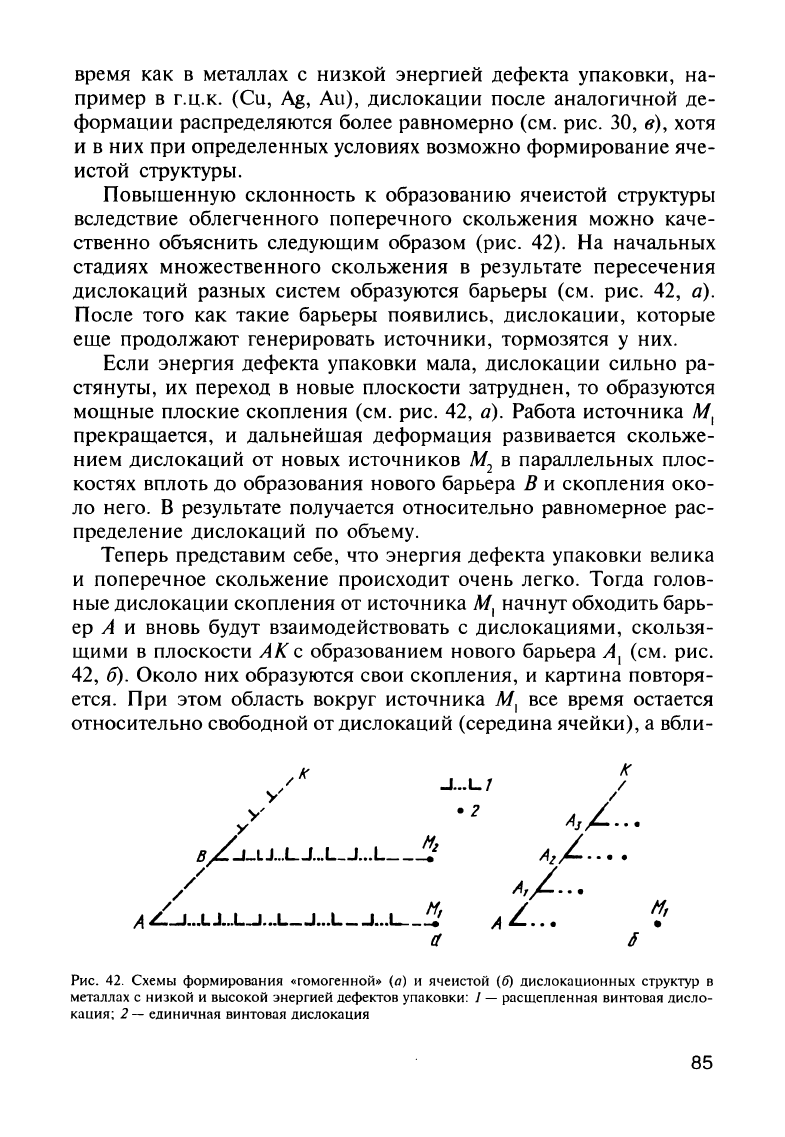
время
как
в
металлах
с
низкой
энергией
дефекта
упаковки,
на
пример
в
Г.ц.К.
(Си,
Лg,
Аи),
дислокации
после
аналогичной
де
формации
распределяются
более
равномерно
(см.
рис.
ЗО,
в),
хотя
и
в
них
при
определенных
условиях
возможно
формирование
яче
истой
структуры.
Повышенную
склонность
к
образованию
ячеистой
структуры
вследствие
облегченного
поперечного
скольжения
можно
каче
ственно
объяснить
следующим
образом
(рис.
42).
На
начальных
стадиях
множественного
скольжения
в
результате
пересечения
дислокаций
разных
систем
образуются
барьеры
(см.
рис.
42,
а).
После
того
как
такие
барьеры
появились,
дислокации,
которые
еще
продолжают
генерировать
источники, тормозятся
у них.
Если
энергия
дефекта
упаковки
мала,
дислокации
сильно
ра
стянуты,
их переход
в
новые
плоскости
затруднен,
то
образуются
мощные
плоские
скопления
(см.
рис.
42,
а).
Работа
источника
М,
прекращается,
и
дальнейшая
деформация
развивается
скольже
нием
дислокаций
от
новых
источников
М
2
В
параллельных
плос
костях
вплоть
до
образования
нового
барьера
В
и
скопления
око
ло
него.
В
результате
получается
относительно
равномерное
рас
пределение
дислокаций
по
объему.
Теперь
представим
себе,
что
энергия
дефекта
упаковки
велика
и
поперечное
скольжение
происходит
очень
легко.
Тогда
голов
ные
дислокации
скопления
от
источника
М,
начнут
обходить
барь
ер
А
и
вновь
будут
взаимодействовать
с
дислокациями,
скользя
щими
в
плоскости
АК
с
образованием
нового
барьера
А,
(см.
рис.
42,
б).
Около
них
образуются
свои
скопления,
и
картина
повторя
ется.
При
этом
область
вокруг
источника
М,
все
время
остается
относительно
свободной
от
дислокаций
(середина
ячейки),
а
вбли-
-2
к
/
/
AJ,L..
..•
Az,L.
..•
•
A,,,L.
..
•
А
L ...
If,
•
Рис.
42.
Схемы
формирования
.гомогенноЙ.
(а)
и
ячеистой
(б)
дислокационных
структур
в
металлах
с
низкой
и
высокой
энергией
дефектов
упаковки:
J -
расщепленная
винтовая
дисло
кация;
2 -
единичная
винтовая
дислокация
85
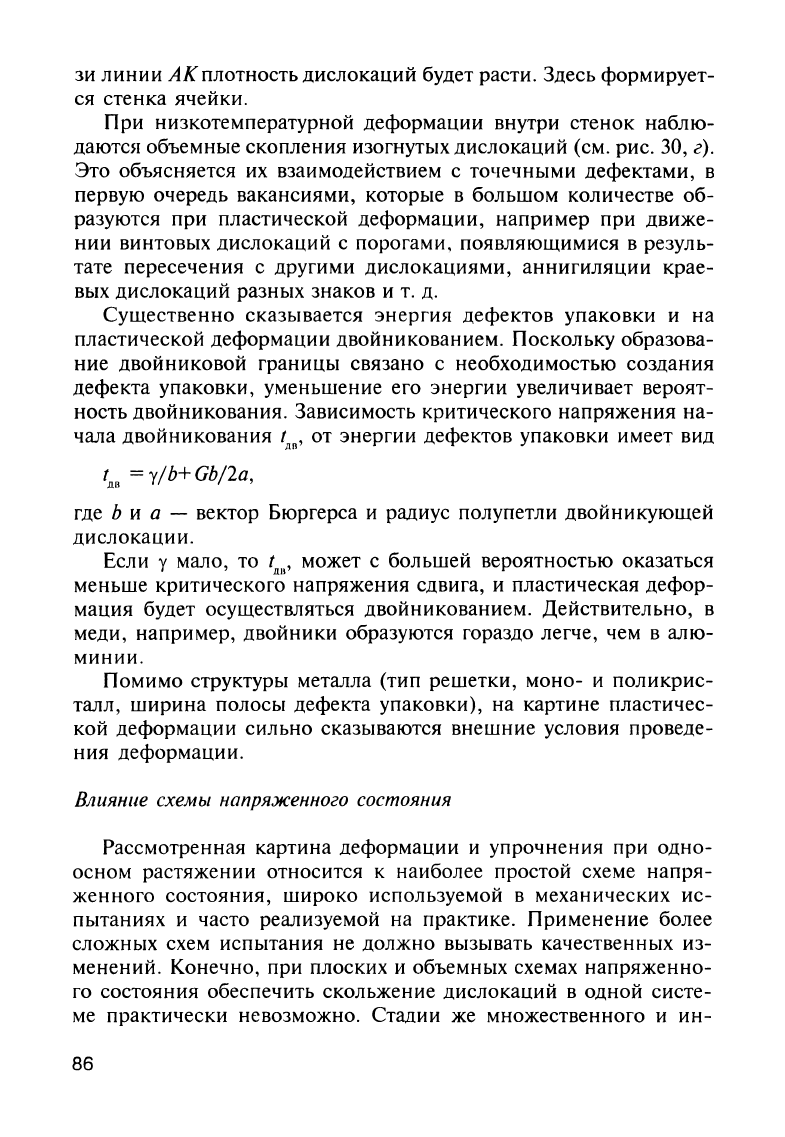
зи
линии
АК
плотность
дислокаций
будет
расти.
Здесь
формирует
ся
стенка
ячейки.
При
низкотемпературной
деформации
внутри стенок
наблю
даются
объемные
скопления
изогнутых
дислокаций
(см.
рис.
ЗО,
г).
Это
объясняется
их
взаимодействием
с
точечными
дефектами,
в
первую
очередь
вакансиями,
которые
в
большом
количестве
об
разуются
при
пластической
деформации,
например
при
движе
нии
винтовых
дислокаций
спорогами,
появляющимися
в
резуль
тате
пересечения
с
другими
дислокациями,
аннигиляции
крае
вых
дислокаций
разных
знаков и
т.
д.
Существенно
сказывается
энергия
дефектов
упаковки
и
на
пластической
деформации
двойникованием.
Поскольку
образова
ние
двойниковой
границы
связано
с
необходимостью
создания
дефекта
упаковки,
уменьшение
его
энергии
увеличивает
вероят
ность
двойникования.
Зависимость
критического
напряжения
на
чала
двойникования
{ДВ'
от
энергии
дефектов
упаковки
имеет
вид
{ДВ
= y/b+Gb/2a,
где Ь
и а
-
вектор
Бюргерса
и
радиус
полупетли
двойни
кующей
дислокации.
Если
у
мало, то
{ДО'
может
с
большей
вероятностью
оказаться
меньше
критического
напряжения
сдвига,
и
пластическая
дефор
мация
будет
осуществляться
двойникованием.
Действительно,
в
меди,
например,
двойники
образуются
гораздо
легче,
чем
в
алю
минии.
Помимо
структуры
металла
(тип
решетки,
моно-
и
поликрис
талл,
ширина
полосы
дефекта
упаковки),
на
картине
пластичес
кой
деформации
сильно
сказываются
внешние
условия
проведе
ния
деформации.
Влияние
схемы
напряженного
состояния
Рассмотренная
картина
деформации
и
упрочнения
при
одно
осном
растяжении
относится
к
наиболее
простой
схеме
напря
женного
состояния,
широко
используемой
в
механических
ис
пытаниях
и
часто
реализуемой
на
практике.
Применение
более
сложных
схем
испытания
не
должно
вызывать
качественных
из
менений.
Конечно,
при
плоских
и
объемных
схемах
напряженно
го
состояния
обеспечить
скольжение
дислокаций
в
одной
систе
ме
практически
невозможно.
Стадии
же
множественного
и
ин-
86
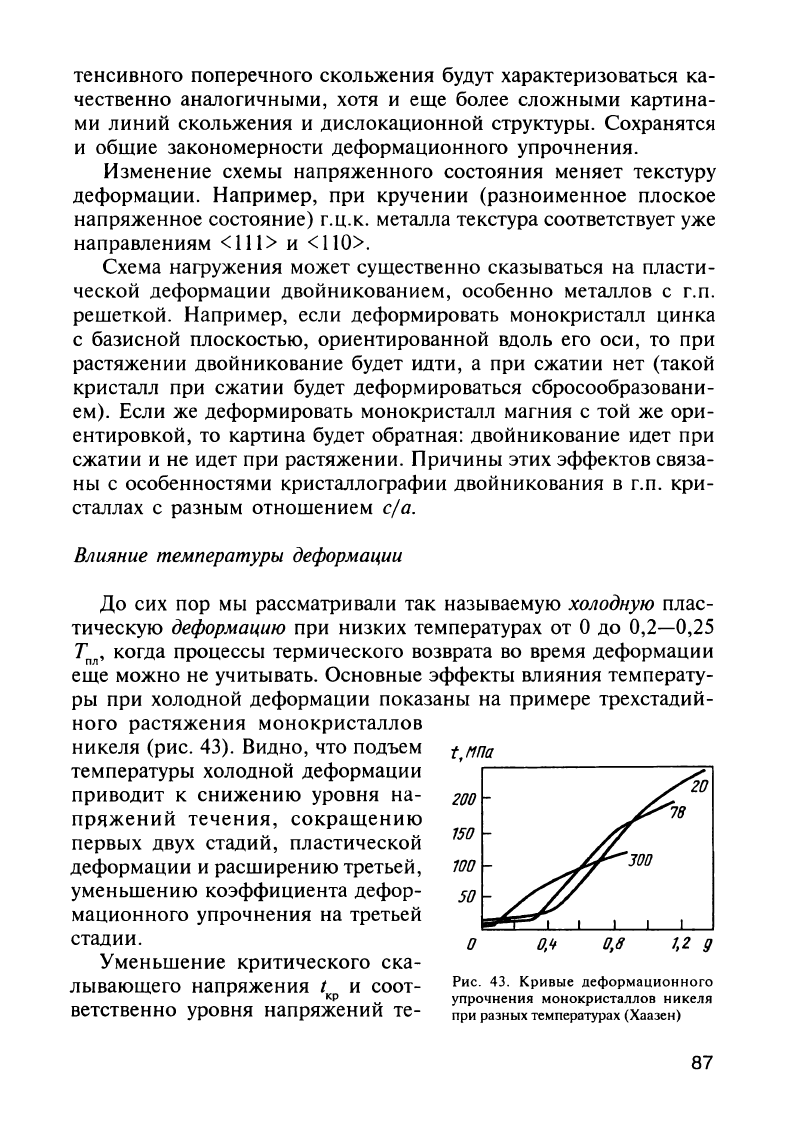
тенсивного
поперечного
скольжения
будут
характеризоваться
ка
чественно
аналогичными,
хотя
и
еще
более
сложными
картина
ми
линий
скольжения
и
дислокационной
структуры.
Сохранятся
и
общие
закономерности
деформационного
упрочнения.
Изменение
схемы
напряженного
состояния
меняет
текстуру
деформации.
Например,
при
кручении
(разноименное
плоское
напряженное
состояние)
г.ц.к.
металла
текстура
соответствует
уже
направлениям
<111>
и
<110>.
Схема
нагружения
может
существенно
сказываться
на
пласти
ческой
деформации
двойникованием,
особенно
металлов
с
г.п.
решеткой.
Например,
если
деформировать
монокристалл
цинка
с
базисной
плоскостью,
ориентированной
вдоль
его оси,
то
при
растяжении
двойникование
будет
идти,
а
при
сжатии
нет
(такой
кристалл
при
сжатии
будет
деформироваться
сбросообразовани
ем).
Если
же
деформировать
монокристалл
магния
с
той
же
ори
ентировкой,
то
картина
будет
обратная:
двойникование
идет
при
сжатии
и
не
идет
при
растяжении.
Причины
этих
эффектов
связа
ны
с
особенностями
кристаллографии
двойникования
в
г.п.
кри
сталлах
с
разным
отношением
с/а.
Влияние
температуры
деформации
До
сих
пор
мы
рассматривали
так
называемую
холодную
плас
тическую
деформацию
при
низких
температурах
от
О
до
0,2-0,25
Т
пn
'
когда
процессы
термического
возврата
во
время
деформации
еще
можно
не
учитывать.
Основные
эффекты
влияния
температу
ры
при
холодной
деформации
показаны
на
при
мере
трехстадий
ного
растяжения
монокристаллов
никеля
(рис.
43).
Видно,
что
подъем
температуры
холодной
деформации
приводит
к
снижению
уровня
на
пряжений
течения,
сокращению
первых
двух
стадий,
пластической
деформации
и
расширению
третьей,
уменьшению
коэффициента
дефор
мационного
упрочнения
на
третьей
стадии.
Уменьшение
критического
ска
лывающего
напряжения
t
KP
и
соот
ветственно
уровня
напряжений
те-
200
750
100
.50
о
0,8
1,2
g
Рис.
43.
Кривые
деформационного
упрочнения
монокристаллов
никеля
при
разных
температурах
(Хаазен)
87
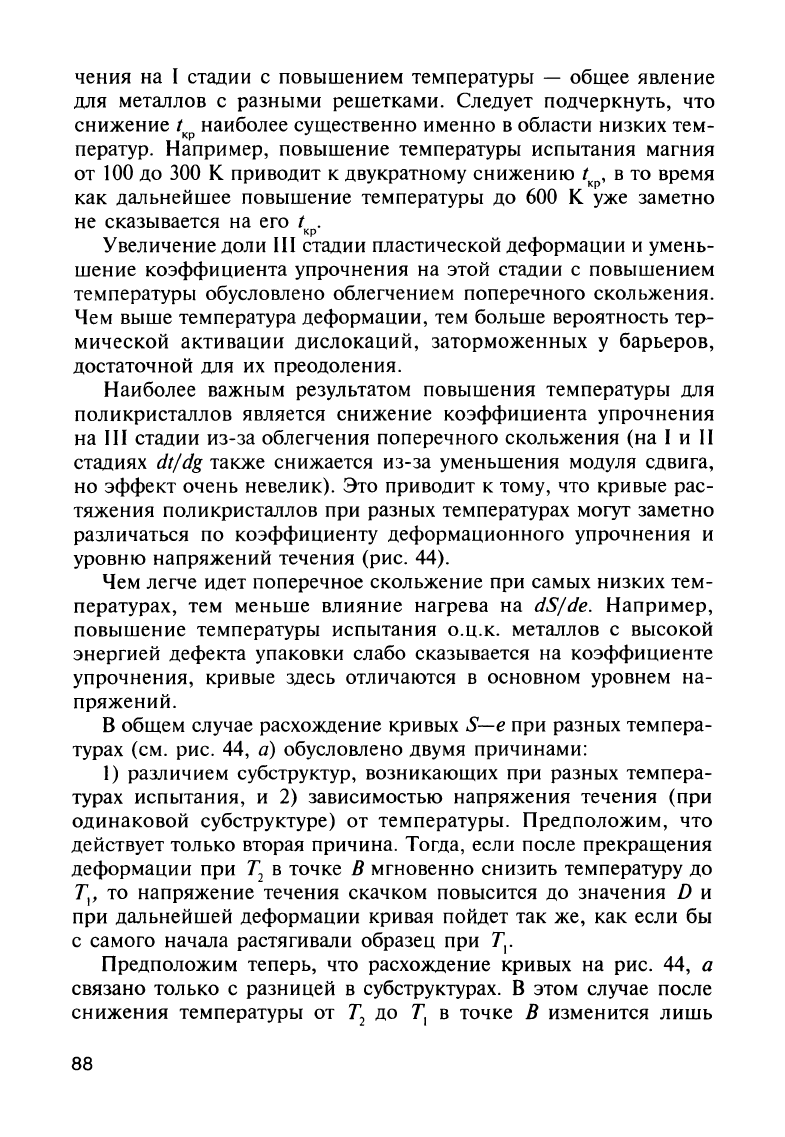
чения
на
1
стадии
с
повышением
температуры
-
общее
явление
для
металлов
с
разными
решетками.
Следует
подчеркнуть,
что
снижение
t
наиболее
существенно
именно
в
области
низких
тем-
кр
ператур.
Например,
повышение
температуры
испытания
магния
от
100
до
300
К
приводит
К
двукратному
снижению
t
KP
'
в
то
время
как
дальнейшее
повышение
температуры до
600
К
уже
заметно
не
сказывается
на
его
t .
кр
Увеличение
доли
111
стадии
пластической
деформации
и
умень-
шение
коэффициента
упрочнения
на
этой
стадии
с
повышением
температуры
обусловлено
облегчением
поперечного
скольжения.
Чем
выше
температура
деформации,
тем
больше
вероятность
тер
мической
активации
дислокаций,
заторможенных
у
барьеров,
достаточной
для
их
преодоления.
Наиболее
важным
результатом
повышения
температуры
для
поликристаллов
является
снижение
коэффиuиента
упрочнения
на
111
стадии
из-за
облегчения
поперечного
скольжения
(на
1
и
11
стадиях
dt/
dg
также
снижается
из-за
уменьшения
модуля
сдвига,
но
эффект
очень
невелик).
Это
приводит
к
тому,
что
кривые
рас
тяжения
поликристаллов
при
разных
температурах
могут
заметно
различаться
по
коэффициенту
деформационного
упрочнения
и
уровню
напряжений
течения
(рис.
44).
Чем
легче
идет
поперечное
скольжение
при
самых
низких
тем
пературах,
тем
меньше
влияние
нагрева
на
dS/
de.
Например,
повышение
температуры
испытания
о.ц.к.
металлов
с
высокой
энергией
дефекта
упаковки
слабо
сказывается
на
коэффициенте
упрочнения,
кривые
здесь
отличаются
в
основном
уровнем
на
пряжений.
В
общем
случае
расхождение
кривых
S-e
при
разных
темпера
турах
(см.
рис.
44,
а)
обусловлено
двумя
причинами:
1)
различием
субструктур,
возникаюших
при разных
темпера
турах
испытания,
и
2)
зависимостью
напряжения
течения
(при
одинаковой
субструктуре)
от
температуры.
Предположим,
что
действует
только
вторая
причина.
Тогда,
если
после
прекращения
деформации
при
Т
2
в
точке
В
мгновенно
снизить
температуру
до
Тр
то
напряжение
течения
скачком
повысится
до значения
D
и
при
дальнейшей
деформации
кривая
пойдет
так же,
как
если
бы
с
самого
начала
растягивали
образец
при
Т,.
Предположим
теперь,
что
расхождение
кривых
на
рис.
44,
а
связано
только
с
разницей
в
субструктурах.
В
этом
случае
после
снижения
температуры
от
Т
2
дО
Т,
В
точке
В
изменится
лишь
88
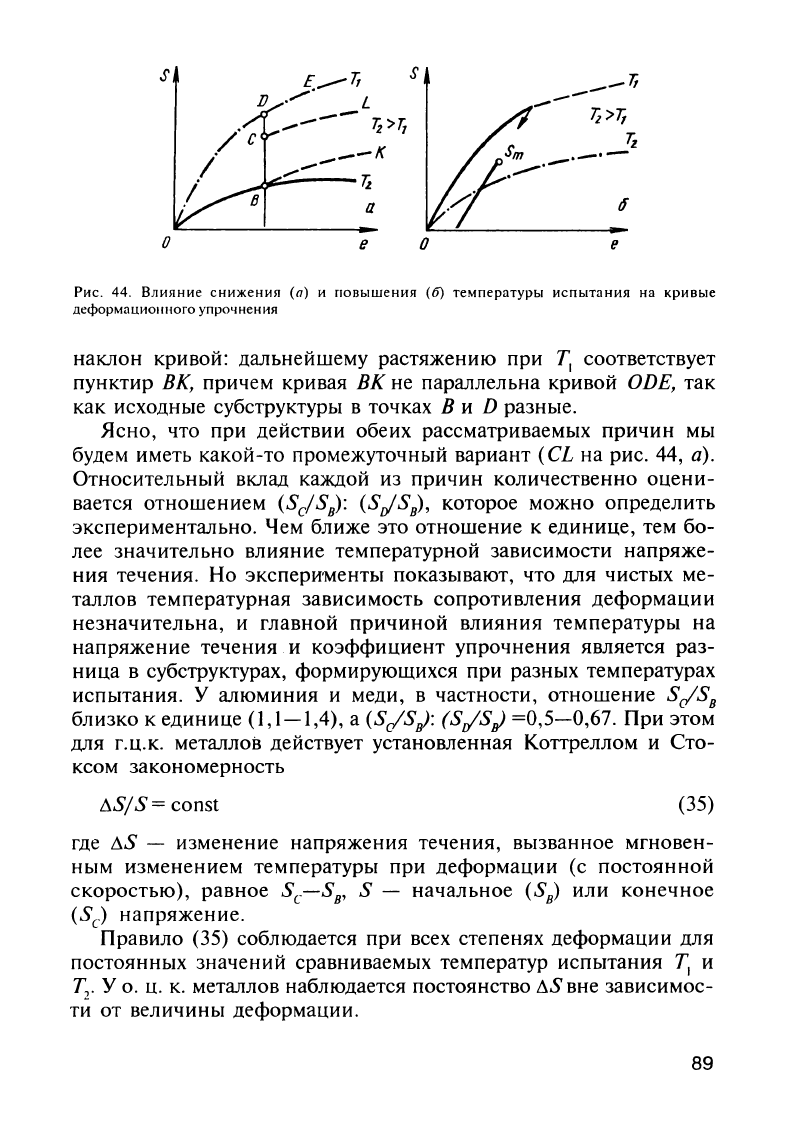
s
о
Е
__
т,
./0
L
--
--
Тz>Т;
_-К
--
-
7l
а
е
s
_7;
--
--
о
е
Рис.
44.
Влияние
снижения
(о)
и
повышения
(6)
температуры
испытания
на
кривые
деформаUИОIIНОГО
упрочнения
наклон
кривой:
дальнейшему
растяжению
при
~
соответствует
пунктир
ВК,
причем
кривая
ВК
не
параллельна
кривой
опЕ,
так
как
исходные
субструктуры
в
точках
В
и
D
разные.
Ясно,
что
при
действии
обеих
рассматриваемых
причин
мы
будем иметь
какой-то
промежуточный
вариант
(CL
на
рис.
44,
а).
Относительный
вклад
каждой
из
причин
количественно
оцени
вается
отношением
(SCjSB):
(Sr/SB)'
которое
можно
определить
экспериментально.
Чем
ближе
это
отношение
к
единице,
тем
бо
лее
значительно
влияние
температурной
зависимости
напряже
ния
течения.
Но
эксперименты
показывают,
что
для
чистых
ме
таллов
температурная
зависимость
сопротивления
деформации
незначительна,
и
главной
причиной
влияния
температуры
на
напряжение
течения
и
коэффициент
упрочнения
является
раз
ница
в
субструктурах,
формирующихся
при разных
температурах
испытания.
У
алюминия
и
меди,
в
частности,
отношение
S/SB
близко
к
единице
(1,1-1,4),
а
(S/S):
(SifS)
=0,5-0,67.
При
этом
для
г.ц.к.
металлов
действует
установленная
Коттреллом
и
Сто
ксом
закономерность
t-.SjS=
const
(35)
где
t-.S
-
изменение
напряжения
течения,
вызванное
мгновен
ным
изменением
температуры
при
деформации
(с
постоянной
скоростью),
равное
SC-SB' S -
начальное
(SB)
или
конечное
(Sc)
напряжение.
Правило
(35)
соблюдается
при
всех
степенях
деформации
для
постоянных
значений
сравниваемых
температур
испытания
~
и
то.
у
о. ц.
к.
металлов
наблюдается
постоянство
t-.S
вне
зависимос
ти от
величины
деформации.
89