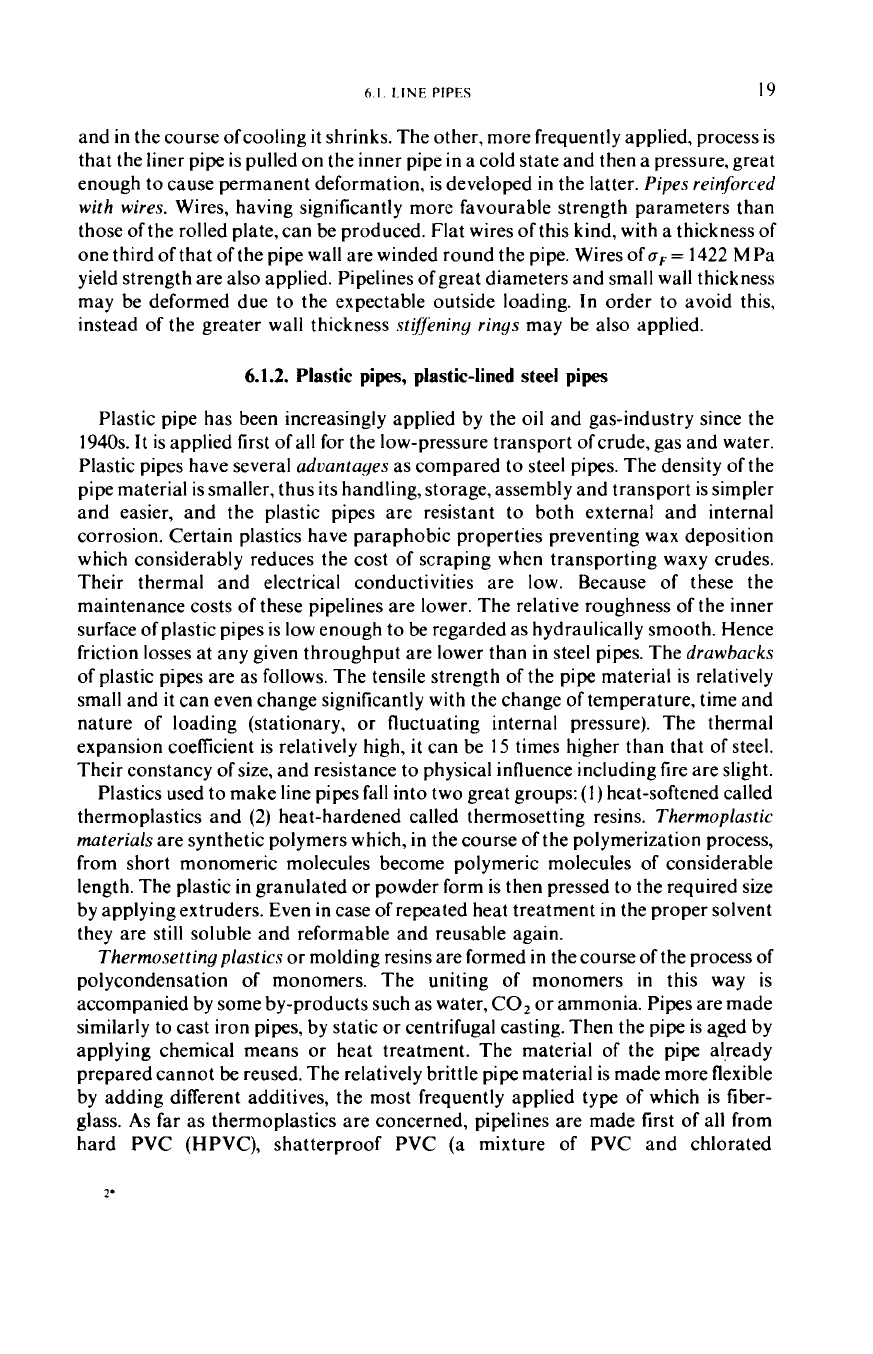
6.1.
LINE
PIPES
19
and in the course ofcooling
it
shrinks. The other, more frequently applied, process is
that the liner pipe is pulled on the inner pipe in a cold state and then a pressure, great
enough to cause permanent deformation, is developed
in
the latter.
Pipes reinforced
with wires.
Wires, having significantly more favourable strength parameters than
those of the rolled plate, can be produced. Flat wires of this kind, with a thickness of
one third of that of the pipe wall are winded round the pipe. Wires of
oF
=
1422
M
Pa
yield strength are also applied. Pipelines ofgreat diameters and small wall thickness
may be deformed due
to
the expectable outside loading.
In
order to avoid this,
instead of the greater wall thickness
stflening rings
may be also applied.
6.1.2.
Plastic pipes, plastic-lined steel pipes
Plastic pipe has been increasingly applied by the oil and gas-industry since the
1940s.
It
is applied first of all for the low-pressure transport ofcrude, gas and water.
Plastic pipes have several
advantages
as compared to steel pipes. The density of the
pipe material is smaller, thus its handling, storage, assembly and transport is simpler
and easier, and the plastic pipes are resistant
to
both external and internal
corrosion. Certain plastics have paraphobic properties preventing wax deposition
which considerably reduces the cost of scraping when transporting waxy crudes.
Their thermal and electrical conductivities are low. Because of these the
maintenance costs of these pipelines are lower. The relative roughness of the inner
surface of plastic pipes is low enough to be regarded as hydraulically smooth. Hence
friction losses at any given throughput are lower than in steel pipes. The
drawbacks
of plastic pipes are as follows. The tensile strength of the pipe material is relatively
small and
it
can even change significantly with the change of temperature, time and
nature of loading (stationary,
or
fluctuating internal pressure). The thermal
expansion coefficient is relatively high,
it
can be
15
times higher than that of steel.
Their constancy of size, and resistance to physical influence including fire are slight.
Plastics used to make line pipes fall into two great groups:
(1)
heat-softened called
thermoplastics and
(2)
heat-hardened called thermosetting resins.
Thermoplastic
materials
are synthetic polymers which, in the course
of
the polymerization process,
from short monomeric molecules become polymeric molecules of considerable
length. The plastic in granulated
or
powder form is then pressed to the required size
by applying extruders. Even in case of repeated heat treatment in the proper solvent
they are still soluble and reformable and reusable again.
Thermosetting plastics
or
molding resins are formed in the course of the process of
polycondensation of monomers. The uniting of monomers
in
this way is
accompanied by some by-products such as water,
CO,
or
ammonia. Pipes are made
similarly to cast iron pipes, by static
or
centrifugal casting. Then the pipe is aged by
applying chemical means
or
heat treatment. The material of the pipe already
prepared cannot
be
reused. The relatively brittle pipe material is made more flexible
by adding different additives, the most frequently applied type of which is
fiber-
glass.
As
far as thermoplastics are concerned, pipelines are made first of all from
hard
PVC
(HPVC), shatterproof PVC (a mixture of PVC and chlorated
2'