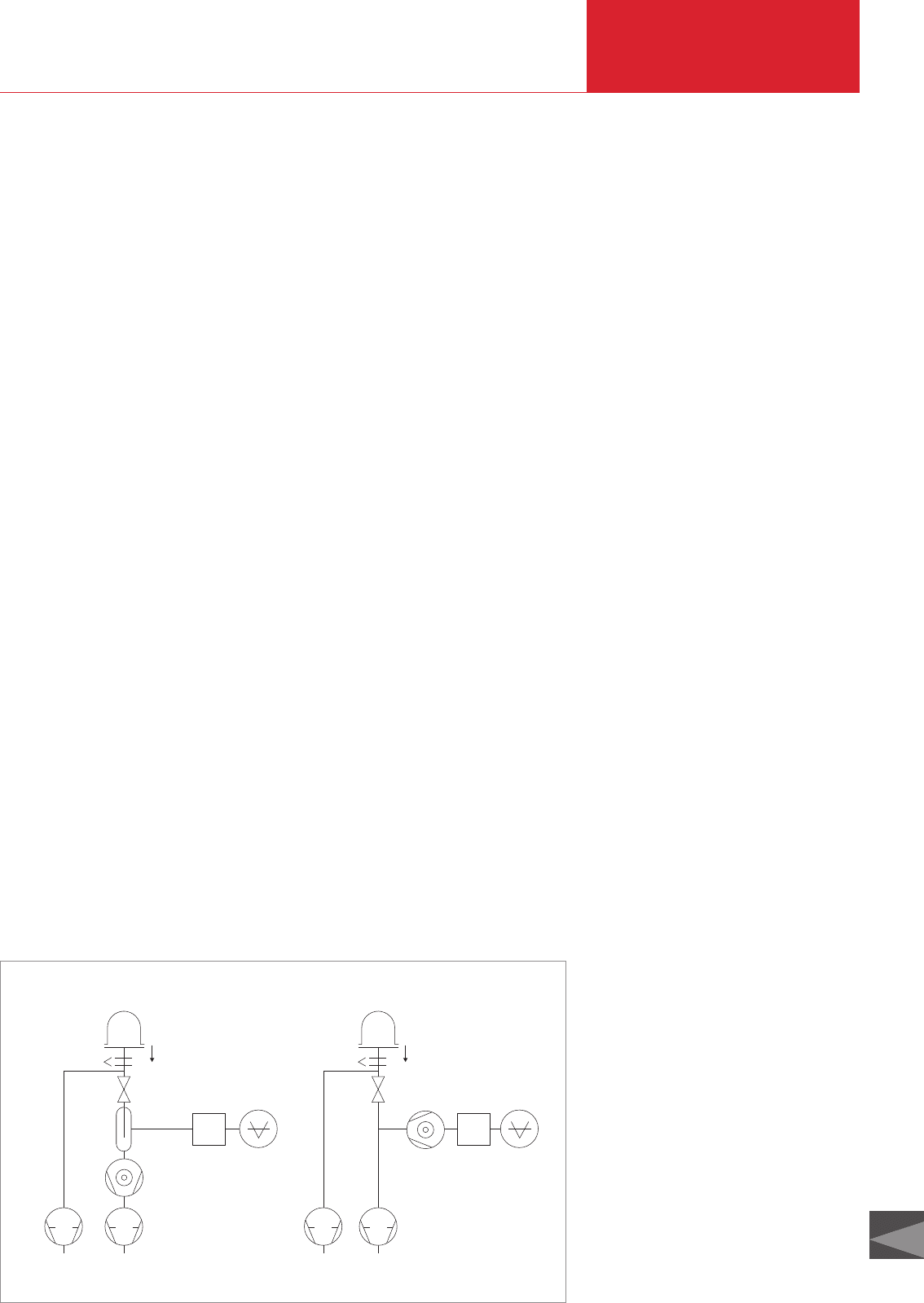
Leak Detection
Fundamentals of Vacuum Technology
D00.115
LEYBOLD VACUUM PRODUCTS AND REFERENCE BOOK 2001/2002
5.5.2.6 Direct-flow and counter-flow
leak detectors
Figure 5.12 shows the vacuum schematic
for the two leak detector types. In both
cases the mass spectrometer is evacuated
by the high vacuum pumping system com-
prising a turbomolecular pump and a
rotary vane pump. The diagram on the left
shows a direct-flow leak detector. Gas
from the inlet port is admitted to the spec-
trometer via a cold trap. It is actually equi-
valent to a cryopump in which all the
vapors and other contaminants condense.
(The cold trap in the past also provided
effective protection against the oil vapors
of the diffusion pumps used at that time).
The auxiliary roughing pump system ser-
ves to pre-evacuate the components to be
tested or the connector line between the
leak detector and the system to be tested.
Once the relatively low inlet pressure
(pumping time!) has been reached, the
valve between the auxiliary pumping
system and the cold trap will be opened for
the measurement. The Seff used in equati-
on 5.4b is the pumping speed of the tur-
bomolecular pump at the ion source loca-
tion:
Q
He
= p
He
· S
eff,turbomolecular pump ion source
(5.5a)
In the case of direct-flow leak detectors, an
increase in the sensitivity can be achieved
by reducing the pumping speed, for exam-
ple by installing a throttle between the tur-
bomolecular pump and the cold trap. This
is also employed to achieve maximum
sensitivity. To take an example:
The smallest detectable partial pressure
for helium is
p
min,He
= 1 · 10
-12
mbar. The pumping
speed for helium would be S
He
= 10 l/s.
Then the smallest detectable leak rate is
Q
min
= 1 · 10
-12
mbar · 10 l/s
= 1 · 10
-11
mbar · l/s. If the pumping speed
is now reduced to 1/s, then one will achie-
ve the smallest detectable leak rate of
1 · 10
-12
mbar · l/s. One must keep in
mind, however, that with the increase in
the sensitivity the time constant for achie-
ving a stable test gas pressure in the test
specimen will be correspondingly larger
(see Section 5.5.2.9).
In Figure 5.12 the right hand diagram
shows the schematic for the counter-flow
leak detector. The mass spectrometer, the
high vacuum system and also the auxiliary
roughing pump system correspond exact-
ly to the configuration for the direct-flow
arrangement. The feed of the gas to be
examined is however connected between
the roughing pump and the turbomolecu-
lar pump. Helium which reaches this
branch point after the valve is opened will
cause an increase in the helium pressure
in the turbomolecular pump and in the
mass spectrometer. The pumping speed
S
eff
inserted in equation 5.4b is the pum-
ping speed for the rotary vane pump at the
branch point. The partial helium pressure
established there, reduced by the helium
compression factor for the turbomolecular
pump, is measured at the mass spectro-
meter. The speed of the turbomolecular
pump in the counter-flow leak detectors is
regulated so that pump compression also
remains constant. Equation 5.5b is derived
from equation 5.5a:
Q
He
= p
He
· S
eff
· K (5.5b)
S
eff
= effective pumping speed at the
rotary vane pump at the
branching point
K = Helium compression factor at
the turbomolecular pump
The counter-flow leak detector is a particu-
lar benefit for automatic vacuum units
since there is a clearly measurable pressu-
re at which the valve can be opened, name-
ly the roughing vacuum pressure at the
turbomolecular pump. Since the turbo-
molecular pump has a very large compres-
sion capacity for high masses, heavy mo-
lecules in comparison to the light test gas,
helium (M = 4), can in practice not reach
the mass spectrometer. The turbomolecu-
lar pump thus provides ideal protection for
the mass spectrometer and thus elimina-
tes the need for an LN
2
cold tap, which is
certainly the greatest advantage for the
user. Historically, counter-flow leak detec-
tors were developed later. This was due in
part to inadequate pumping speed stabili-
ty, which for a long time was not sufficient
with the rotary vane pumps used here. For
both types of leak detector, stationary
units use a built-in auxiliary pump to assist
in the evacuation of the test port. With por-
table leak detectors, it may be necessary to
provide a separate, external pump, this
being for weight reasons.
5.5.2.7 Partial flow operation
Where the size of the vacuum vessel or the
leak makes it impossible to evacuate the
test specimen to the necessary inlet pres-
sure, or where this would simply take too
long, then supplementary pumps will have
to be used. In this case the helium leak
detector is operated in accordance with the
so-called “partial flow” concept. This
means that usually the larger part of the
gas extracted from the test object will be
removed by an additional, suitably dimen-
sioned pump system, so that only a part of
the gas stream reaches the helium leak
detector (see Fig. 5.13). The splitting of
the gas flow is effected in accordance with
the pumping speed prevailing at the bran-
ching point. The following then applies:
Q
Vacuum vessel
= γ · Display
Leak detector
(5.6)
where g is characterized as the partial flow
ratio, i.e. that fraction of the overall leak
current which is displayed at the detector.
D00
Test specimen Test specimen
Test gas stream Test gas stream
pp
LN
p
p
High vacuum pump
High vacuum pump
Roughing pumpRoughing pump
Cold trap:
S = 6.1 /s · cm
Fl 1000 cm
S = 6,100 /s
`
`
2
2
≈
Auxiliary pumpAuxiliary pump
< 10 mbar
–4
< 10 mbar
–4
HeHe
2
TOT
TOT
MS MS
Fig. 5.12 Full-flow and counter-flow leak detector
Solution 1: Direct-flow leak detector
Solution 2: Counter-flow leak detector
D00 E 19.06.2001 21:39 Uhr Seite 115