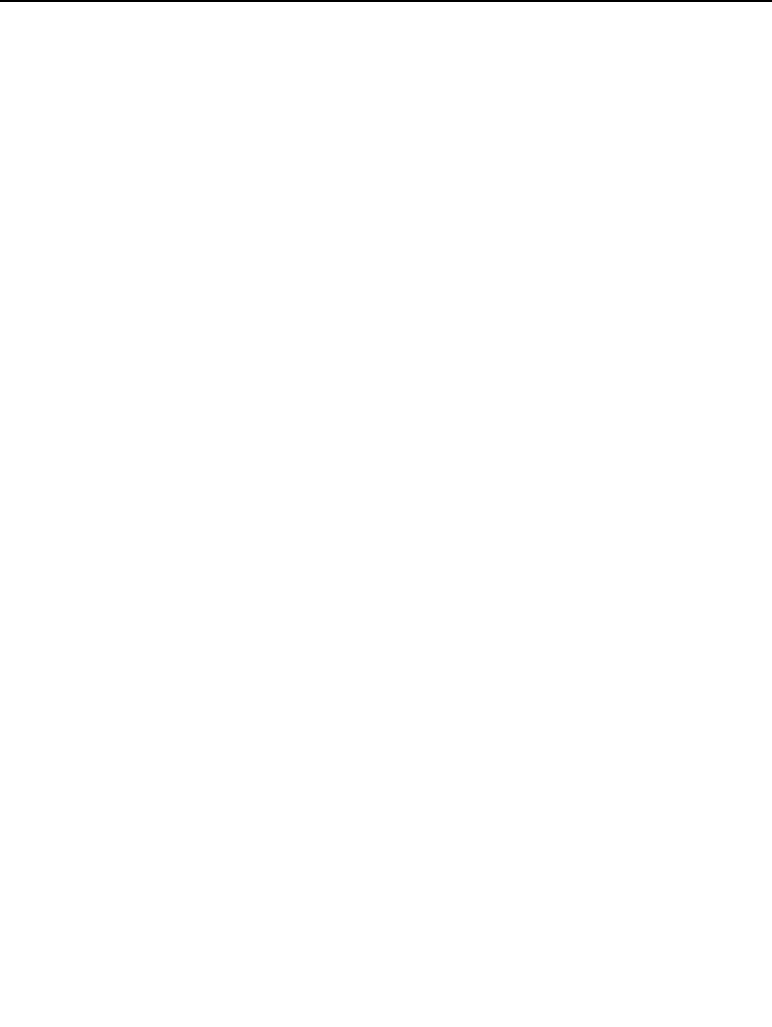
334 27 Special-purpose presses
The fact that the punch holder and punch can be precisely adjusted and the ram is guided with
no play guarantees consistently small tolerances in the finished part and long tool lives. The
manufacturing plants typically used in bulk forming are capital-intensive, and their cost-
efficiency depends crucially upon the percentage of the total production time taken up by non-
productive time and set-up time. Here, tool changing and set-up systems can make a vital con-
tribution to shortening these non-productive times and lengthening the time the press is in
action.
As manufacturing structures can differ greatly as concerns part size, lot size, processing and
the manufacturing sequence, various systems for fast tool changing are available on the mar-
ket: the operator can choose a combination suited to the operation.
With this tool-changing system all the tooling is adjusted and changed fully automatically
when the press set-up is changed. This reduces changeover times drastically. The result is
flexible manufacturing which means these presses can also be used economically for smaller
lot sizes.
The die block, shearing block and punch blocks, which are mounted on a single die plate, are
changed as one unit. The press is equipped with a special device to help carry out the change.
The die block and the die plate are clamped in place with quick-action hydraulic devices which
can easily be released.
The shearing blade, shearing bush, punch and die can still be changed separately, independ-
ently of this fast tool-changing system.
The tooling being changed can be adjusted before it is mounted in the press. For this purpose
the press has a tooling support area for adjusting tools, and a fixed holder for the die block and
die plate, as well as appropriate adjustment devices.
The optimum settings for the X, Y and Z coordinates of a workpiece are determined once for
every stage and then saved in the tooling databank. When the tooling is changed, these saved
parameters can be called up at any time, even when the work is not being done on the press.
This makes tool changing faster, easier and safer. When the conditions of a process are the
same, sound parts are produced right from the first strokes. With this system, a program ad-
justs peripheral units: this is fully automatic. The ejector stroke and return stroke are adjusted
with a motor. The feed system is set up to fit a wide range of diameters so that the grippers do
not need changing when production is switched over.
A numerically controlled transfer system (Figure 27.11) is used to transport the workpieces
within the press. The transfer system and grippers are operated by individually-controlled
electric servo drives. The settings are adjusted using a menu í it is no longer necessary to
change camshafts or adjust cams. These settings are saved in a tooling databank and can be
called up when needed within seconds.