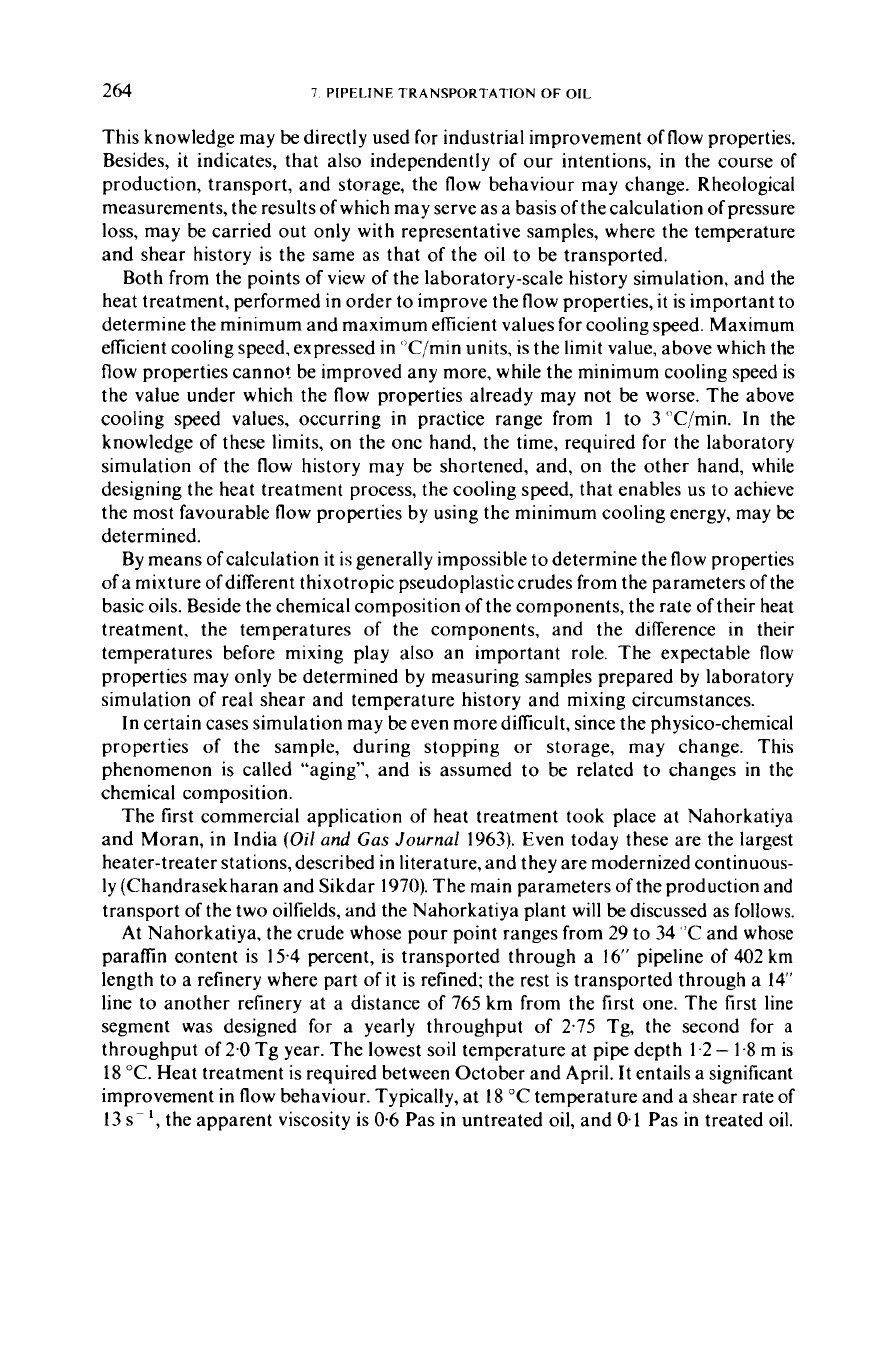
264
7
PIPELINE TRANSPORTATION
OF
OIL
This knowledge may
be
directly used for industrial improvement of flow properties.
Besides,
it
indicates, that also independently of our intentions, in the course
of
production, transport, and storage, the flow behaviour may change. Rheological
measurements, the results of which may serve as a basis of the calculation of pressure
loss,
may be carried out only with representative samples, where the temperature
and shear history is the same as that of the oil to be transported.
Both from the points of view of the laboratory-scale history simulation, and
the
heat treatment, performed in order to improve the flow properties,
it
is important to
determine the minimum and maximum efficient values for cooling speed. Maximum
efficient cooling speed, expressed
in
"C/min units, is the limit value, above which
the
flow properties cannot be improved any more, while the minimum cooling speed is
the value under which the flow properties already may not be worse. The above
cooling speed values, occurring in practice range from
1
to 3"C/min.
In
the
knowledge of these limits, on the onc hand, the time, required
for
the laboratory
simulation of the flow history may be shortened, and, on the other hand, while
designing the heat treatment process, the cooling speed, that enables us to achieve
the most favourable flow properties by using the minimum cooling energy, may be
determined.
By means of calculation
it
is generally impossible to determine the flow properties
of a mixture of different thixotropic pseudoplastic crudes from the parameters of the
basic oils. Beside the chemical composition
of
the components, the rate of their heat
treatment. the temperatures of the components, and the difference in their
temperatures before mixing play also an important role. The expectable flow
properties may only be determined by measuring samples prepared by laboratory
simulation of real shear and temperature history and mixing circumstances.
In
certain cases simulation may be even more difficult, since the physico-chemical
properties
of
the sample, during stopping
or
storage, may change. This
phenomenon is called "aging", and is assumed to be related to changes
in
the
chemical composition.
The first commercial application
of
heat treatment took place at Nahorkatiya
and Moran, in India
(Oil
and
Gas
Journal
1963).
Even today these are the largest
heater-treater stations, described
in
literature, and they are modernized continuous-
ly
(Chandrasekharan and Sikdar
1970).
The main parameters of the production and
transport of the two oilfields, and the Nahorkatiya plant will
be
discussed as follows.
At
Nahorkatiya, the crude whose pour point ranges from
29
to
34
"C
and whose
paraffin content is
15.4
percent, is transported through a
16"
pipeline of
402
km
length to a refinery where part of
it
is refined; the rest is transported through a
14'
line to another refinery at a distance
of
765
km from the first one. The first
line
segment was designed for a yearly throughput of
2.75
Tg, the second
for
a
throughput of
2.0
Tg year. The lowest soil temperature at pipe depth
1.2
-
1.8
m
is
18
"C. Heat treatment is required between October and April.
It
entails a significant
improvement in flow behaviour. Typically, at
18
"C temperature and a shear rate of
13
s-
I,
the apparent viscosity is
06
Pas in untreated oil, and
0.1
Pas in treated oil.