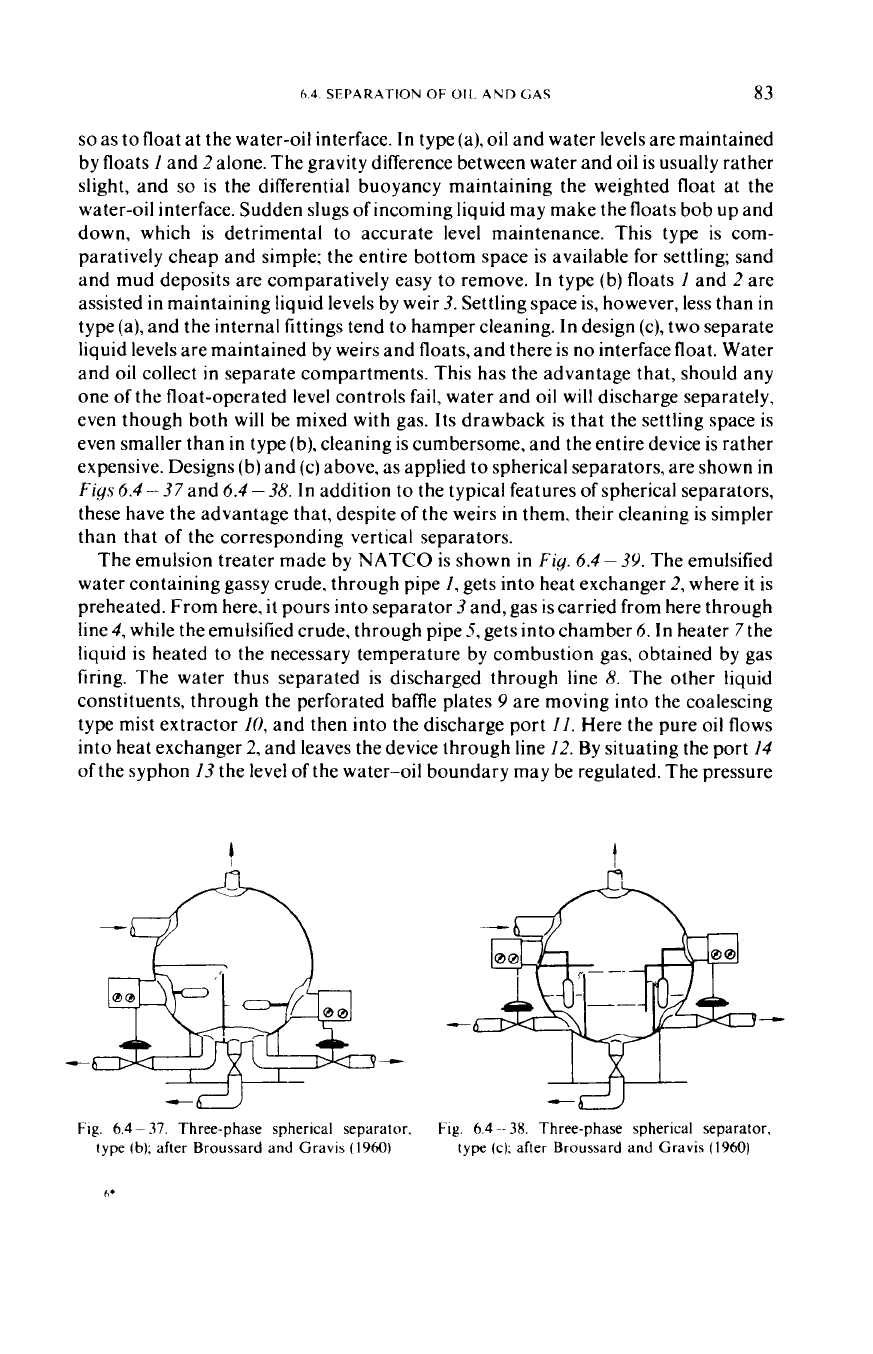
64
SFPARATION
OF
011
AND GAS
83
so
as to float at the water-oil interface.
In
type (a), oil and water levels are maintained
by floats
1
and
2
alone. The gravity difference between water and oil is usually rather
slight, and
so
is the differential buoyancy maintaining the weighted float at the
water-oil interface. Sudden slugs of incoming liquid may make the floats bob up and
down, which is detrimental to accurate level maintenance. This type is com-
paratively cheap and simple; the entire bottom space is available for settling; sand
and mud deposits are comparatively easy
to remove. In type (b) floats
I
and
2
are
assisted
in
maintaining liquid levels by weir
3.
Settling space is, however, less than in
type (a), and the internal fittings tend to hamper cleaning. In design (c), two separate
liquid levels are maintained by weirs and floats, and there is no interface float. Water
and oil collect in separate compartments. This has the advantage that, should any
one of the float-operated level controls fail, water and oil will discharge separately,
even though both
will
be mixed with gas. Its drawback is that the settling space is
even smaller than
in
type (b). cleaning is cumbersome, and the entire device is rather
expensive. Designs (b) and (c) above,
as applied to spherical separators, are shown in
Figs
6.4
-
37
and
6.4
-
38.
In
addition to the typical features of spherical separators,
these have the advantage that, despite of the weirs in them. their cleaning is simpler
than that of the corresponding vertical separators.
The emulsion treater made by NATCO is shown
in
Fig.
6.4
-
3Y.
The emulsified
water containing gassy crude, through pipe
1,
gets into heat exchanger
2,
where
it
is
preheated. From here.
it
pours into separator
3
and, gas is carried from here through
line
4,
while the emulsified crude, through pipe
5,
gets into chamber
6.
In
heater
7
the
liquid is heated
to
the necessary temperature by combustion gas. obtained by gas
firing. The water thus separated is discharged through line
8.
The other liquid
constituents, through the perforated bame plates
9
are moving into the coalescing
type mist extractor
10,
and then into the discharge port
1 1.
Here the pure oil flows
into heat exchanger
2,
and leaves the device through line 12. By situating the port
14
of the syphon
13
the level
of
the water-oil boundary may be regulated. The pressure
I
r4
-“I“_
‘---I-
-
t
c
Fig.
6.4
-
37.
Three-phase spherical separator,
Fig.
6.4
--
38.
Three-phase spherical separator.
type
Ib);
after Broussard and Gravis
(19601
type (c): after Broussard and Gravis
(1960)