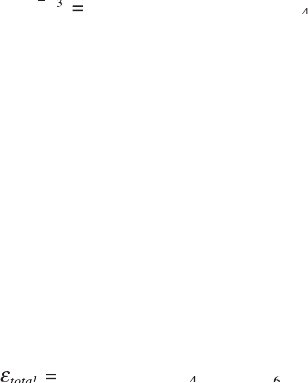
141Durability and reliability in diesel engine system design
© Woodhead Publishing Limited, 2011
The lifetime of the component in LCF can be predicted by either plastic
strain amplitude or stress amplitude, with the former being more appropriate
and commonly used. In fact, both maximum tensile stress and the strain
amplitude are useful in LCF life prediction. In general, larger plastic strains
cause a shorter life. Better material ductility can improve the LCF life. Higher
material strength may actually reduce the component life if it is subject to
LCF failure since higher material strength usually reduces ductility.
Under a single type of cyclic loading (i.e., the plastic strain range remains
constant in every cycle of the loading) the plastic strain deformation is
usually predicted by the Manson–Cof n relation developed in the 1950s.
The formula characterizes the relationship between the plastic strain range
and LCF life as follows:
i.e.,
2.6
where De
p
is the plastic strain range, N
f
is the number of load cycles to
reach fatigue failure. Note that 2N
f
is the number of reversals to failure in
the stress–strain hysteresis loop. C
3
and C
4
are empirical material constants.
C
3
is known as the fatigue ductility exponent, usually ranging from –0.5
to –0.7. Higher temperature gives a more negative value of C
3
. C
4
is an
empirical constant known as the fatigue ductility coef cient, which is closely
related to the fracture ductility of the material. It is observed from equation
2.6 that a larger plastic strain range leads to a lower number of cycles of
the fatigue life.
A more general relationship was later proposed by Mason by using the
total strain, including both elastic and plastic strains, as the indicator of LCF
failure:
DD
ee
DD
lp
DD
ee
DD =DD
ee
DD
lp
DD
ee
DD
DD
ee
DD
lp
DD
ee
DD DD
ee
DD
lp
DD
ee
DD
2.7
where De
e
is the elastic strain range which is equal to the elastic stress
range divided by the Young’s modulus, De
p
is the plastic strain range,
C
6
is a coef cient related to the fatigue strength, C
3
and C
5
are material
constants. Equation 2.7 can be used to construct the strain–life diagram for
the component on a logarithmic scale (Fig. 2.3c).
The LCF in diesel engines is usually caused by large thermal stresses at
high component temperatures which are higher than the creep temperature.
The creep temperature is usually equal to 30–50% of the melting temperature
of the metal in Kelvin. Many factors such as creep, relaxation, oxidation,
and material degradation start to play important roles at high temperatures.
At low temperatures the fatigue mechanism is predominant, while at high
temperatures creep may become more important. The life of high temperature
LCF is usually signi cantly lower than the life at lower temperatures (Fig.
Diesel-Xin-02.indd 141 5/5/11 11:44:51 AM