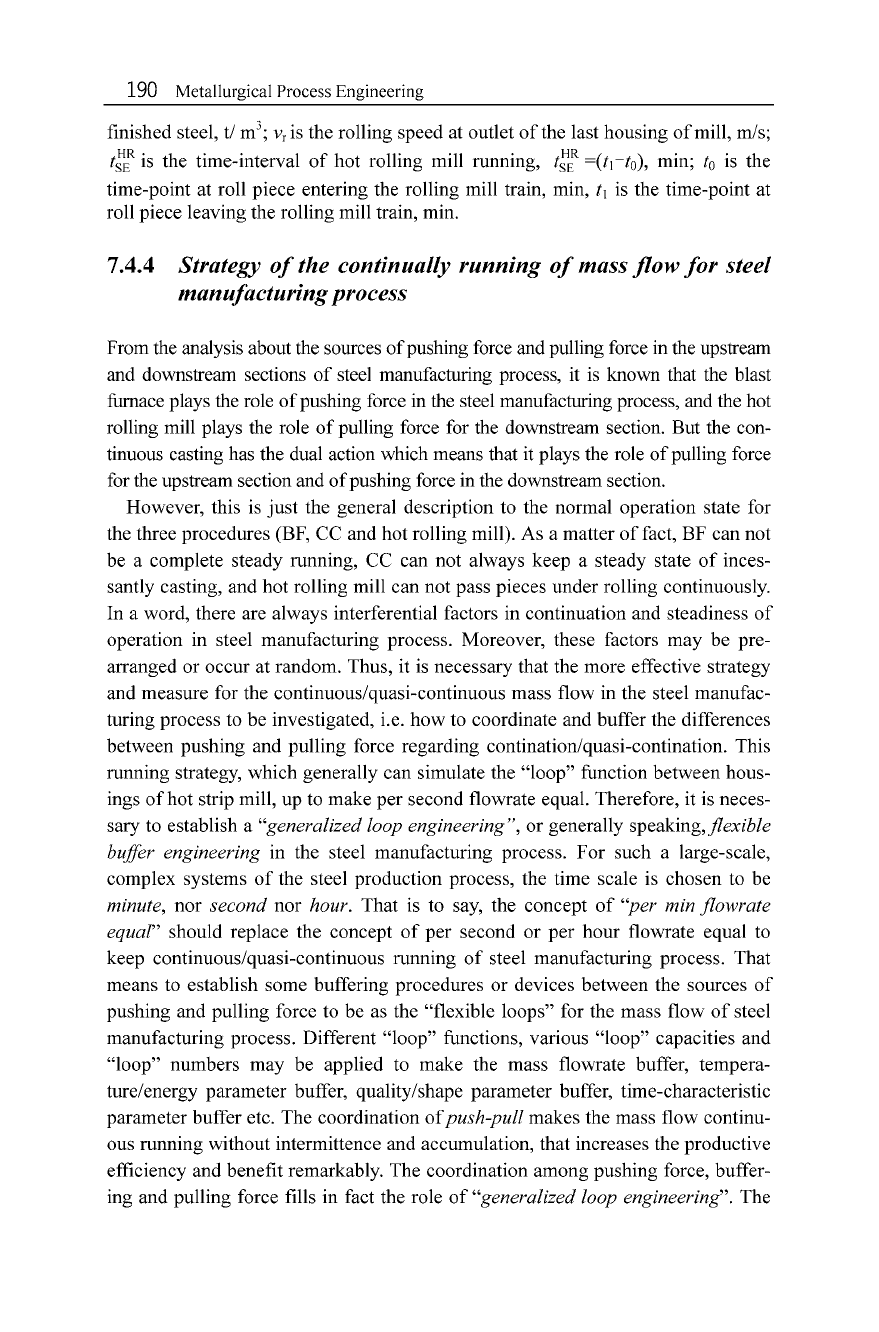
190 Metallurgical Process Engineering
finished steel, t/ rrr'; vris the rolling speed at outlet
of
the last housing of mill, m/s;
t~
ER
is the time-interval
of
hot rolling mill running,
t~
ER
=(t1- tO), min;
to
is the
time-point at roll piece entering the rolling mill train, min,
t1
is the time-point at
roll piece leaving the rolling mill train, min.
7.4.4 Strategy
of
the continually running
of
mass flow
for
steel
manufacturingprocess
Fromthe analysisabout the sources
of
pushing force and pulling force in the upstream
and downstream sections of steel manufacturing process, it is known that the blast
furnaceplays the role
of
pushing force in the steel manufacturingprocess, and the hot
rolling mill plays the role
of
pulling force for the downstream section. But the con-
tinuous casting has the dual action which means that it plays the role of pulling force
for the upstreamsectionand
of
pushing force in the downstreamsection.
However, this is just the general description to the normal operation state for
the three procedures (SF, CC and hot rolling mill). As a matter
of
fact, SF can not
be a complete steady running, CC can not always keep a steady state
of
inces-
santly casting, and hot rolling mill can not pass pieces under rolling continuously.
In a word, there are always interferential factors in continuation and steadiness
of
operation in steel manufacturing process. Moreover, these factors may be pre-
arranged or occur at random. Thus, it is necessary that the more effective strategy
and measure for the continuous/quasi-continuous mass flow in the steel manufac-
turing process to be investigated, i.e. how to coordinate and buffer the differences
between pushing and pulling force regarding contination/quasi-contination. This
running strategy, which generally can simulate the "loop" function between hous-
ings
of
hot strip mill, up to make per second flowrate equal. Therefore, it is neces-
sary to establish a
"generalized loop engineering", or generally speaking,flexible
buff
er engineering in the steel manufacturing process. For such a large-scale,
complex systems
of
the steel production process, the time scale is chosen to be
minute, nor second nor hour. That is to say, the concept
of
"per min flowrate
equal" should replace the concept
of
per second or per hour flowrate equal to
keep continuous/quasi-continuous running
of
steel manufacturing process. That
means to establish some buffering procedures or devices between the sources
of
pushing and pulling force to be as the "flexible loops" for the mass flow
of
steel
manufacturing process. Different "loop" functions, various "loop" capacities and
"loop" numbers may be applied to make the mass flowrate buffer, tempera-
ture/energy parameter buffer, quality/shape parameter buffer, time-characteristic
parameter buffer etc. The coordination
of
push-pull makes the mass flow continu-
ous running without intermittence and accumulation, that increases the productive
efficiency and benefit remarkably. The coordination among pushing force, buffer-
ing and pulling force fills in fact the role
of
"generalized loop engineering". The