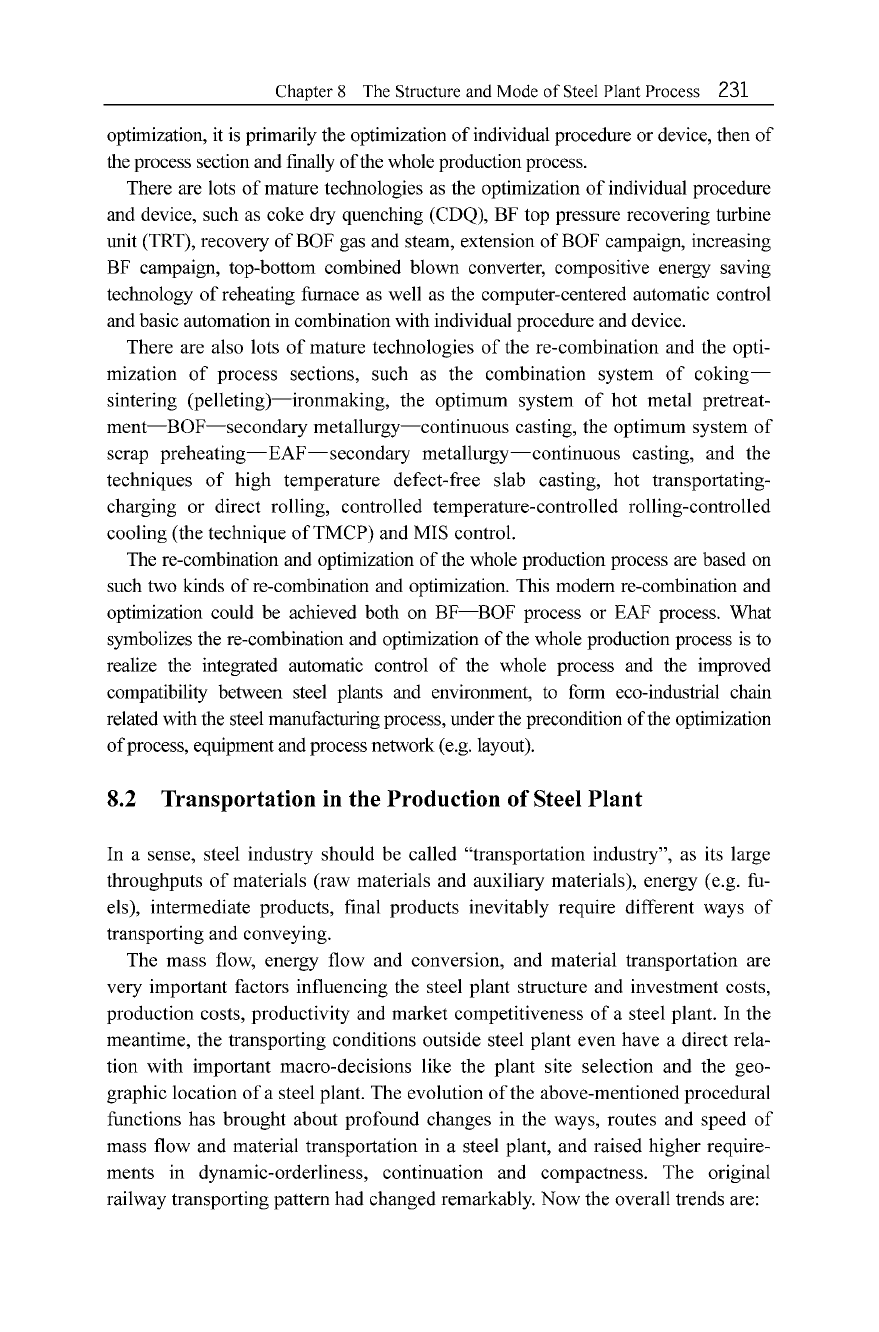
Chapter 8 The Structure and Mode
of
Steel Plant Process
231
optimization,it is primarily the optimization
of
individualprocedure or device,then of
the processsectionand finallyofthe whole productionprocess.
There are lots
of
mature technologies as the optimization
of
individual procedure
and device, such as coke dry quenching (CDQ),
SF
top pressure recovering turbine
unit (TRT), recovery of BOF gas and steam, extension
of
BOF campaign, increasing
BF campaign, top-bottom combined blown converter, compositive energy saving
technology
of
reheating furnace as well as the computer-centered automatic control
and basic automation in combinationwith individualprocedure and device.
There are also lots
of
mature technologies
of
the re-combination and the opti-
mization
of
process sections, such as the combination system
of
coking-
sintering (pelletingj-r-ironmaking, the optimum system
of
hot metal pretreat-
ment
-SOF
-secondary
metallurgy
-continuous
casting, the optimum system
of
scrap preheating
-EAF
-secondary
metallurgy
-continuous
casting, and the
techniques
of
high temperature defect-free slab casting, hot transportating-
charging or direct rolling, controlled temperature-controlled rolling-controlled
cooling (the technique
ofTMCP)
and MIS control.
The re-combination and optimization of the whole production process are based on
such two kinds
of
re-combination and optimization. This modem re-combination and
optimization could be achieved both on
BF-BOF
process or EAF process. What
symbolizes the re-combination and optimization
of
the whole production process is to
realize the integrated automatic control of the whole process and the improved
compatibility between steel plants and environment, to form eco-industrial chain
relatedwith the steel manufacturingprocess, underthe precondition
of
the optimization
of process,equipmentand processnetwork (e.g. layout).
8.2 Transportation in the Production of Steel Plant
In a sense, steel industry should be called "transportation industry", as its large
throughputs
of
materials (raw materials and auxiliary materials), energy (e.g. fu-
els), intermediate products, final products inevitably require different ways
of
transporting and conveying.
The mass flow, energy flow and conversion, and material transportation are
very important factors influencing the steel plant structure and investment costs,
production costs, productivity and market competitiveness
of
a steel plant. In the
meantime, the transporting conditions outside steel plant even have a direct rela-
tion with important macro-decisions like the plant site selection and the geo-
graphic location
of
a steel plant. The evolution
of
the above-mentioned procedural
functions has brought about profound changes in the ways, routes and speed
of
mass flow and material transportation in a steel plant, and raised higher require-
ments in dynamic-orderliness, continuation and compactness. The original
railway transporting pattern had changed remarkably. Now the overall trends are: