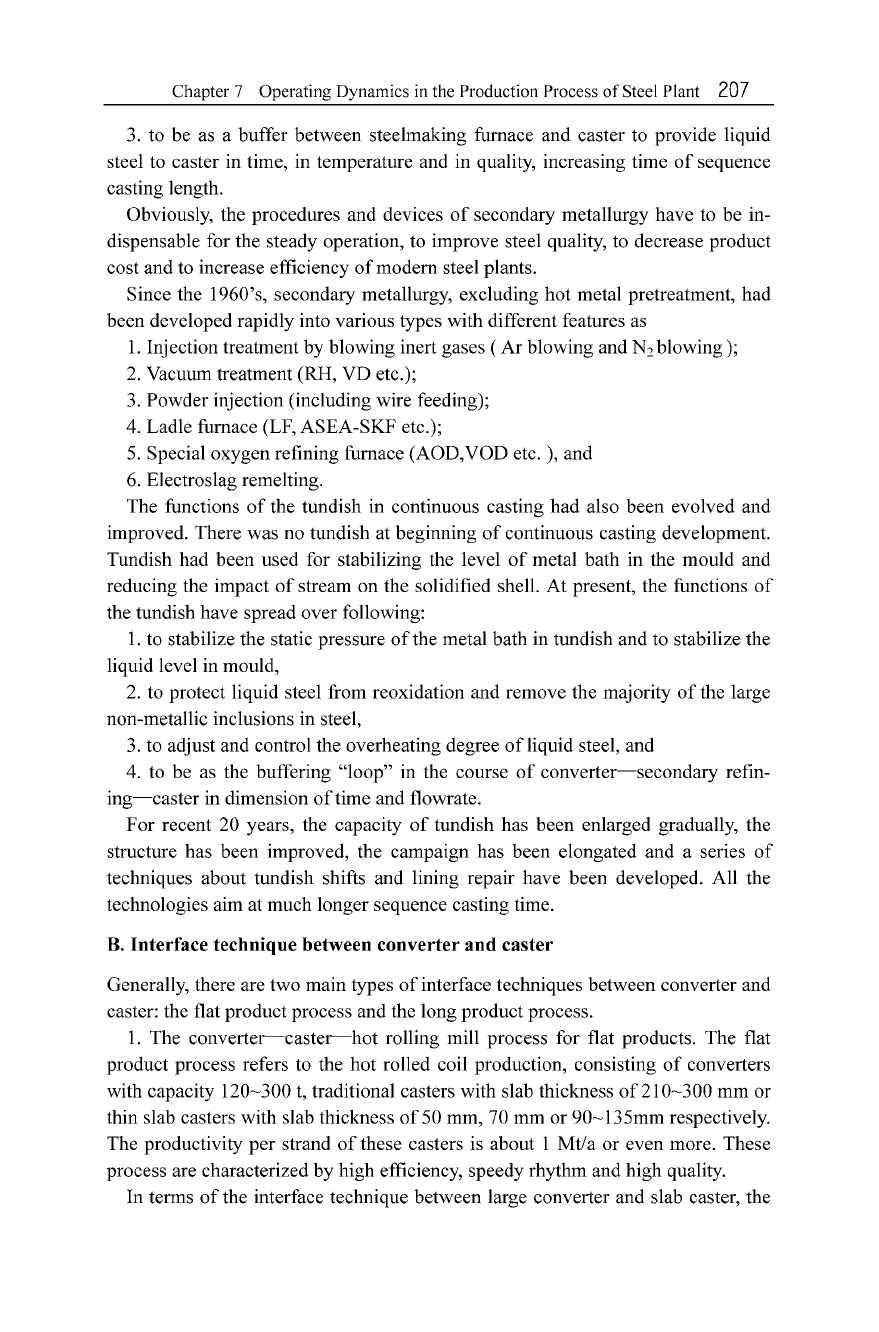
Chapter 7 Operating Dynamics in the Production Process
of
Steel Plant 207
3. to be as a buffer between steelmaking furnace and caster to provide liquid
steel to caster in time, in temperature and in quality, increasing time
of
sequence
casting length.
Obviously, the procedures and devices
of
secondary metallurgy have to be in-
dispensable for the steady operation, to improve steel quality, to decrease product
cost and to increase efficiency
of
modem steel plants.
Since the 1960's, secondary metallurgy, excluding hot metal pretreatment, had
been developed rapidly into various types with different features as
1. Injection treatment by blowing inert gases
(Ar
blowing and N
2
blowing);
2. Vacuum treatment (RH, VD etc.);
3. Powder injection (including wire feeding);
4. Ladle furnace (LF, ASEA-SKF etc.);
5. Special oxygen refining furnace (AOD,VOD etc. ), and
6. Electroslag remelting.
The functions
of
the tundish in continuous casting had also been evolved and
improved. There was no tundish at beginning
of
continuous casting development.
Tundish had been used for stabilizing the level
of
metal bath in the mould and
reducing the impact
of
stream on the solidified shell. At present, the functions
of
the tundish have spread over following:
I. to stabilize the static pressure
of
the metal bath in tundish and to stabilize the
liquid level in mould,
2. to protect liquid steel from reoxidation and remove the majority
of
the large
non-metallic inclusions in steel,
3. to adjust and control the overheating degree
of
liquid steel, and
4. to be as the buffering "loop" in the course
of
converter-secondary refin-
ing
-caster
in dimension
of
time and flowrate.
For recent 20 years, the capacity
of
tundish has been enlarged gradually, the
structure has been improved, the campaign has been elongated and a series
of
techniques about tundish shifts and lining repair have been developed. All the
technologies aim at much longer sequence casting time.
B. Interface technique between converter and caster
Generally, there are two main types
of
interface techniques between converter and
caster: the flat product process and the long product process.
1. The
converter-caster-hot
rolling mill process for flat products. The flat
product process refers to the hot rolled coil production, consisting
of
converters
with capacity 120
-300
t, traditional casters with slab thickness of210
-300
mm or
thin slab casters with slab thickness
of
50 mm, 70 mm or 90
-I35mm
respectively.
The productivity per strand
of
these casters is about 1 Mtla or even more. These
process are characterized by high efficiency, speedy rhythm and high quality.
In terms
of
the interface technique between large converter and slab caster, the