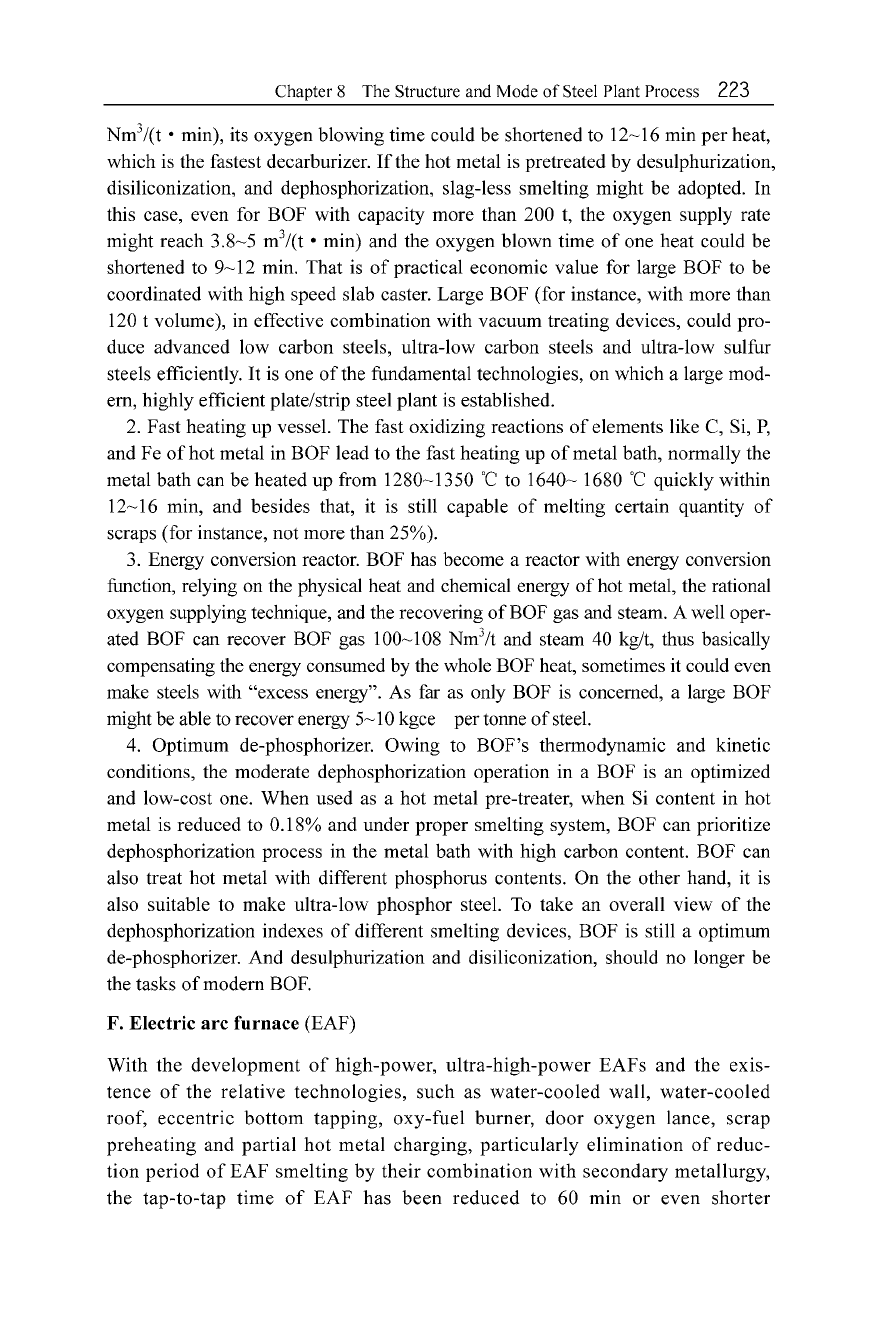
Chapter 8 The Structure and Mode
of
Steel Plant Process
223
Nm
3
/(t • min), its oxygen blowing time could be shortened to
12
~
16 min per heat,
which is the fastest decarburizer.
If
the hot metal is pretreated by desulphurization,
disiliconization, and dephosphorization, slag-less smelting might be adopted. In
this case, even for BOF with capacity more than 200 t, the oxygen supply rate
might reach
3.8
~5
m
3
/(t • min) and the oxygen blown time
of
one heat could be
shortened to
9
~
12 min. That is
of
practical economic value for large BOF to be
coordinated with high speed slab caster. Large BOF (for instance, with more than
120 t volume), in effective combination with vacuum treating devices, could pro-
duce advanced low carbon steels, ultra-low carbon steels and ultra-low sulfur
steels efficiently.
It
is one
of
the fundamental technologies, on which a large mod-
em, highly efficient plate/strip steel plant is established.
2. Fast heating up vessel. The fast oxidizing reactions
of
elements like C, Si, P,
and Fe
of
hot metal in BOF lead to the fast heating up
of
metal bath, normally the
metal bath can be heated up from
1280
~
1350 'C to
1640
~
1680 'C quickly within
12
~
16 min, and besides that, it is still capable
of
melting certain quantity
of
scraps (for instance, not more than 25%).
3. Energy conversion reactor. BOF has become a reactor with energy conversion
function, relying on the physical heat and chemical energy
of
hot metal, the rational
oxygen supplying technique, and the recovering
of
BOF gas and steam. A well oper-
ated BOF can recover BOF gas
100
~1O8
Nm
3
/t and steam 40 kg/t, thus basically
compensating the energy consumed by the whole BOF heat, sometimes it could even
make steels with "excess energy". As far as only BOF is concerned, a large BOF
might be able to recover energy
5
~
10 kgce per tonne
of
steel.
4. Optimum de-phosphorizer. Owing to BOF's thermodynamic and kinetic
conditions, the moderate dephosphorization operation in a BOF is an optimized
and low-cost one. When used as a hot metal pre-treater, when Si content in hot
metal is reduced to 0.18% and under proper smelting system, BOF can prioritize
dephosphorization process in the metal bath with high carbon content. BOF can
also treat hot metal with different phosphorus contents. On the other hand, it is
also suitable to make ultra-low phosphor steel. To take an overall view
of
the
dephosphorization indexes
of
different smelting devices, BOF is still a optimum
de-phosphorizer. And desulphurization and disiliconization, should no longer be
the tasks
of
modem BOF.
F. Electric arc furnace (EAF)
With the
development
of
high-power,
ultra-high-power
EAFs and the exis-
tence
of
the relative technologies,
such
as water-cooled wall, water-cooled
roof,
eccentric
bottom tapping, oxy-fuel burner,
door
oxygen
lance, scrap
preheating
and partial
hot
metal charging, particularly elimination
of
reduc-
tion period
of
EAF smelting by
their
combination
with
secondary metallurgy,
the tap-to-tap time
of
EAF has been reduced to 60 min or even
shorter