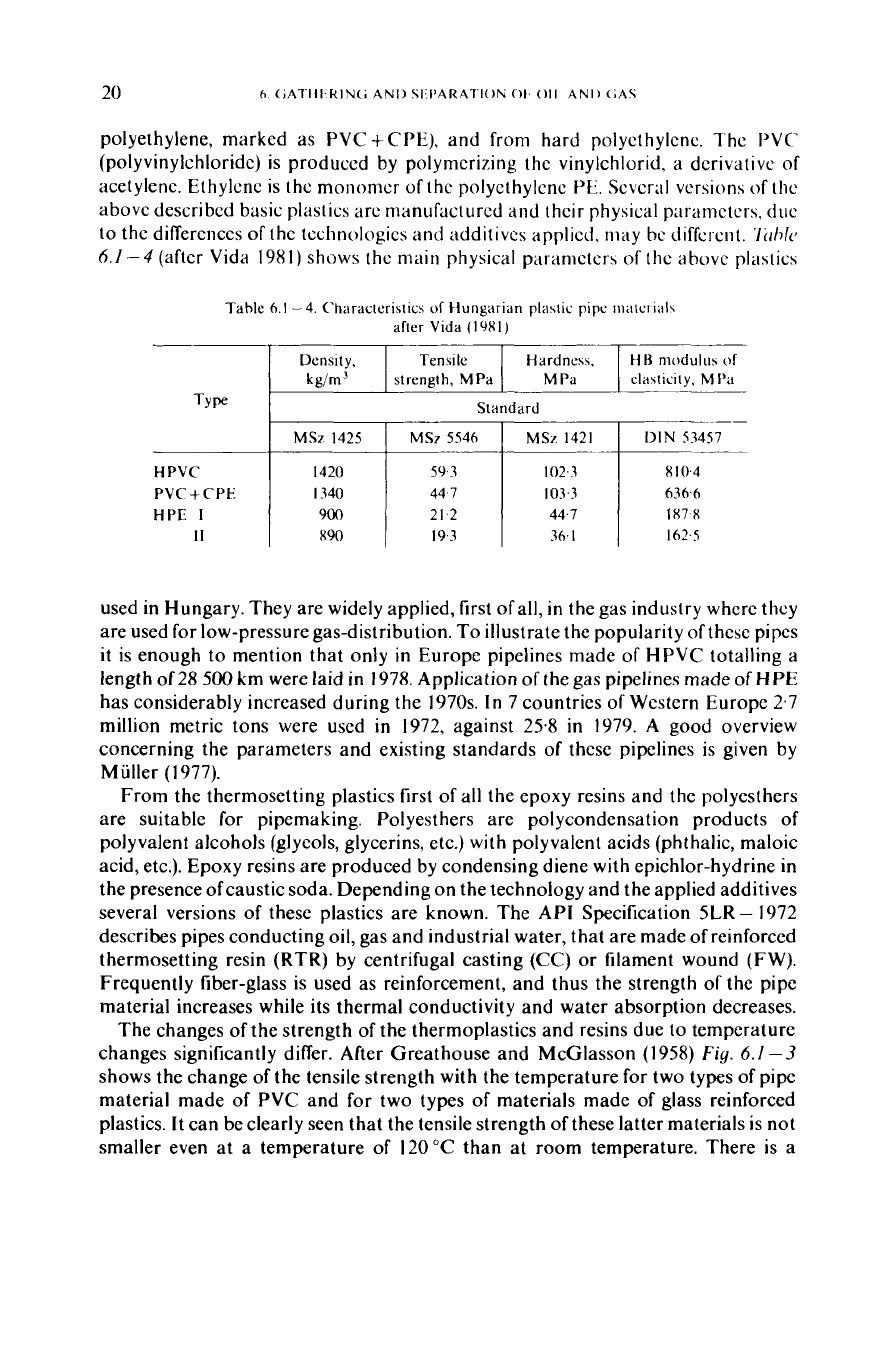
polyethylene, marked as PVC
+
CPE),
and from hard polyethylene. The
I’VC‘
(polyvinylchloride) is produced by polymerizing thc vinylchlorid, a derivative of
acetylene. Ethylene is thc monomer of the polyethylene
PZ;.
Scvcrul
versions of the
above described basic plastics are manufaclured and their physical
parameters,
due
to the differences of the technologies and additives applied, may bc different.
7irhlc
6.1
-4
(after Vida
1981)
shows thc main physical paranietcra of thc above plastics
TY
Pe
H
PVC
PVC
+
CPE
HPE
I
I1
Table
6.1
-4.
Characteristics
of
Hungarian plastic
pipe
niiilciiitl\
after Vida
(1
98
I)
Density, Tensile
Hardnexh.
t1H
nioduluh
of
kg/rn’
strength,
MPa
M
Pa
ela\ticity.
M
I’a
Standard
DIN
53457
___
MS7
5546
MSz
1421
MS7
1425
I420
59.3
102.3
8
10.4
I340
44.7
103.3
636.6
900
21.2
44.7 187.8
x90
19.3
36.
I
162.5
used
in
Hungary. They are widely applied, first ofall,
in
the gas industry where they
are used
for
low-pressure gas-distribution. To illustrate the popularity of these pipes
it
is enough to mention that only
in
Europe pipelines made of HPVC totalling a
length
of
28
500
km were laid
in
1978. Application
of
the gas pipelines made
of
HPE
has considerably increased during the 1970s.
In
7 countries of Western Europe 2.7
million metric tons were used
in
1972, against
25.8
in
1979.
A
good overview
concerning the parameters and existing standards of these pipelines is given by
Muller (1977).
From the thermosetting plastics first of all the epoxy resins and the polyesthers
are suitable for pipemaking. Polyesthers are polycondensation products
of
polyvalent alcohols (glycols, glycerins, etc.) with polyvalent acids (phthalic, maloic
acid, etc.). Epoxy resins are produced by condensing diene with epichlor-hydrine in
the presence
of
caustic soda. Depending on the technology and the applied additives
several versions of these plastics are known. The
API
Specification
5LR
-
1972
describes pipes conducting oil, gas and industrial water, that are made of reinforced
thermosetting resin
(RTR)
by centrifugal casting (CC)
or
filament wound (FW).
Frequently fiber-glass is used as reinforcement, and thus the strength of the pipe
material increases while its thermal conductivity and water absorption decreases.
The changes of the strength of the thermoplastics and resins due to temperature
changes significantly differ. After Greathouse and McGlasson (1958)
Fig.
6.1
-3
shows the change
of
the tensile strength with the temperature for two types
of
pipe
material made
of
PVC and
for
two types
of
materials made
of
glass reinforced
plastics.
It
can be clearly seen that the tensile strength
of
these latter materials is not
smaller even at a temperature
of
120°C than at room temperature. There is a