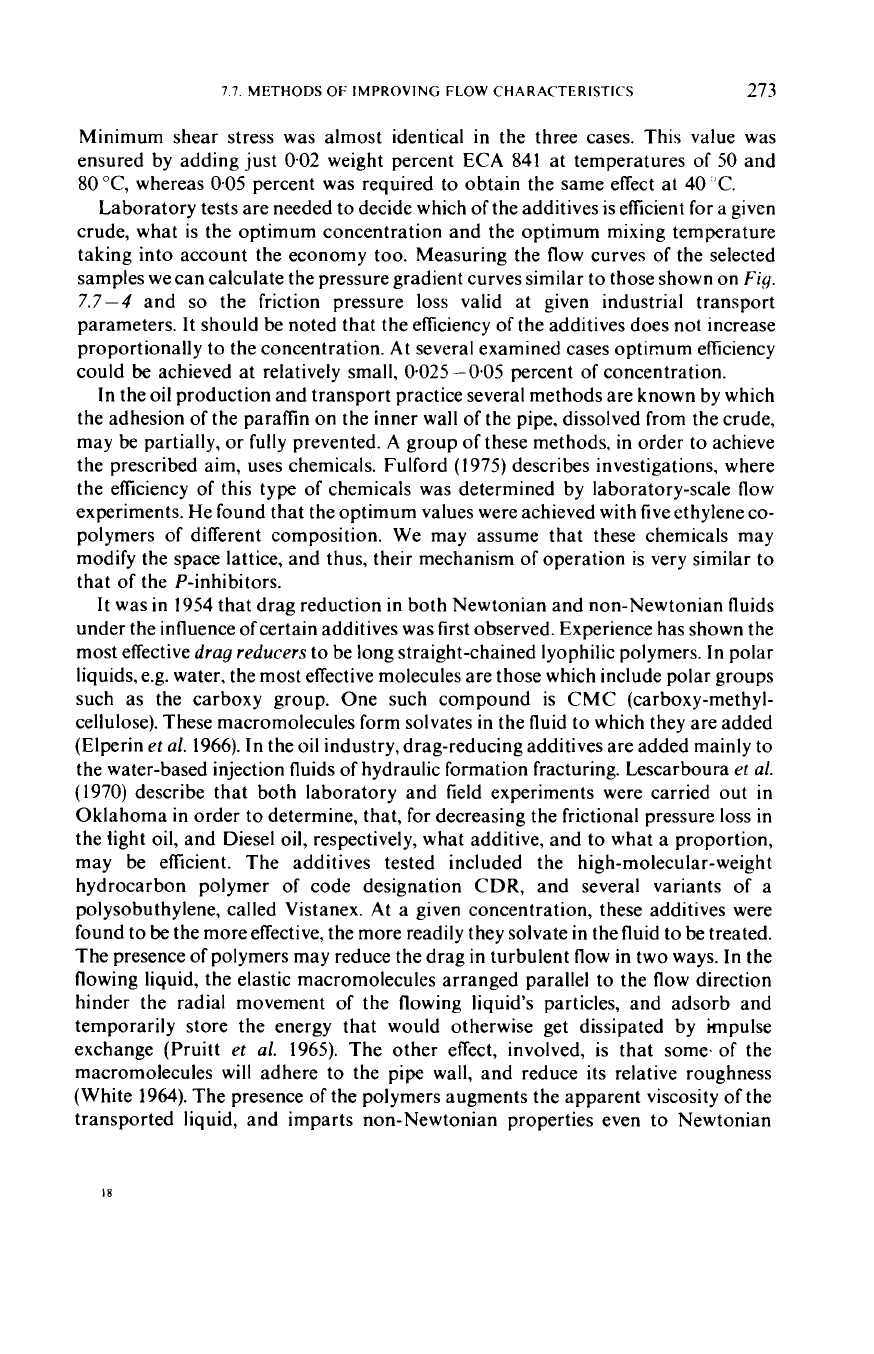
7
7
METHODS
OF
IMPROVING
FLOW
CHARACTERISTICS
273
Minimum shear stress was almost identical in the three cases. This value was
ensured by adding just
0.02
weight percent ECA 841 at temperatures of 50 and
80
"C, whereas 0.05 percent was required to obtain the same effect at
40
C.
Laboratory tests are needed to decide which of the additives is efficient for a given
crude, what is the optimum concentration and the optimum mixing temperature
taking into account the economy too. Measuring the flow curves of the selected
samples we can calculate the pressure gradient curves similar to those shown on
Fig.
7.7-4
and
so
the friction pressure
loss
valid at given industrial transport
parameters. It should be noted that the efficiency of the additives does not increase
proportionally to the concentration.
At
several examined cases optimum efficiency
could
be
achieved at relatively small, 0.025 -0.05 percent of concentration.
In the oil production and transport practice several methods are known by which
the adhesion of the paraffin on the inner wall of the pipe, dissolved from the crude,
may be partially,
or
fully prevented.
A
group of these methods, in order to achieve
the prescribed aim, uses chemicals. Fulford
(
1975) describes investigations, where
the efficiency of this type of chemicals was determined by laboratory-scale flow
experiments. He found that the optimum values were achieved with five ethylene co-
polymers of different composition. We may assume that these chemicals may
modify the space lattice, and thus, their mechanism of operation is very similar to
that of the P-inhibitors.
It was in 1954 that drag reduction in both Newtonian and non-Newtonian fluids
under the influence ofcertain additives was first observed. Experience has shown the
most effective
drag reducers
to
be long straight-chained lyophilic polymers. In polar
liquids, e.g. water, the most effective molecules are those which include polar groups
such as the carboxy group. One such compound is CMC (carboxy-methyl-
cellulose). These macromolecules form solvates in the fluid to which they are added
(Elperin
et
al.
1966).
In the
oil
industry, drag-reducing additives are added mainly to
the water-based injection fluids of hydraulic formation fracturing. Lescarboura
et
al.
(1970) describe that both laboratory and field experiments were carried out in
Oklahoma in order to determine, that, for decreasing the frictional pressure
loss
in
the light oil, and Diesel oil, respectively, what additive, and to what a proportion,
may be efficient. The additives tested included the high-molecular-weight
hydrocarbon polymer of code designation CDR, and several variants
of
a
polysobuthylene, called Vistanex.
At
a given concentration, these additives were
found to
be
the more effective, the more readily they solvate in the fluid to be treated.
The presence of polymers may reduce the drag in turbulent flow in two ways. In the
flowing liquid, the elastic macromolecules arranged parallel to the flow direction
hinder the radial movement of the flowing liquid's particles, and adsorb and
temporarily store the energy that would otherwise get dissipated by impulse
exchange (Pruitt
et
al.
1965).
The other effect, involved, is that some.of the
macromolecules will adhere to the pipe wall, and reduce its relative roughness
(White 1964). The presence of the polymers augments the apparent viscosity of the
transported liquid, and imparts non-Newtonian properties even to Newtonian
I8