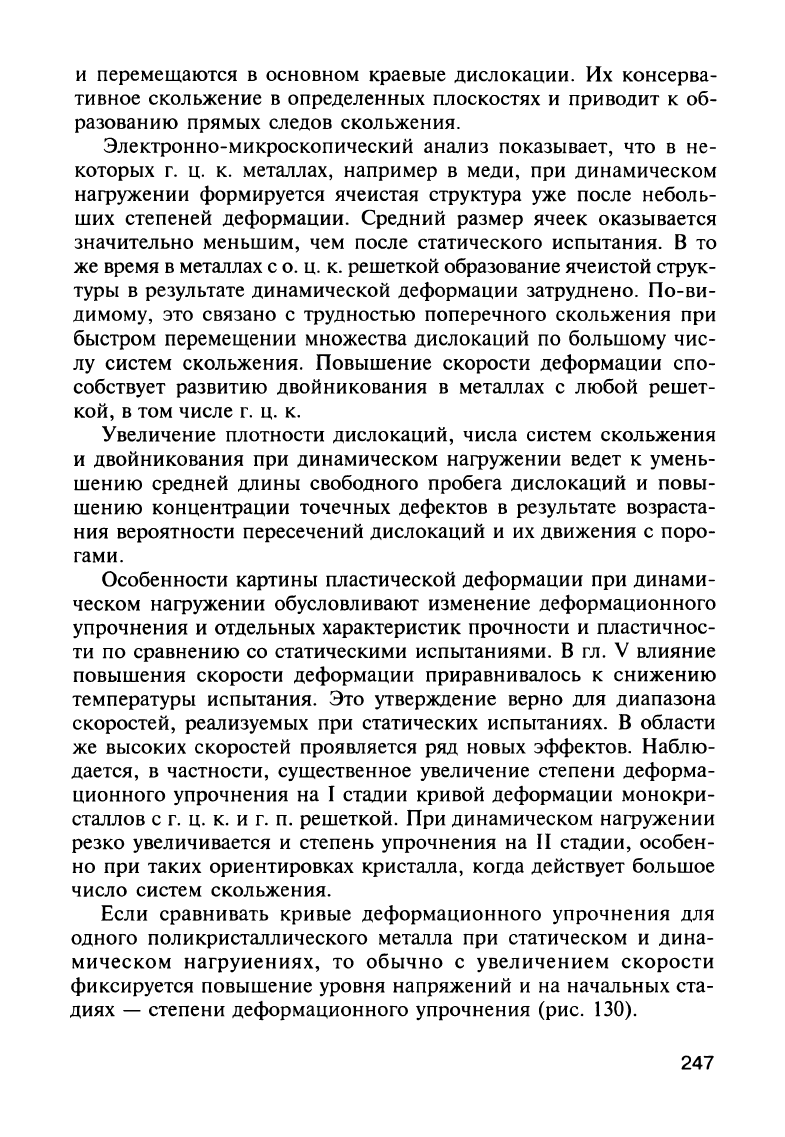
и
перемещаются
в
основном
краевые
дислокации.
Их
консерва
тивное
скольжение
в
определенных
плоскостях
и
при
водит
К
об
разованию
прямых
следов
скольжения.
Электронно-микроскопический
анализ
показывает,
что
в
не
которых
г.
ц.
к.
металлах,
например
в
меди,
при
динамическом
нагружении
формируется
ячеистая
структура
уже
после
неболь
ших
степеней
деформации.
Средний
размер
ячеек
оказывается
значительно
меньшим,
чем
после
статического
испытания.
В
то
же
время
в
металлах
с
о.
ц.
к.
решеткой
образование
ячеистой
струк
туры
в
результате
динамической
деформации
затруднено.
По-ви
димому,
это
связано
с
трудностью
поперечного
скольжения
при
быстром
перемещении
множества
дислокаций
по
большому
чис
лу
систем
скольжения.
Повышение
скорости
деформации
спо
собствует
развитию
двойникования
в
металлах
с
любой
решет
кой,
в
том
числе
г.
ц.
к.
Увеличение
плотности
дислокаций,
числа
систем
скольжения
и
двойникования
при динамическом
нагружении
ведет
к
умень
шению
средней
длины
свободного
пробега
дислокаций
и
повы
шению
концентрации
точечных
дефектов
в
результате
возраста
ния
вероятности
пересечений
дислокаций
и
их
движения
с
поро
гами.
Особенности
картины
пластической
деформации
при
динами
ческом
нагружении
обусловливают
изменение
деформационного
упрочнения
и
отдельных
характеристик
прочности
и
пластичнос
ти
по
сравнению
со
статическими
испытаниями.
В
гл.
V
влияние
повышения
скорости
деформации
приравнивалось
к
снижению
температуры
испытания.
Это
утверждение
верно
для
диапазона
скоростей,
реализуемых
при
статических
испытаниях.
В
области
же
высоких
скоростей
проявляется
ряд
новых
эффектов.
Наблю
дается,
в
частности,
существенное
увеличение
степени
деформа
ционного
упрочнения
на
1
стадии
кривой
деформации
монокри
сталлов
с
г.
ц.
к.
И
г.
п.
решеткой.
При
динамическом
нагружении
резко
увеличивается
и
степень
упрочнения
на
11
стадии,
особен
но
при
таких
ориентировках
кристалла,
когда
действует
большое
число
систем
скольжения.
Если
сравнивать
кривые
деформационного
упрочнения
для
одного
поликристаллического
металла
при
статическом
и
дина
мическом
нагруиениях,
то
обычно
с
увеличением
скорости
фиксируется
повышение
уровня
напряжений
и
на
начальных
ста
диях
-
степени
деформационного
упрочнения
(рис.
130).
247