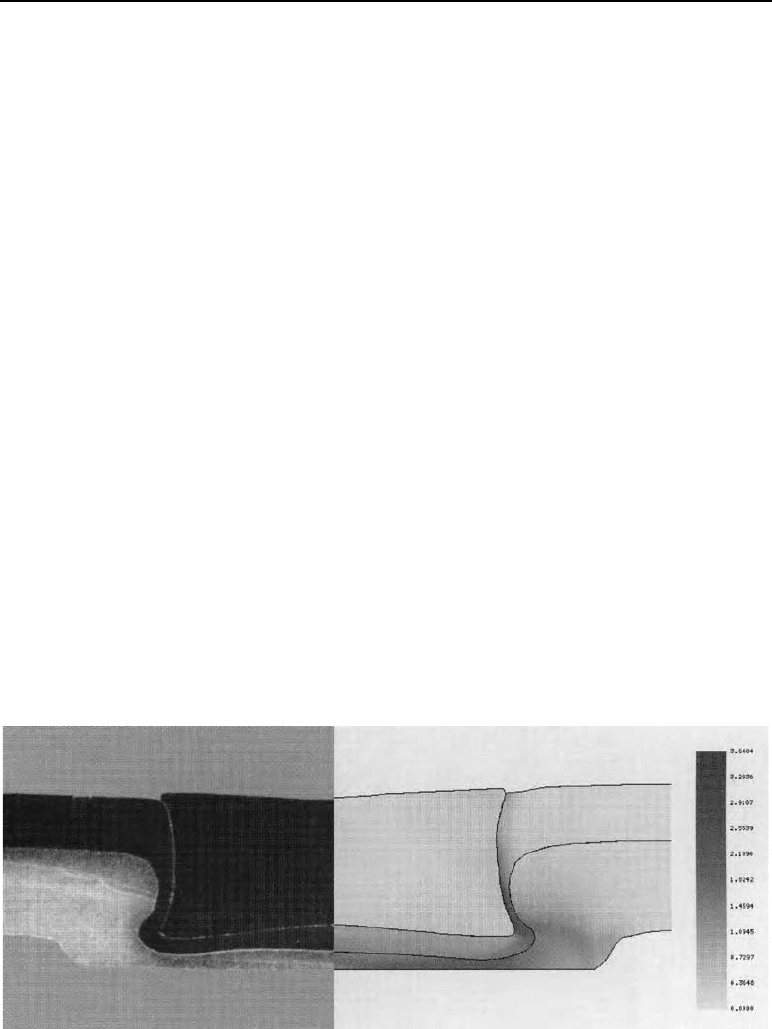
260 20 Joining by forming
20.3.4 Trends in development
Similarly to clinching and punch riveting, again the problems to be solved concern
– cost reduction
– improved joinability for high-strength sheet (use of high-strength rivets, workpiece heat-
ing)
– raised process stability (tolerance for process fluctuations)
– monitoring (monitoring of force is the standard; other possible methods are the analysis of
distance or impact sound)
– realistic calculation of the processes
– reduction of joining force
– accessibility from one side
– raised resistance to corrosion (e.g. new kind of coating in a vacuum)
– combination with other methods (punch riveting and adhesion; internal high-pressure form-
ing and self-piercing semi-tubular riveting with the fluid as an opposing force)
The method described above with clinching, with a single, flat opposing die with no shaping
die, can be used for riveting following the same principle (Figure 20.18) with the following
aims:
– no more concentricity required between punch and die, no outlay for setup, low tooling
wear, high process stability; better accessibility during joining
– bump on underside flatter (good for structural space requirement, appearance, cleaning,
lacquering, hybrid joining with displacement of adhesive in the undercut area)
Figure 20.18 Dieless rivet clinching; left: experiment, right: calculation (Fraunhofer IWU, Chemnitz, Ger-
many)