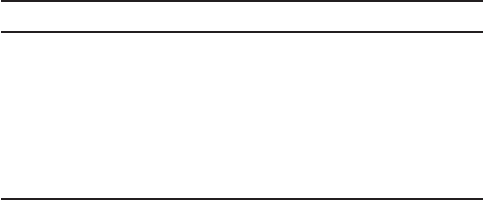
COAGULATION AND FLOCCULATION 6-37
Flocculation Mixing Design Criteria
While rapid mix is the most important physical factor affecting coagulant efficiency, flocculation is
the most important factor affecting particle-removal efficiency. The objective of flocculation is to
bring the particles into contact so that they will collide, stick together, and grow to a size that will
readily settle or filter out. Enough
mixing must be provided to bring the floc into contact and to keep
the floc from settling in the flocculation basin. Too much mixing will shear the floc particles so that
the floc is small and finely dispersed. Therefore, the velocity gradient must be controlled within a
relatively narrow range. Flexibility should also be bu
ilt into the flocculator so that the plant operator
can vary the G value by a factor of two to three. Heavier floc and higher suspended solids concen-
trations require more mixing to keep the floc in suspension. For example, softening floc is heavier
than coagulation floc and, therefore, requires a higher G value to flocculate. This is reflected in the
reco
mmended G values shown in Table 6-6 . An increase in the floc concentration (as measured
by the suspended solids concentration) also increases the required G. Although GLUMRB (2003)
specifies a minimum detention time of 30 minutes for flocculation, cu
rrent practice is to use shorter
times that are adjusted by temperature. With water temperatures of approximately 20 C, modern
plants provide about 20 minutes of flocculation time at plant capacity. With lower temperatures,
the detention time is increased. At 15 C the detention time is in
creased by 7 percent, at 10 C it is
increased 15 percent, and at 5 C it is increased 25 percent.
Flocculation Basin. The flocculation basin should be divided into at least three compartments.
The velocity gradient is tapered so that the G values decrease from the first c
ompartment to the last
and that the average of the compartments is the design value selected from Table 6-6 . GLUMRB
(2003) recommends flow through velocities be not less than 0.15 m/s nor greater than 0.45 m/s.
Water depths in the basin range from 3 to 5 m (Kawamura, 2000). The velocity of flow from the
flocculation basin to the settling basin s
hould be low enough to prevent shear and breakup of the
floc but high enough to keep the floc in suspension.
Baffle Wall. A baffle wall is used to separate the flocculation basin compartments ( Figure 6-19 ).
The top of the baffle is slightly submerged (1 to 2 cm), and the bottom should have a space of 2
to 3 cm above the floor to allow for drainage and sludge re
moval (Kawamura, 2000). Each baffle
should have orifices that are uniformly distributed over the vertical surface. The size should be
selected with the objective of providing a velocity gradient that does not exceed the gradient in
the compartment immediately upstream.
TABLE 6-6
Gt values for flocculation
Type
G, s
1
Gt (unitless)
Low-turbidity, color
removal coagulation
20–70 60,000 to 200,000
High-turbidity, solids
removal coagulation
30–80 36,000 to 96,000
Softening, 10% solids 130–200 200,000 to 250,000
Softening, 39% solids 150–300 390,000 to 400,000