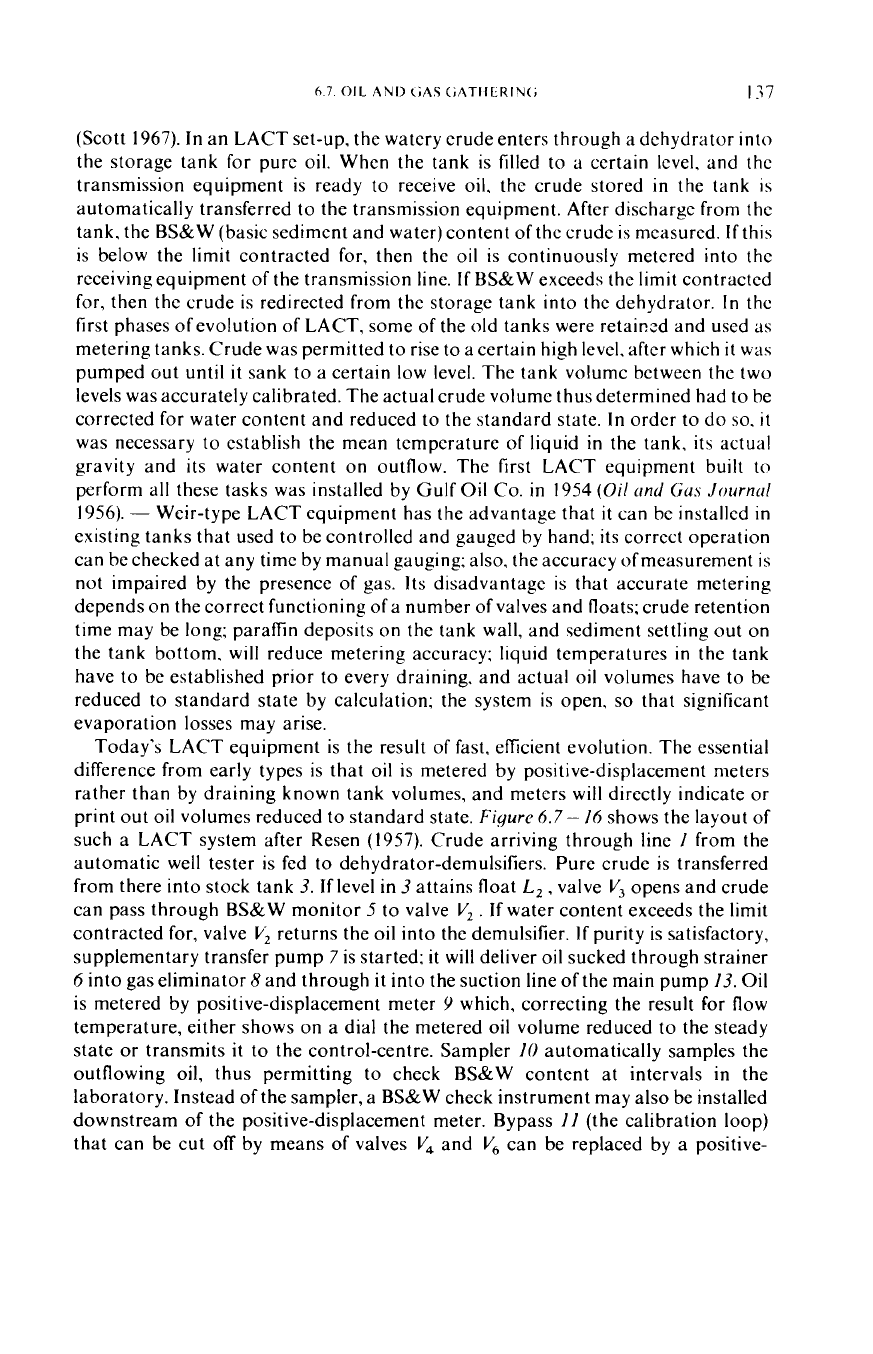
(Scott
1967).
In
an LACT set-up, the watery crude enters through a dehydrator into
the storage tank for pure oil. When the tank is filled to a certain level. and the
transmission equipment is ready to receive oil. the crude stored
in
the tank
is
automatically transferred to the transmission equipment. After discharge from the
tank. the BS&W (basic sediment and water) content of the crude is measured.
If
this
is below the limit contracted for, then the oil is continuously metered into the
receiving equipment of the transmission line.
If
BS&W exceeds the limit contracted
for, then the crude is redirected from the storage tank into the dehydrator.
In
the
first phases of evolution of LACT, some of the old tanks were retaipcd and used as
metering tanks. Crude was permitted to rise to acertain high level, after which
it
was
pumped out
until
it
sank to a certain low level. The tank volumc between the two
levels was accurately calibrated. The actual crude volume thus determined had to
be
corrected for water content and reduced to the standard state.
In
order to do
so.
it
was necessary to establish the mean temperature of liquid
in
the tank, its actual
gravity and its water content on outflow. The first LACT equipment built to
perform all these tasks was installed by Gulf
Oil
Co.
in
1954
(Oil
trnd
Gus
Journril
1956).
-
Weir-type LACT equipment has the advantage that
it
can be installed
in
existing tanks that used to be controlled and gauged by hand; its correct operation
can be checked at any time by manual gauging; also. the accuracy of measurement is
not impaired by the presence of gas. Its disadvantage is that accurate metering
depends on the correct functioning of a number of valves and floats; crude retention
time may be long; paraffin deposits on the tank wall, and sediment settling out on
the tank bottom.
will
reduce metering accuracy; liquid temperatures
in
the tank
have to be established prior to every draining. and actual oil volumes have to be
reduced to standard state by calculation; the system is open,
so
that significant
evaporation losses may arise.
Today’s LACT equipment is the result of fast. efficient evolution. The essential
difference from early types is that oil is metered by positive-displacement meters
rather than by draining known tank volumes, and meters
will
directly indicate
or
print out oil volumes reduced to standard state.
Figure
6.7-
16
shows the layout of
such a LACT system after Resen
(1957).
Crude arriving through line
1
from the
automatic well tester is fed to
dehydrator-demulsifiers.
Pure crude is transferred
from there into stock tank
3.
If
level in
3
attains float
L,
,
valve
V3
opens and crude
can pass through BS&W monitor
5
to valve
Vz
. If water content exceeds the limit
contracted for, valve
V2
returns the oil into the demulsifier.
If
purity is satisfactory,
supplementary transfer pump
7
is started;
it
will
deliver oil sucked through strainer
6
into gas eliminator
8
and through
it
into the suction line of the main pump
13.
Oil
is metered by positive-displacement meter
Y
which, correcting the result
for
flow
temperature, either shows on a dial the metered oil volume reduced to the steady
state
or
transmits it to the control-centre. Sampler
10
automatically samples the
outflowing oil, thus permitting to check BS&W content at intervals
in
the
laboratory. Instead of the sampler, a BS&W check instrument may also be installed
downstream
of
the positive-displacement meter. Bypass
11
(the calibration loop)
that can be cut
off
by means
of
valves
V4
and
V6
can be replaced by a positive-