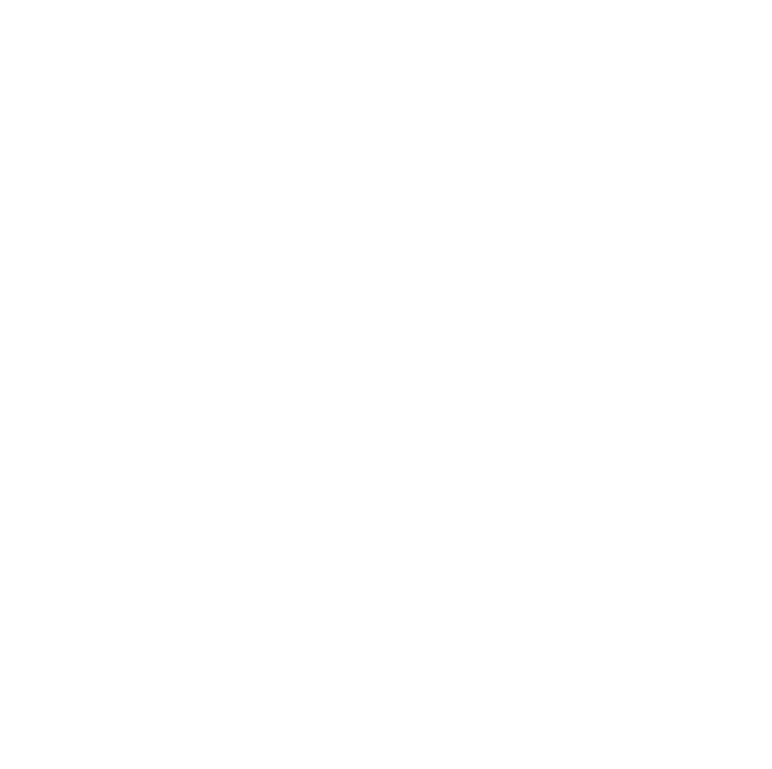
20 Joining by forming
Joining by forming includes all processes where parts being joined or involved in the join-
ing are formed locally, sometimes also completely. The deformation forces may be gener-
ated mechanically, electromagnetically or in another way e.g. by an explosion. Generally,
the joint is kept from unintentionally coming undone by positive locking. With joining, a
difference is made between
– forming wire-shaped bodies (e.g. braiding)
– forming sheet, tube and profiled parts (flanging, bending, clinching) and
– riveting processes (hollow riveting, punch riveting).
This chapter deals with clinching and punch riveting with no pre-punching, as these methods
have been growing in importance since the mid-1990s. The advantages they confer in automo-
bile production mean that they can largely replace conventional resistance spot welding.
Their economic advantages are in the joinability of differing materials (e.g. aluminium with
steel), the longer tooling life and avoiding heat input. With higher-strength sheet in particular,
the latter means that better use can be made of its strength, as the original properties of the
material are not changed thermally.
At the point of joining, the deformation is carried out by deliberately changing the thickness of
the semi-finished product. This is a bulk forming operation made up of different, overlapping
processes, e.g. pushing through, compressing, extrusion.
Difficulties still arise when calculating theoretical values such as the required force and work,
or describing process limits (joinable sheet thicknesses, joinable strengths) due to the complex
triaxial changes in the states of tension and deformation involved. For this reason, until now
development has been shaped by experiments. In future, the increasing use of numerical simu-
lation will reduce the number of experiments needed.