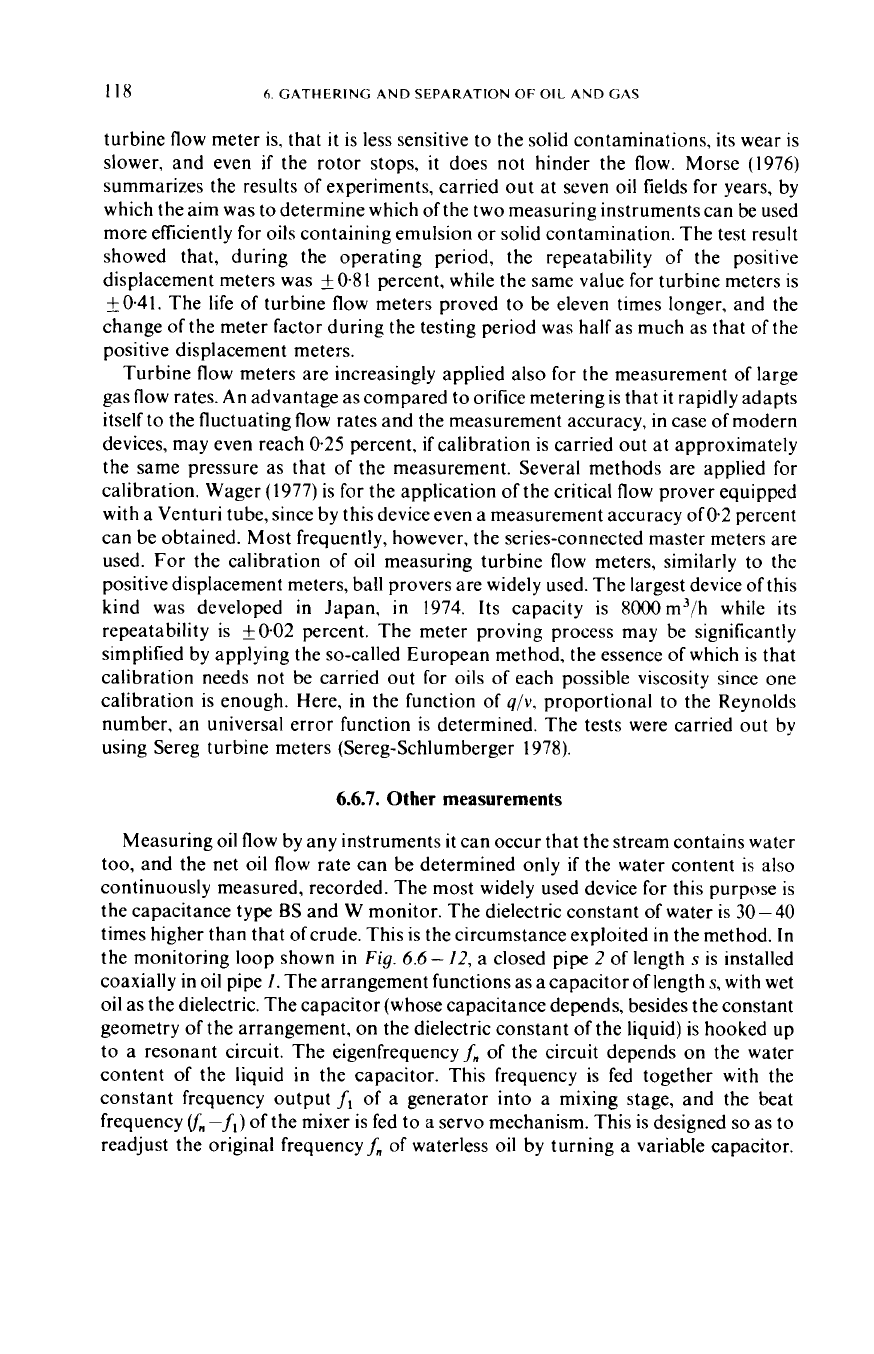
118
6.
GATHERING AND SEPARATION
OF
OIL
AND
GAS
turbine flow meter is, that
it
is less sensitive to the solid contaminations, its wear is
slower, and even
if
the rotor stops,
it
does not hinder the flow. Morse (1976)
summarizes the results of experiments, carried out at seven oil fields for years, by
which the aim was to determine which ofthe two measuring instruments can be used
more efficiently for oils containing emulsion
or
solid contamination. The test result
showed
that, during the operating period, the repeatability of the positive
displacement meters was
f0.81
percent, while the same value for turbine meters is
kO.41.
The life of turbine flow meters proved to be eleven times longer, and the
change of the meter factor during the testing period was half as much as that of the
positive displacement meters.
Turbine flow meters are increasingly applied also for the measurement of large
gas flow rates.
An
advantage as compared
to
orifice metering is that
it
rapidly adapts
itself to the fluctuating flow rates and the measurement accuracy,
in
case of modern
devices, may even reach
0.25
percent,
if
calibration is carried out at approximately
the same pressure as that of the measurement. Several methods are applied for
calibration. Wager (1977) is for the application of the critical flow prover equipped
with a Venturi tube, since by this deviceeven a measurement accuracy of0.2 percent
can be obtained. Most frequently, however, the series-connected master meters are
used.
For
the calibration of oil measuring turbine flow meters, similarly to the
positive displacement meters, ball provers are widely used. The largest device of this
kind was developed
in Japan,
in
1974. Its capacity is 8000m3/h while its
repeatability is
kO.02
percent. The meter proving process may be significantly
simplified by applying the so-called European method, the essence of which is that
calibration needs not be carried out for oils of each possible viscosity since one
calibration is enough. Here, in the function of
q/v,
proportional to the Reynolds
number, an universal error function is determined. The tests were carried out by
using Sereg turbine meters (Sereg-Schlumberger 1978).
6.6.7.
Other measurements
Measuring oil flow by any instruments
it
can occur that the stream contains water
too, and the net oil flow rate can be determined only
if
the water content is also
continuously measured, recorded. The most widely used device for this purpose is
the capacitance type
BS
and W monitor. The dielectric constant of water is 30-40
times higher than that ofcrude. This is the circumstance exploited in the method.
In
the monitoring loop shown in
Fig.
6.6
-
12, a closed pipe
2
of
length
s
is installed
coaxially in oil pipe
I.
The arrangement functions as a capacitor of length
s,
with
wet
oil as the dielectric. The capacitor (whose capacitance depends, besides the constant
geometry of the arrangement, on the dielectric constant of the liquid) is hooked up
to a resonant circuit. The eigenfrequencyf, of the circuit depends on the water
content of the liquid in the capacitor. This frequency is fed together with the
constant frequency output
fi
of a generator into a mixing stage, and the beat
frequency
rm-f,)
of the mixer is fed to a servo mechanism. This is designed
so
as to
readjust the original frequencyf, of waterless oil by turning a variable capacitor.