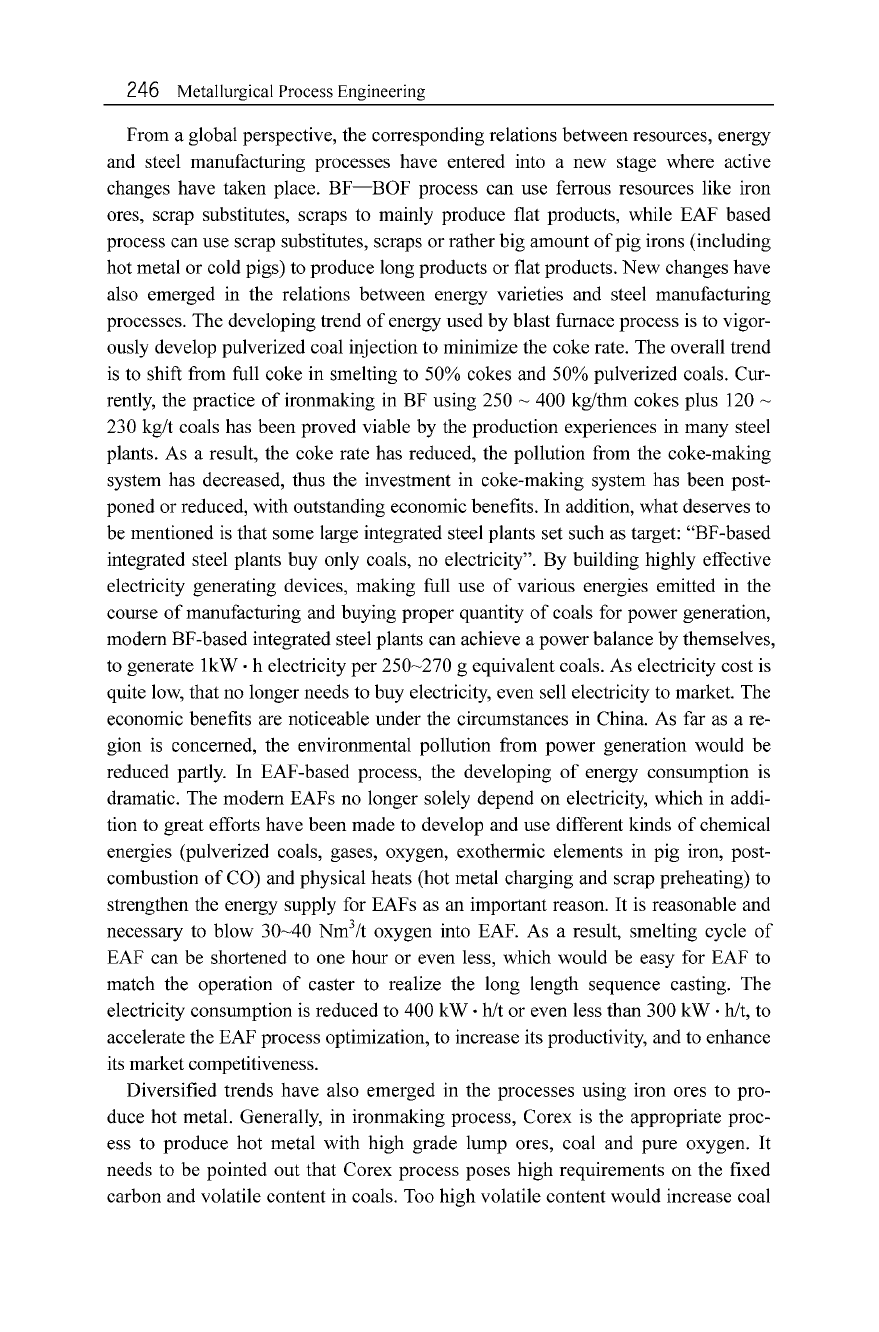
246 Metallurgical Process Engineering
From a global perspective, the corresponding relations between resources, energy
and steel manufacturing processes have entered into a new stage where active
changes have taken place. BF
-BOF
process can use ferrous resources like iron
ores, scrap substitutes, scraps to mainly produce flat products, while EAF based
process can use scrap substitutes, scraps or rather big amount
of
pig irons (including
hot metal or cold pigs) to produce long products or flat products. New changes have
also emerged in the relations between energy varieties and steel manufacturing
processes. The developing trend
of
energy used by blast furnace process is to vigor-
ously develop pulverized coal injection to minimize the coke rate. The overall trend
is to shift from full coke in smelting to 50% cokes and 50% pulverized coals. Cur-
rently, the practice
of
ironmaking in SF using 250
~
400 kg/thm cokes plus 120
~
230 kglt coals has been proved viable by the production experiences in many steel
plants. As a result, the coke rate has reduced, the pollution from the coke-making
system has decreased, thus the investment in coke-making system has been post-
poned or reduced, with outstanding economic benefits. In addition, what deserves to
be mentioned is that some large integrated steel plants set such as target: "SF-based
integrated steel plants buy only coals, no electricity".
By building highly effective
electricity generating devices, making full use
of
various energies emitted in the
course
of
manufacturing and buying proper quantity
of
coals for power generation,
modern SF-based integrated steel plants can achieve a power balance by themselves,
to generate 1kW . h electricity per
250
~270
g equivalent coals. As electricity cost is
quite low, that no longer needs to buy electricity,even sell electricity to market. The
economic benefits are noticeable under the circumstances in China. As far as a re-
gion is concerned, the environmental pollution from power generation would be
reduced partly. In EAF-based process, the developing
of
energy consumption is
dramatic. The modern EAFs no longer solely depend on electricity, which in addi-
tion to great efforts have been made to develop and use different kinds
of
chemical
energies (pulverized coals, gases, oxygen, exothermic elements in pig iron, post-
combustion
of
CO) and physical heats (hot metal charging and scrap preheating) to
strengthen the energy supply for EAFs as an important reason.
It
is reasonable and
necessary to blow
30
~40
Nm
3
It oxygen into EAF. As a result, smelting cycle
of
EAF can be shortened to one hour or even less, which would be easy for EAF to
match the operation
of
caster to realize the long length sequence casting. The
electricity consumption is reduced to 400 kW •
hit or even less than 300 kW . hit, to
accelerate the EAF process optimization, to increase its productivity, and to enhance
its market competitiveness.
Diversified trends have also emerged in the processes using iron ores to pro-
duce hot metal. Generally, in ironmaking process, Corex is the appropriate proc-
ess to produce hot metal with high grade lump ores, coal and pure oxygen.
It
needs to be pointed out that Corex process poses high requirements on the fixed
carbon and volatile content in coals. Too high volatile content would increase coal