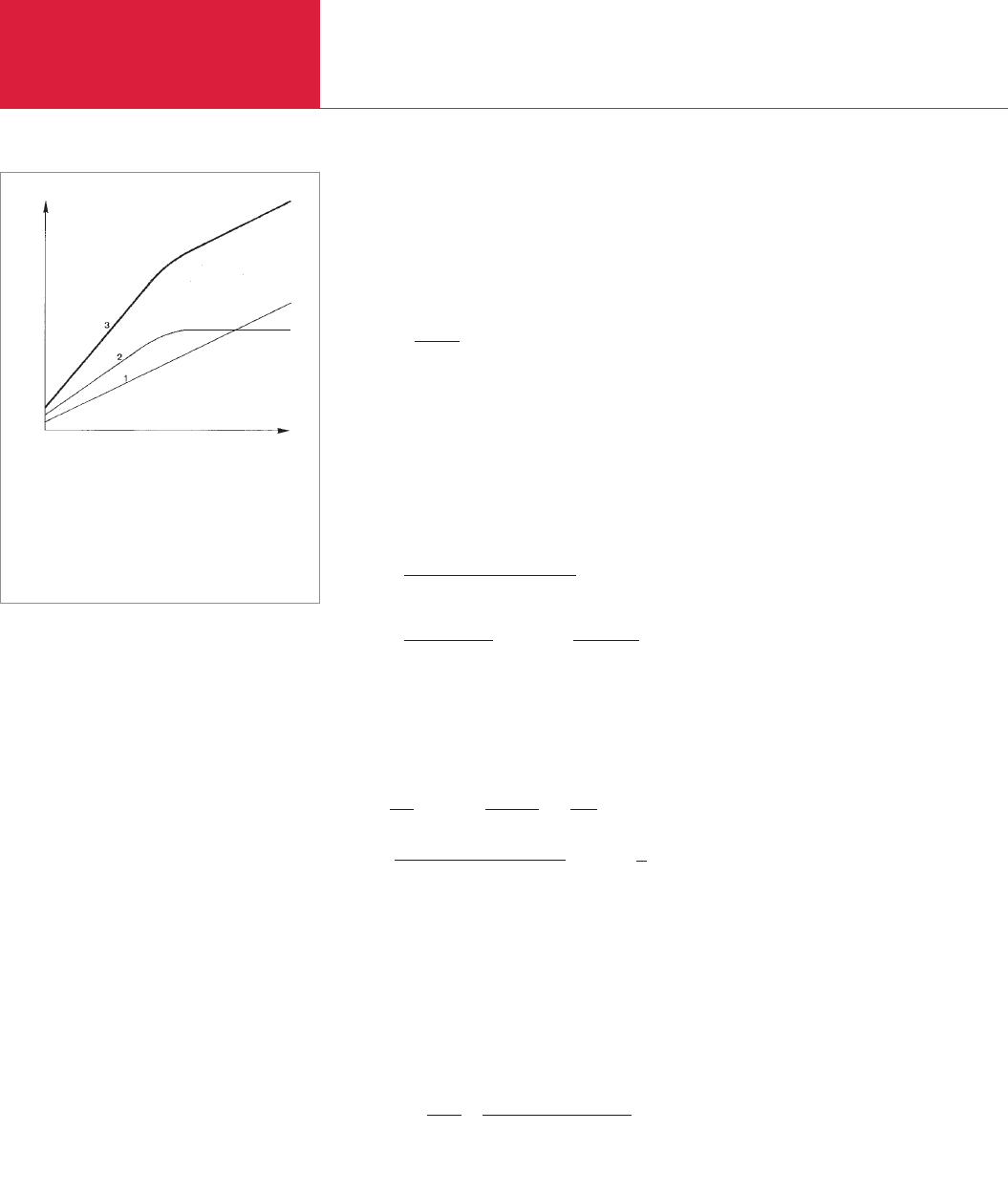
Leak Detection
Fundamentals of Vacuum Technology
D00.108
LEYBOLD VACUUM PRODUCTS AND REFERENCE BOOK 2001/2002
ciently free of outgassing) will decline
through time since these will practically
always be condensable vapors for which
an equilibrium pressure is reached at
some time (see Fig. 5.5). The valve at the
pump end of the evacuated vacuum vessel
will be closed in preparation for pressure
rise measurements. Then the time is mea-
sured during which the pressure rises by a
certain amount (by one power of ten, for
example). The valve is opened again and
the pump is run again for some time, fol-
lowing which the process will be repeated.
If the time noted for this same amount of
pressure rise remains constant, then a leak
is present, assuming that the waiting peri-
od between the two pressure rise trials
was long enough. The length of an appro-
priate waiting period will depend on the
nature and size of the device. If the pres-
sure rise is more moderate during the
second phase, then the rise may be assu-
med to result from gases liberated from
the inner surfaces of the vessel. One may
also attempt to differentiate between leaks
and contamination by interpreting the
curve depicting the rise in pressure. Plot-
ted on a graph with linear scales, the curve
for the rise in pressure must be a straight
line where a leak is present, even at higher
pressures. If the pressure rise is due to
gas being liberated from the walls (owing
ultimately to contamination), then the
pressure rise will gradually taper off and
will approach a final and stable value. In
most cases both phenomena will occur
simultaneously so that separating the two
causes is often difficult if not impossible.
These relationships are shown schematic-
ally in Figure 5.5. Once it has become clear
that the rise in pressure is due solely to a
real leak, then the leak rate can be deter-
mined quantitatively from the pressure
rise, plotted against time, in accordance
with the following equation:
(5.3)
Example: Once the vacuum vessel with a
volume of 20 l has been isolated from the
pump, the pressure in the apparatus rises
from 1·10
-4
mbar to 1·10
-3
mbar in 300 s.
Thus, in accordance with equation 5.2, the
leak rate will be
The leak rate, expressed as mass flow
∆m / ∆t, is derived from equation 5.1 at
Q
L
= 6 · 10
-5
mbar · l/s, T = 20 °C and the
molar mass for air (M = 29 g/mole) at
If the container is evacuated with a
TURBOVAC 50 turbomolecular pump, for
example (S = 50 l/s), which is attached to
the vacuum vessel by way of a shut-off
valve, then one may expect an effective
pumping speed of about S
eff
= 30 l/s. Thus
the ultimate pressure will be
Naturally it is possible to improve this ulti-
mate pressure, should it be insufficient, by
using a larger-capacity pump (e.g. the
TURBOVAC 151) and at the same time to
reduce the pump-down time required to
reach ultimate pressure.
Today leak tests for vacuum systems are
usually carried out with helium leak detec-
tors and the vacuum method (see Section
5.7.1). The apparatus is evacuated and a
test gas is sprayed around the outside. In
this case it must be possible to detect (on
the basis of samplings inside the appara-
p
end
Q
L
S
eff
mbar s
s
mbar
= =
–
⋅⋅ ⋅
–
⋅
–
= ⋅
–
6 10
5 1
30
1
2 10
6
`
`
Q
m
t
mbar
s
g
mol
mol K
mbar
K
g
s
L
= = ⋅ ⋅
⋅
⋅ ⋅
⋅
⋅
⋅ ⋅ ⋅
= ⋅
–
–
∆
∆
6 10 29
8314 293 10
7 10
5
2
8
`
`.
Q
L
mbar
s
=
⋅
–
− ⋅
–
⋅
=
⋅
–
⋅
=
–
⋅
1 10
3
1 10
4
20
300
9 10
4
20
300
6 10
5
⋅
`
tus) the test gas which has passed through
leaks and into the apparatus. Another opti-
on is to use the positive-pressure leak test.
A test gas (helium) is used to fill the appa-
ratus being inspected and to build up a
slight positive pressure; the test gas will
pass to the outside through the leaks and
will be detected outside the device. The
leaks are located with leak sprays (or soap
suds, 5.4.5) or – when using He or H
2
as
the test gas – with a leak detector and snif-
fer unit (5.7.2).
5.4.2 Pressure drop test
The thinking here is analogous to that for
the pressure rise method (Section 5.4.1).
The method is, however, used only rarely
to check for leaks in vacuum systems. If
this is nonetheless done, then gauge pres-
sure should not exceed 1 bar since the
flange connectors used in vacuum techno-
logy will as a rule not tolerate higher pres-
sures. Positive pressure testing is, on the
other hand, a technique commonly
employed in tank engineering. When dea-
ling with large containers and the long test
periods they require for the pressure drop
there it may under certain circumstances
be necessary to consider the effects of
temperature changes. As a consequence it
may happen, for example, that the system
cools to below the saturation pressure for
water vapor, causing water to condense;
this will have to be taken into account
when assessing the pressure decline.
5.4.3 Leak test using
vacuum gauges which
are sensitive to the type
of gas
The fact that the pressure reading at vacu-
um gauges (see Section 3.3) is sensitive to
the type of gas involved can, to a certain
extent, be utilized for leak detection purpo-
ses. Thus it is possible to brush or spray
suspected leaks with alcohol. The alcohol
vapors which flow into the device – the
thermal conductivity and ionizablity of
which will vary greatly from the same pro-
perties for air – will affect and change
pressure indication to a greater or lesser
Fig. 5.5 Pressure rise within a vessel after the pump is
switched off
1 Leak
2 Gas evolved from the container walls
3 Leak + gas evolution
Time
Pressure
D00 E 19.06.2001 21:39 Uhr Seite 108