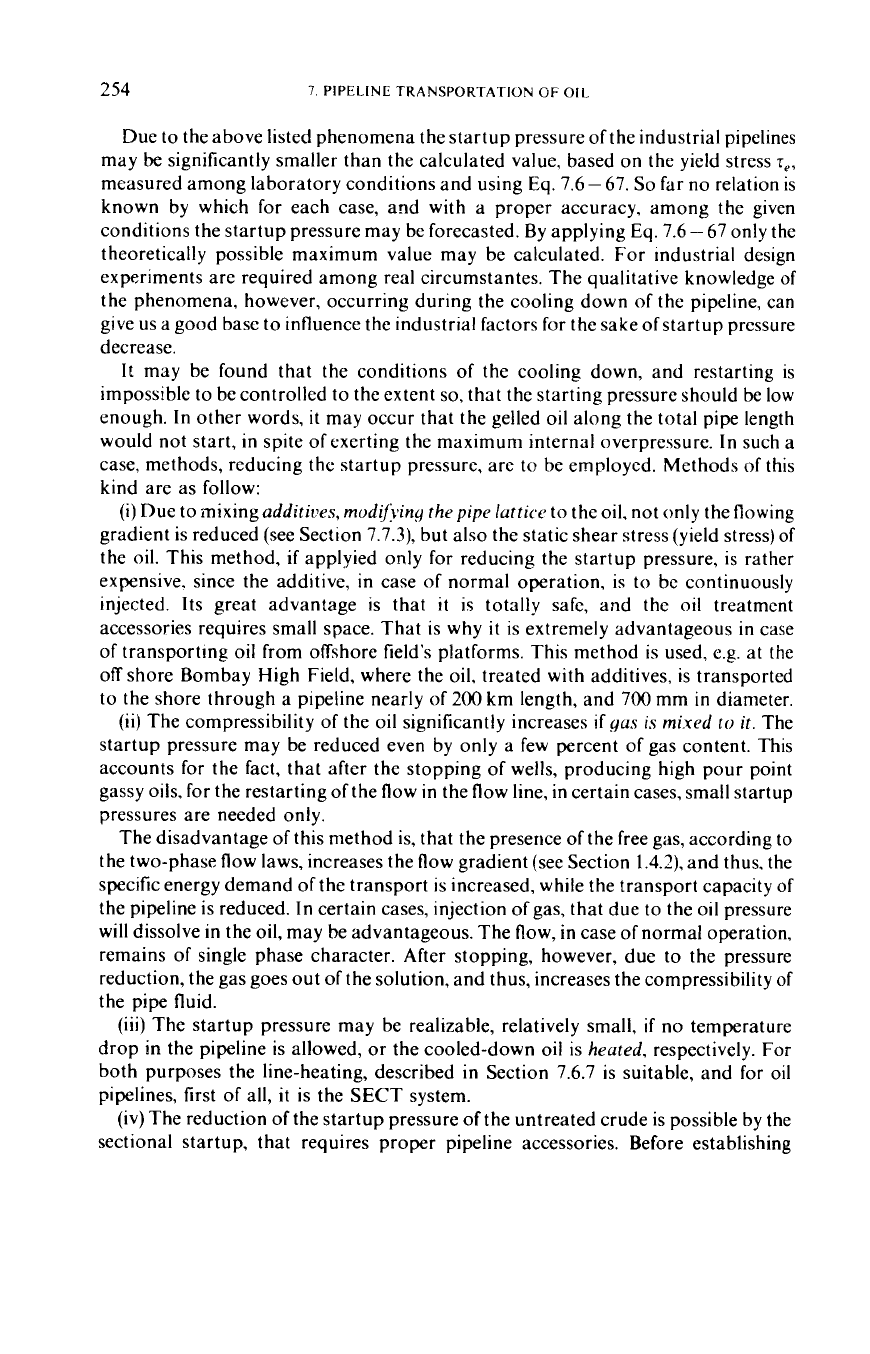
254
7
PIPELINE
TRANSPORTATION OF
OIL
Due to the above listed phenomena the startup pressure of the industrial pipelines
may
be
significantly smaller than the calculated value, based on the yield stress
T~,
measured among laboratory conditions and using Eq.
7.6
-
67.
So
far no relation is
known by which
for
each case, and with a proper accuracy, among the given
conditions the startup pressure may be forecasted.
By
applying Eq.
7.6-67
only the
theoretically possible maximum value may be calculated.
For
industrial design
experiments are required among real circumstantes. The qualitative knowledge
of
the phenomena, however, occurring during the cooling down of the pipeline, can
give us a good base
to
influence the industrial factors
for
the sake of startup pressure
decrease.
It
may be found that the conditions of the cooling down, and restarting is
impossible to be controlled
to
the extent
so,
that the starting pressure should be
low
enough.
In
other words,
it
may occur that the gelled oil along the total pipe length
would not start,
in
spite of exerting the maximum internal overpressure.
In
such a
case, methods, reducing the startup pressure, are to be employed. Methods of
this
kind are as follow:
(i)
Due to mixing
additives,
modifving
the
pipe
lattice
to the oil, not only the flowing
gradient is reduced (see Section
7.7.3),
but also the static shear stress (yield stress) of
the oil. This method,
if
applyied only
for
reducing the startup pressure, is rather
expensive. since the additive,
in
case of normal operation, is to be continuously
injected. Its great advantage is that
it
is totally safe, and the oil treatment
accessories requires small space. That is why
it
is extremely advantageous
in
case
of transporting oil from offshore field’s platforms. This method is used, e.g. at the
off shore Bombay High Field, where the oil, treated with additives, is transported
to the shore through a pipeline nearly of
200
km length, and
700
mm
in
diameter.
(ii)
The compressibility of the oil significantly increases
if
gus
is
mixed to
it.
The
startup pressure may be reduced even by only a few percent of gas content. This
accounts for the fact,
that
after the stopping of wells, producing high pour point
gassy
oils,
for the restarting of the flow in the flow line, in certain cases, small startup
pressures are needed only.
The disadvantage of this method is, that the presence of the free gas, according to
the two-phase flow laws, increases the flow gradient (see Section
1.42).
and thus. the
specific energy demand of the transport
is
increased, while the transport capacity of
the pipeline is reduced. In certain cases, injection
of
gas, that due to the
oil
pressure
will dissolve in the
oil,
may be advantageous. The flow, in case of normal operation,
remains of single phase character. After stopping, however, due to the pressure
reduction, the gas goes out of the solution, and thus, increases the compressibility of
the pipe fluid.
(iii)
The startup pressure may be realizable, relatively small,
if
no temperature
drop in the pipeline is allowed,
or
the cooled-down oil is
heuted,
respectively. For
both purposes the line-heating, described in Section
7.6.7
is
suitable, and for oil
pipelines, first of all,
it
is the SECT system.
(iv)
The reduction
of
the startup pressure of the untreated crude is possible by the
sectional startup, that requires proper pipeline accessories. Before establishing