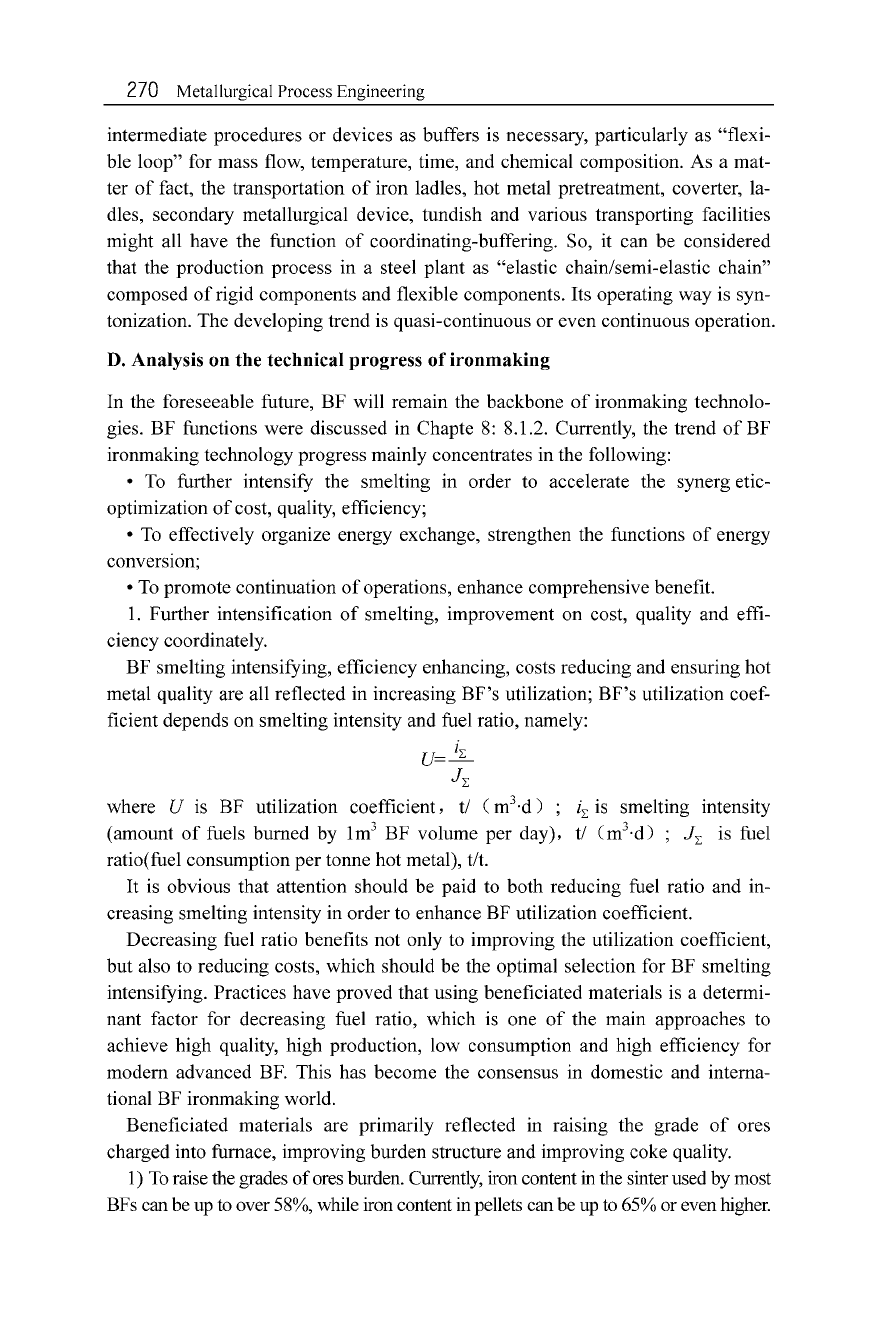
l'L IS smelting intensity
t/ (m
3
'd ) ; J 'L is fuel
270
Metallurgical Process Engineering
intermediate procedures or devices as buffers is necessary, particularly as "flexi-
ble loop" for mass flow, temperature, time, and chemical composition. As a mat-
ter
of
fact, the transportation
of
iron ladles, hot metal pretreatment, coverter, la-
dles, secondary metallurgical device, tundish and various transporting facilities
might all have the function
of
coordinating-buffering. So, it can be considered
that the production process in a steel plant as "elastic chain/semi-elastic chain"
composed
of
rigid components and flexible components. Its operating way is syn-
tonization. The developing trend is quasi-continuous or even continuous operation.
D. Analysis on the technical progress
of
iron
making
In the foreseeable future, BF will remain the backbone
of
ironmaking technolo-
gies. BF functions were discussed in Chapte 8: 8.1.2. Currently, the trend
of
BF
ironmaking technology progress mainly concentrates in the following:
• To further intensify the smelting in order to accelerate the synerg etic-
optimization
of
cost, quality, efficiency;
• To effectively organize energy exchange, strengthen the functions
of
energy
conversion;
• To promote continuation
of
operations, enhance comprehensive benefit.
I. Further intensification
of
smelting, improvement on cost, quality and effi-
ciency coordinately.
BF smelting intensifying, efficiency enhancing, costs reducing and ensuring hot
metal quality are all reflected in increasing
SF's
utilization;
SF's
utilization coef-
ficient depends on smelting intensity and fuel ratio, namely:
U=!:L
J 'L
where U is
SF
utilization coefficient, t/
(m
3'd)
(amount
of
fuels burned by 1m
3
BF volume per day),
ratio(fuel consumption per tonne hot metal), tit.
H is obvious that attention should be paid to both reducing fuel ratio and in-
creasing smelting intensity in order to enhance
SF
utilization coefficient.
Decreasing fuel ratio benefits not only to improving the utilization coefficient,
but also to reducing costs, which should be the optimal selection for BF smelting
intensifying, Practices have proved that using beneficiated materials is a determi-
nant factor for decreasing fuel ratio, which is one
of
the main approaches to
achieve high quality, high production, low consumption and high efficiency for
modern advanced SF. This has become the consensus in domestic and interna-
tional BF ironmaking world.
Beneficiated materials are primarily reflected in raising the grade
of
ores
charged into furnace, improving burden structure and improving coke quality.
I) To raisethe grades
of
ores burden. Currently, iron content inthe sinterused by most
BFs can be up to over 58%, while iron contentin pelletscan be up to 65% or even higher.